Research & Development
Wood wool instead of crude oil: Scientists at TU Dresden develop sustainable biocomposites
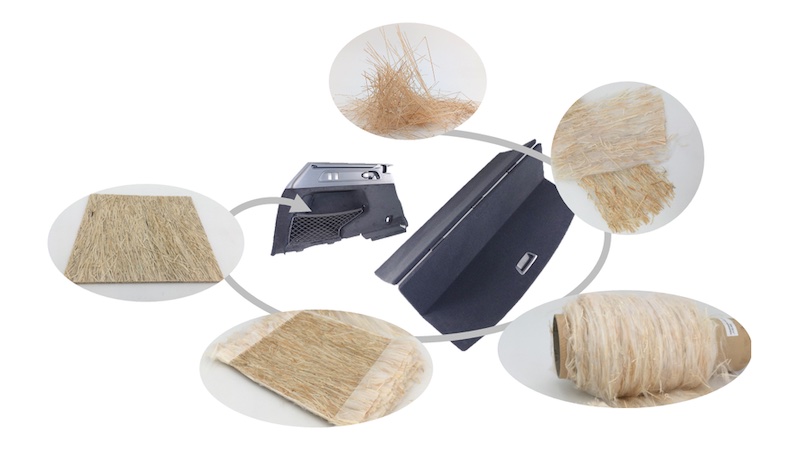
Wood wool is used in everyday areas, for example as a cushioning filling and padding material in packaging, as an ignition aid, but also in horticulture and animal husbandry. It also has a load-bearing function in lightweight panels.
Due to its lack of malleability and low strength, conventional wood wool is currently not used beyond the areas mentioned. With the production of lignowool composites, the TUD scientists at the Chair of Wood Machinery and High Performance Materials Technology, together with the Institute of Textile Machinery and Fiber Materials Technology (ITM) and various practice partners, want to open up a new field of application for wood wool. In the first phase of the project, the technological feasibility of the composite materials was demonstrated. Now the knowledge gained is being implemented. Technical wood wool with previously unattained properties is created from solid wood by means of incisions made in a targeted manner and precise cutting. This is then combed with biopolymer fibers in a carding machine and thus structured. Further textile-technical process steps lead to pressable blanks, the so-called wood wool thermoplastic tapes. In the project, these are processed into prototypes for the above-mentioned automotive applications.
"The technical wood wool we process retains its typical wood properties. It is more stable than the previously established wood wool and has a high formability. It is also reproducible and can be processed using textile technology," explains project manager Sebastian Siwek. "By developing composites, we are closing a gap in the field of wood-based materials and increasing resource efficiency through a more holistic utilization of wood."
The project team is planning an industry-oriented pilot plant to test the process for broad application, further develop the wood wool manufacturing process and improve the combination of the various processing steps.
"Lignowool_2" will run for two and a half years and is funded by the Federal Ministry of Food and Agriculture. The project sponsor is the Agency for Renewable Resources (Fachagentur für Nachwachsende Rohstoffe e.V.).