Spinning
Highest precision for high-viscosity media
Efficiency in mastering viscous media – the GA series
When applying hot-melt adhesives, the focus lies above all on the evenness of the application. However, precise metering not only presupposes the fast and reproducible setting of an operating point, but also low-pulsation feeding of the conveying medium. Supplementing the proven GM series, Oerlikon Barmag has now developed the GA range for conveying higher-viscosity media. The GA series is available for conveying volumes of between 1.25 and 30 cm³/rev (0.6-144 l/h). It has been designed for pressures of up to 200 bar, for viscosities of up to 1,500 Pas as well as for temperatures of up to a maximum of 225 °C. With this new program of pumps, Oerlikon Barmag offers tailor-made solutions for all applications for which precisely-defined, even metering is absolutely essential.
Conveying and metering using a single unit – the drum pump
The drum pump is designed especially for conveying and metering high-viscosity materials such as adhesives, silicones, etc., from drums and other large containers and for pressures of up to 250 bar. Thorsten Wagener, the sales employee responsible for pumps used in industrial and chemical applications comments: “The drum pump not only conveys high-viscosity materials from the drum, it also meters the medium to the mixing head without any additional interim stops and with the customary volumetric efficiency.” In close agreement with the customer, the gear pump and drum follow-up plate are harmonized in such a way as to ensure that the plate can effortlessly reach the bottom of the container, hence guaranteeing a very small amount of residue totaling <1%. This has a positive impact on both the materials costs and the production process.
Working under high pressure
In high-pressure technology, conveying small volumes with low viscosities is a particular challenge. Specifically for this application, Oerlikon Barmag has expanded the GM series with round plate package to include an option for the pressure build-up capacity. This multi-stage pump is available for conveying volumes of between 0.05 and 20 cm³/rev and guarantees the generation of operating pressures even at low viscosities (for example, 250 bar, 100 mPas). To this end, higher volumetric efficiencies or a larger useable speed range can be achieved. The robust gear metering pump ensures continual low-pulsation operation. Hence, high-pressure applications conveying minimum flow-through rates (for example, 0.5g – 1.5g/sec.) can also be covered for the very first time. For the manufacturers of PUR molded parts, block foams, refrigeration unit insulation and sandwich panels, this means consistent process stability and low investment costs.
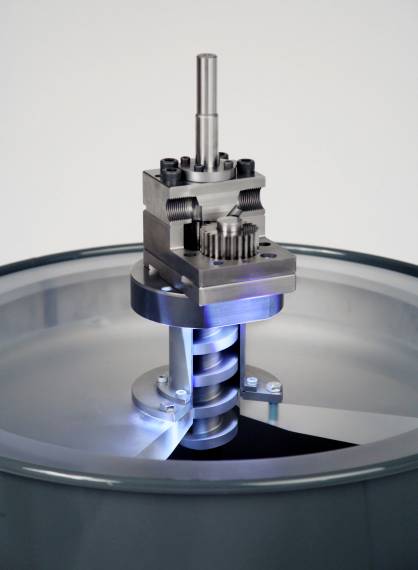
One for all – high-speed metering made easy
The new high-speed metering pumps have been developed especially for lightly-lubricating and abrasive media. With their enlarged speed range (30 - 500 rpm), they cover a large application area for which several pumps of varying sizes have had to be used to date. For the manufacturer, this means less work when switching production and smaller spare parts inventories. The compact construction of the pump (ø65 mm) reduces the space required in the machine and the low weight (1.4 kg) keeps the load as low as possible, which in turn has a positive impact on the construction of the machine. The external lifetime-lubricated ball-bearings ensure that the pump is not only very durable, they also do not come into contact with the respective product.