Spinning
Reifenhäuser extrusion lines provide carbon footprint calculation for more sustainable and economical production
Dr. Tim Pohl, Director Sustainability and Business Development at the Reifenhäuser Group, explains: "The Carbon Footprint Dashboard shows the different emission sources over the production period. In the basic version, assumptions are made about the carbon footprint of the raw materials used and the calculation is based on the energy mix of Europe, for example. This is sufficient to determine initial potential for carbon footprint reduction. If more precise information is required, we can customize the calculation according to local conditions. Such a calculation becomes exciting when in-house recycled material is used."
Carbon footprint calculation for manufacturing companies is quite complex and starts with the different methods of calculation - at the company level, but also at the product level. The corporate carbon footprint (CCF) balances the CO2 footprint for the entire company - from energy procurement to production to the vehicle fleet. The product carbon footprint (PCF) records all CO2 emissions that occur along the life cycle of a product, i.e. from raw materials to production and use to disposal.
Manufacturers of films and nonwovens can therefore approach the topic of calculation "bottom-down" via a corporate carbon footprint, or they can do it "bottom-up" via a product carbon footprint for each of their products. The latter is ideal if a broad product portfolio with different raw materials and recycled content is processed. For this purpose, a customer-specific carbon footprint dashboard can be created in Reifenhäuser's ExtrusionOS software solution.
From an economic point of view, the carbon footprint calculation is worthwhile in any case: Producers can show the carbon footprint to third parties and thus certify a particularly sustainable product series, for example. This opens up new sales markets and increases economic success. In addition, the savings in energy and raw materials pay off, especially in view of the current high purchase prices.
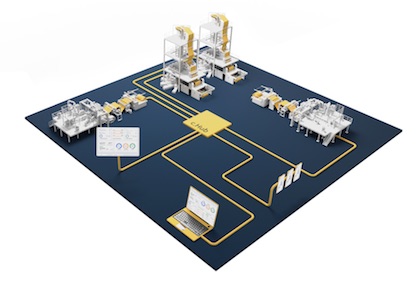
Carbon footprint of a Reifenhäuser extruder
The Reifenhäuser Group has been following the path of the corporate carbon footprint for 10 years now. The machine manufacturer is energy certified according to ISO 50001 and reduces its emission sources every year. This year, for example, this includes the installation of a new photovoltaic system with which Reifenhäuser can produce more than 600,000 kWh of electricity and save approximately 175,000 kilograms of CO2 equivalents.
In addition, the PCF of components, such as screws and barrels, and of entire extruders was determined. One finding is that emissions during the production of the line components are significantly lower than emissions during the use phase. For example, the production of a 120 extruder generates a calculated one-time emission of around 27,000 kilograms of CO2 equivalents. In contrast, the operation of the extruder causes around 3.5 million kilograms of CO2 equivalents through electricity consumption over the course of ten years. In this case, the manufacturing process causes less than one percent of the PCF along the life cycle. By contrast, 99 percent is generated during the use of the extruder - so the leverage for reducing emissions is much greater at this stage. For extruder operators, investing in energy-efficient technologies and subsequent energy-saving measures is therefore doubly worthwhile - both the wallet and the environment benefit.
Carbon Footprint Dashboard at K 2022:
Reifenhäuser main booth: Hall 17 / C 22
More information and illustrations on the subject of sustainability
can be found at: www.reifenhauser-sustainability.de