Spinning
Sustainable and efficient - Barmag's technologies for the Vietnamese textile industry
Trade visitors will have the opportunity to get a comprehensive picture of the complete solutions on offer, which range from polycondensation systems to spinning and texturing through to digital solutions. The provision of all process steps from a single source ensures a harmonized technology whose design guarantees the high quality of the yarn produced.
Another focus is on sustainability. Together with partners such as Oerlikon Barmag Huitong Engineering (OBHE) and BB Engineering (BBE), the company presents specific concepts that include mechanical and chemical technologies for bottle recycling as well as for textiles, biopolymers and the circular economy. With the sustainability label e-save, the company has been offering innovative solutions for the textile industry for 20 years, hence setting standards for a more environmentally friendly future.
Recycling - the path to a sustainable future
OBHE's homogenizer enables the thermomechanical recycling of polyester waste. The well-known and commercially available raw materials such as bottle flakes, post-industrial waste and film waste are processed into high-quality PET products. The OBHE Homogenizer ensures constant polymerization conditions with an optimized residence time spectrum. Hence, the desired increase in viscosity can be specifically influenced and an excellent and homogeneous melt quality can be produced. The production of high-quality and defined rPET products with further processing of the melt to POY and FDY in the direct spinning process or for the production of PET chips is thus guaranteed and has already been proven by installed systems on the market. The OBHE homogenizer provides the customer with a flexible system for thermomechanical recycling of polyester waste.
With the flexible compact spinning system VarioFil® R+ from BBE, PET bottle granulate and PET waste produced during start-up can be recycled and processed directly back into POY. The sustainable machine concept allows a high degree of product flexibility, including the production of spun-dyed yarn. The turnkey spinning line is also ideal for producers who manufacture small batch sizes or specialized products.
"From Waste to Value" - this is what BBE's VacuFil PET recycling system achieves. It is specially designed for the high-quality processing of textile waste. The patented technology is unique and is based on years of experience in extrusion, filtration and spinning: it combines gentle large-area flitration with targeted IV regulation for consistently excellent rPET melt quality, comparable to virgin material. A wide range of input materials can be processed: in addition to the usual bottle flakes, VacuFil is particularly suitable for production waste from the spinning mill, from start-up lumps and yarn to unmixed fabrics, which can also include post-consumer waste. The patented key component Visco+ , a liquid-state polycondensation system, quickly and reliably removes volatile impurities and automatically regulates the IV. There are also various options for further processing of the treated melt. For example, the melt can be fed into the main melt stream, processed into chips via palletization or flow directly back into the spinning mill. The VacuFil recycling system can therefore be designed modularly and flexibly to meet customer requirements.
DTY yarns - maximum flexibility and uncompromising quality
Whether for home textiles, in the clothing industry or in the automotive sector - the possible applications for texturized yarns are virtually unlimited. Oerlikon Barmag offers a wide range of DTY machine configurations for the efficient and sustainable production of high-quality textured yarns from various polymers such as polyester, polyamide, polypropylene, PLA and PTT. Thanks to sophisticated components, comprehensive know-how and tried and tested technology, the modular DTY machines - whether manual or automatic - produce texturized yarns that are ideal for downstream processes and ensure optimum OPEX costs.
JeTex® Air texturizing from BBE enables a broad and flexible product portfolio
The Oerlikon Barmag subsidiary also offers a solution for texturing. The JeTex air texturing system perfectly complements the Oerlikon Barmag DTY system and enables the customer's product portfolio to be expanded to include high-quality ATY based on POY and FDY for a wide range of textile applications. The centerpiece of the system is the texturing box specially developed by BB Engineering. Alongside many other state-of-the-art components from Oerlikon Barmag, it ensures gentle yarn treatment with reliable texturing effects as well as production efficiency in terms of OPEX, handling and speed.
Particularly smart: JeTex® is not only available as a complete system, but also as a retrofit variant for existing DTY systems from Oerlikon Barmag. This allows customers to expand or convert their product portfolio to include ATY at comparatively short notice and at low cost.
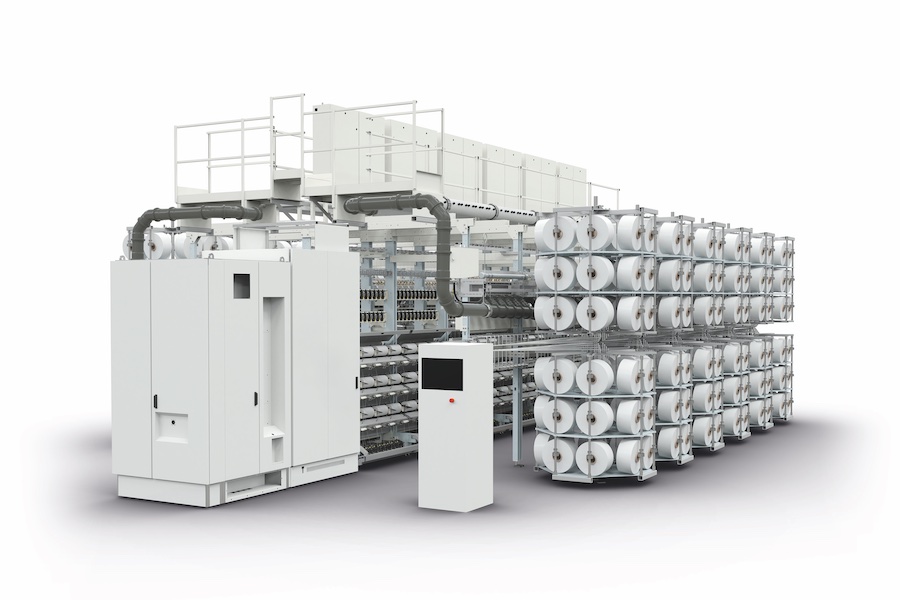
Bi-shrinkage yarns - from niche to standard
Bi-shrinkage yarns (BSY/ITY) have established themselves from a niche product to a standard yarn with a relevant market share in further processing, be it knitting, weaving or flax. The special yarn properties are visible in the end product, e.g. in crêpe or georgette fabrics or in ladies' outerwear. Oerlikon Barmag offers one- or two-stage solutions for the production of these specialty yarns. The single-stage solution is based on the tried and tested Barmag WINGS FDY concept, while the two-stage solution is based on eFK texturing machine technology. Both score over conventional technologies in terms of energy savings, production speed, process flexibility and quality.
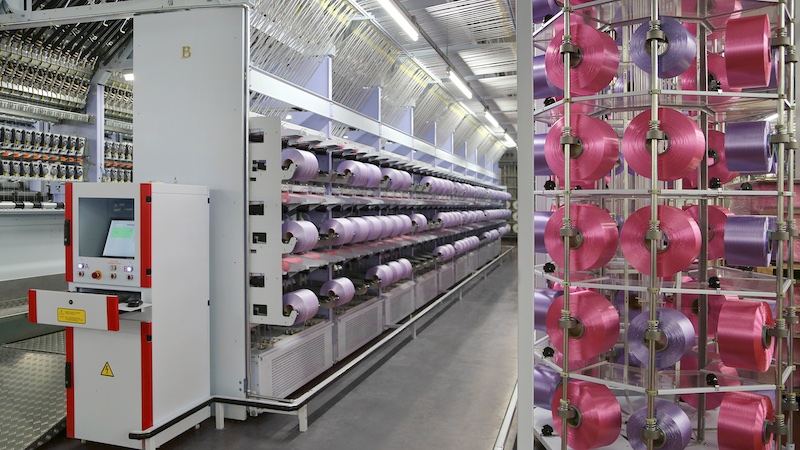
EvoSteam - innovative production of staple fibers
The innovative EvoSteam process from Oerlikon Neumag is the future of more sustainable staple fiber production. It impresses with considerable savings in energy, water and raw material consumption and thus leads to a significant reduction in operating costs (OPEX) and the CO2 footprint - while at the same time providing excellent fiber qualities for downstream processes.
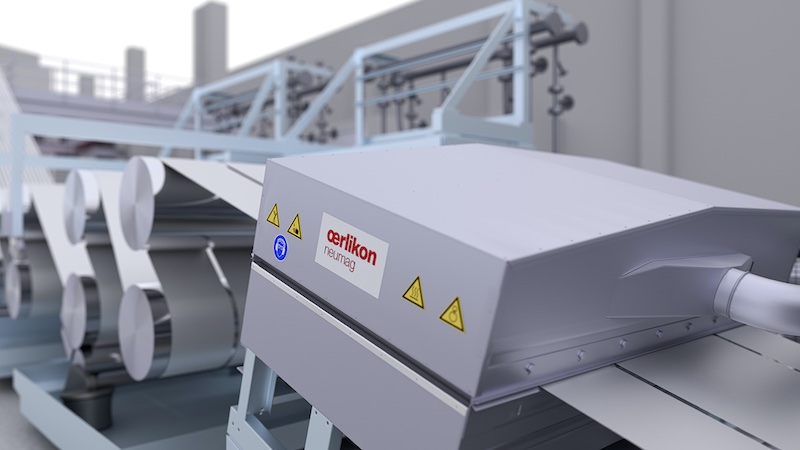