Spinning
Oerlikon focuses on complete solutions for the Central Asian textile industry
Oerlikon Polymer Processing Solutions offers complete solutions ranging from polycondensation plants to texturized yarns, accompanied by automation and digital solutions. The supply of all process steps from a single source ensures a harmonised technology that guarantees the high quality of the yarn produced.
"The Uzbek market continues to develop well. The country has been known for decades for very good products in the cotton sector. However, market players are increasingly recognising the advantages and necessity of synthetically produced yarns and fibres. With our product portfolio, we offer precisely the technologies that the Uzbek textile industry needs to meet its requirements in the coming years,’ explains André Wissenberg, Head of Marketing, Corporate Communications and Public Affairs. "It is important to us that we always make a contribution to sustainability with our technology solutions. Be it by increasing energy efficiency with each new generation of machines or by processing new materials,’ Wissenberg continues. Oerlikon is proud of the fact that the company has been offering innovative solutions for the textile industry under the e-save sustainability label for 20 years and has saved over 15 million tons of CO2 thanks to the machines and systems developed and installed on the market during this time.
Sustainable processes for POY and FDY productionPOY yarns are the raw material for a wide range of fashion, sports, functional and home textiles. They are then textured and, at around 40%, make up the largest proportion of manmade fiber yarns produced worldwide. Oerlikon Barmag's WINGS POY technology guarantees outstanding yarn quality with high productivity and energy efficiency. With its particularly gentle yarn path, WINGS ensures that the yarn remains as high-quality as it was when it left the spinning mill. The minimized deflection angle has a positive effect on yarn evenness, yarn tension, CV% values and thus on dyeability. A perfect package structure ensures excellent further processing properties in downstream processes such as texturing.
Fully drawn FDY yarns are processed into textile surfaces without further finishing. They are used wherever textiles need to fall smoothly or glide. Oerlikon Barmag's WINGS concept for the FDY process stands for optimised production processes, low waste rates and energy consumption reduced by around 30 percent with the highest yarn quality. The technology can be used in the FDY process for polyester and polyamide.
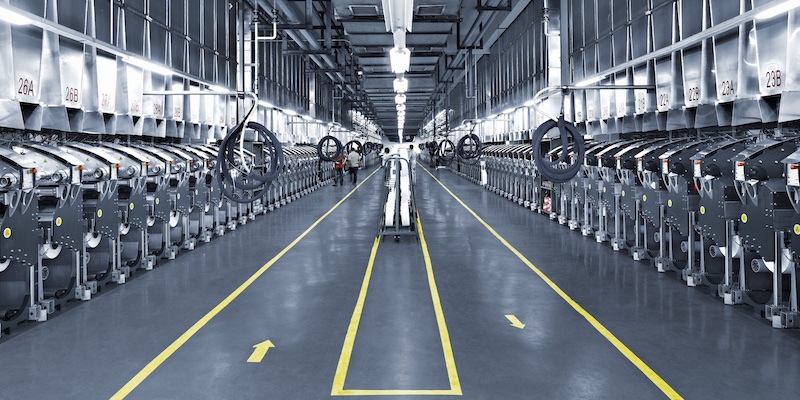
DTY yarns - uncompromising quality and maximum flexibility
Texturized yarns can be used for a wide range of applications. They are used in clothing, home textiles, the automotive industry and many other areas. Oerlikon Barmag offers a wide range of different DTY machine configurations for the efficient and sustainable production of high-quality texturized yarns from various polymers, from polyester and polyamide to polypropylene, PLA and PTT. The modular DTY machines, equipped with sophisticated components, expertise and proven technology, enable the production of texturized yarns for excellent further processing in downstream processes at optimum OPEX costs.
Sustainable production of staple fibers with EvoSteam
The EvoSteam process from Oerlikon Neumag stands for both resource-efficient staple fiber production and excellent fiber quality. It offers impressive savings in energy, water and raw material consumption as well as a reduction in operating costs (OPEX) and the CO2 footprint.
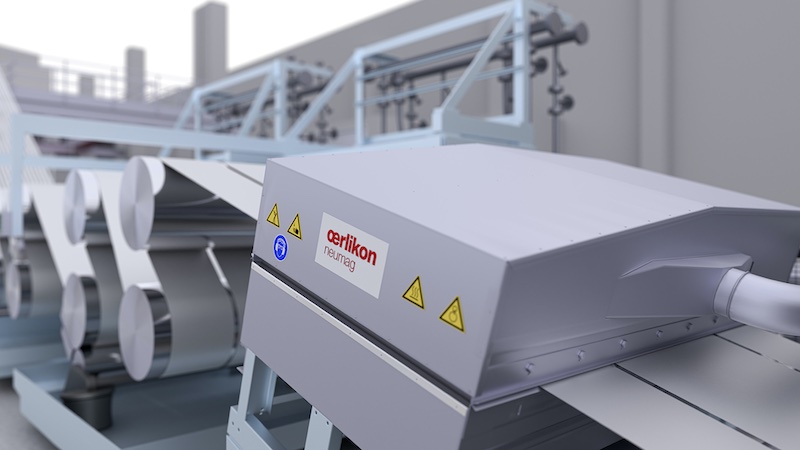
New bicomponent BCF yarn for the carpet market
Quality, efficiency and performance - with its latest development in the field of bicomponent yarns for carpet production, Oerlikon Neumag is meeting the carpet market's demand for new innovative BCF yarns. ‘The new BICO BCF yarn is characterised by a richer and higher volume while at the same time significantly reducing the consumption of raw materials in carpet production,’ explains Oerlikon Neumag BCF Sales Director for Uzbekistan Arnd Luppold. At the exhibition stand, interested parties can see sample yarns and carpets, find out more about the product range and have in-depth discussions with the experts about the advantages of BICO BCF yarn in various applications.