Spinning
FixDye to produce recycled dope-dyed filament yarn with rPET flakes on systems of Oerlikon Barmag Huitong Engineering
Oerlikon Barmag Huitong Engineering (OBHE) supplies polycondensation plant for sustainable production
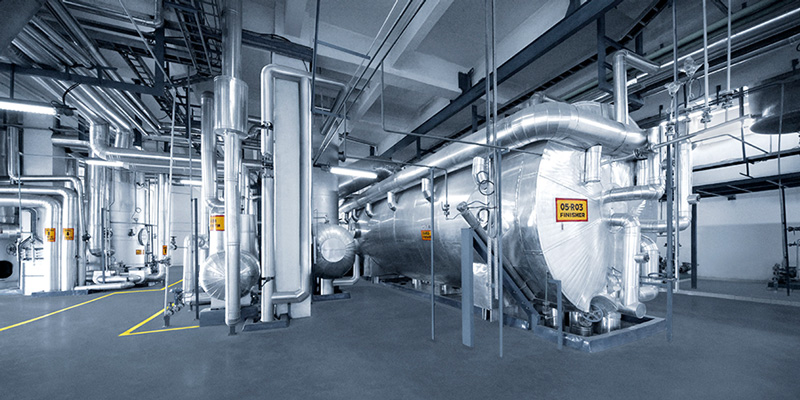
The company, based in Huai’an, China, is thus expanding its production capacities in melt preparation, the production stage upstream of the spinning mill. This will not only allow FixDye to better influence yarn quality, but also to keep an eye on the supply chain of its products, regardless of external influences. This is an unbeatable advantage when it comes to the ambitious goals of the circular economy.
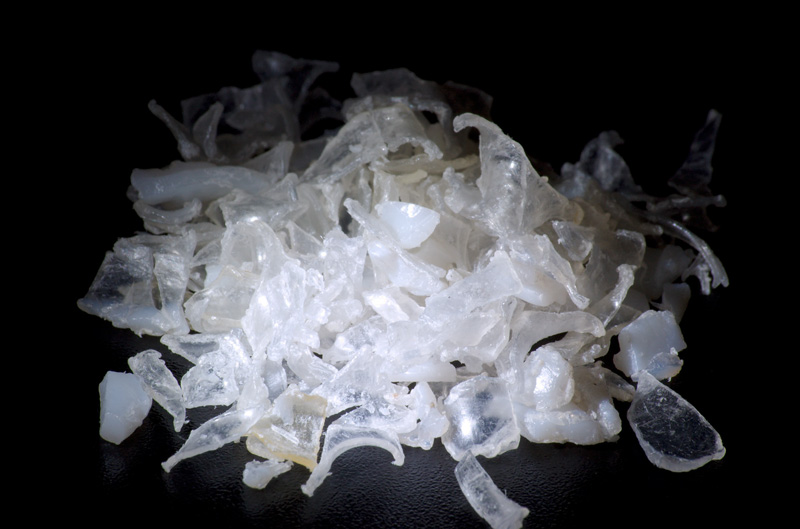
The plant with a capacity of 3 x 180 tons per day of recycled bottle flakes for textile filament yarn is a clear commitment to the sustainable textile industry. From mid-2025, it will mainly produce FDY and POY/DTY for the European and US markets. The yarns produced are spun-dyed for ecological reasons, zero water dyeing method.
With its sustainability concept, FixDye is a pioneer in the textile industry. Certified by numerous recognized institutes such as GRS, BSCI and OEKO-TEX, the company produces everything from recycled melts to textile surfaces for well-known international textile and sporting goods manufacturers. "In the medium term, FixDye also wants to offer materials produced using the Textile-2-Textile recycling process," explains Ivan Ye, CMO of FixDye. "Confidence in the reliability of the highly efficient systems and the sustainable, energy-saving concept were the decisive aspects in choosing OBHE as the supplier of the polycondensation system," adds General Manager Kevin Wang.