Spinning
Airbag yarns on the rise
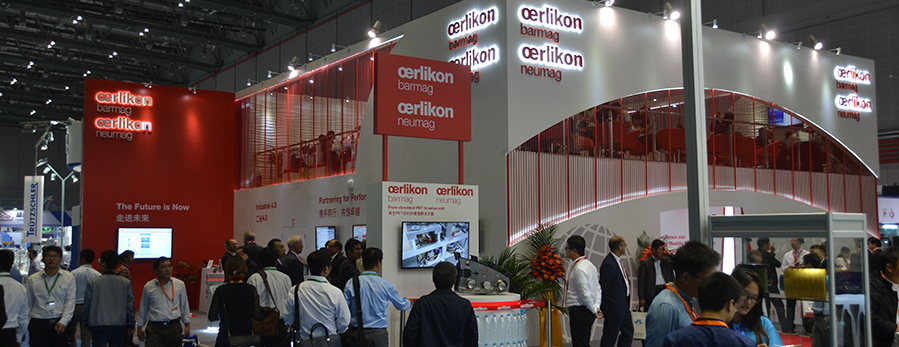
Automotive sector with growth potential
Industrial yarn producers are increasingly perceiving the airbag yarn segment as a growth market. To this end, four projects for manufacturing airbag yarns from polyamide 6.6 (PA6.6) and polyester (PET) supplied by systems builder Oerlikon Barmag have been successfully commissioned in the past 12 months alone. The systems – installed at well-known yarn manufacturers in North America and China – cover titer ranges of between 235 and 700 dtex for PA6.6, and between 470 and 550 dtex for PET.
The systems concept offers the highest level of flexibility: the proven SP4 spinning system with exchangeable melt distribution enables the conversion of the airbag yarn systems from PA6.6 to PET or vice-versa without much effort. To this end, yarn producers can react flexibly and swiftly to changing market requirements.
Market with growth potential
The reason for the increased demand for airbag yarns is the global rise of road safety requirements. Within this context, the Indian government and the Department of Road Transport and Highways, for example, have revised their vehicle safety rules and regulations. The new version, which comes into force in the fall of 2017, demands considerably greater occupant safety, particularly with regards to side and front impact. According to the estimates of numerous automobile manufacturers, compliance with these new safety rules and regulations can only be achieved with the installation of airbags.
And, according to research conducted by PCI, greater safety in vehicles is also a much-discussed topic in Latin America, which is having a positive impact on the airbag and safety belt manufacturing industry: two South Korean airbag producers have already announced investments in Central America.
The average volume of textile fibers and filaments in automobiles is around 30 kg; according to PCI Fibres, just under 19% of this is airbag yarn. This opens up a highly-profitable growth market for industrial yarn manufacturers.