Other suppliers
Microfactory for filter bags developed in Sweden
As a fully automated system, it promises to revolutionise the production of woven or nonwoven needlefelt filter bags which until now have rather surprisingly been assembled and finished in laborious and time-consuming cut and sew operations by third party suppliers.
The microfactory’s configuration is based on two separate interconnecting modules – the Smart Filter Line (SFL) and the Filtermaster 2.0.
The SFL handles the fabric feeding from rolls and its folding prior to seam construction, which can either be by automatic sewing, welding or with sewing and taping, depending on specifications. Very rapid changeover of the modular seaming methods can be achieved during product changes. The specific size of the now fully-tubular fabric is then precisely cut to size for each individual unit and further folded ready to be fed into the Filtermaster 2.0.
The Filtermaster 2.0 then automatically attaches the reinforcement, bottom and snap rings onto the filter tube with a second Juki sewing head on a robotic arm, to form the fully finished filter bag ready for packaging.
“The automation of these essential steps is the real innovation we’ve achieved with this microfactory, eliminating the need for the many hours of labour-intensive manual work that has previously been necessary,” says ACG Kinna Automatic CEO Christian Moore. “The output is 120 finished filter bags per hour and the entire configuration is guided by precise automatic steering and alignment, with quality control handled by the latest high-definition vision cameras.
“This type of automation is the way forward, not just for filter bags, but for many industries who heavily rely on such consumables in their operations,” he adds. “It makes sound economic and operational sense for the major filtration players to have such lines close to their individual operations – wherever they may be in the world – and to be self-sufficient and in control of their production, for just-in-time, guaranteed delivery.”
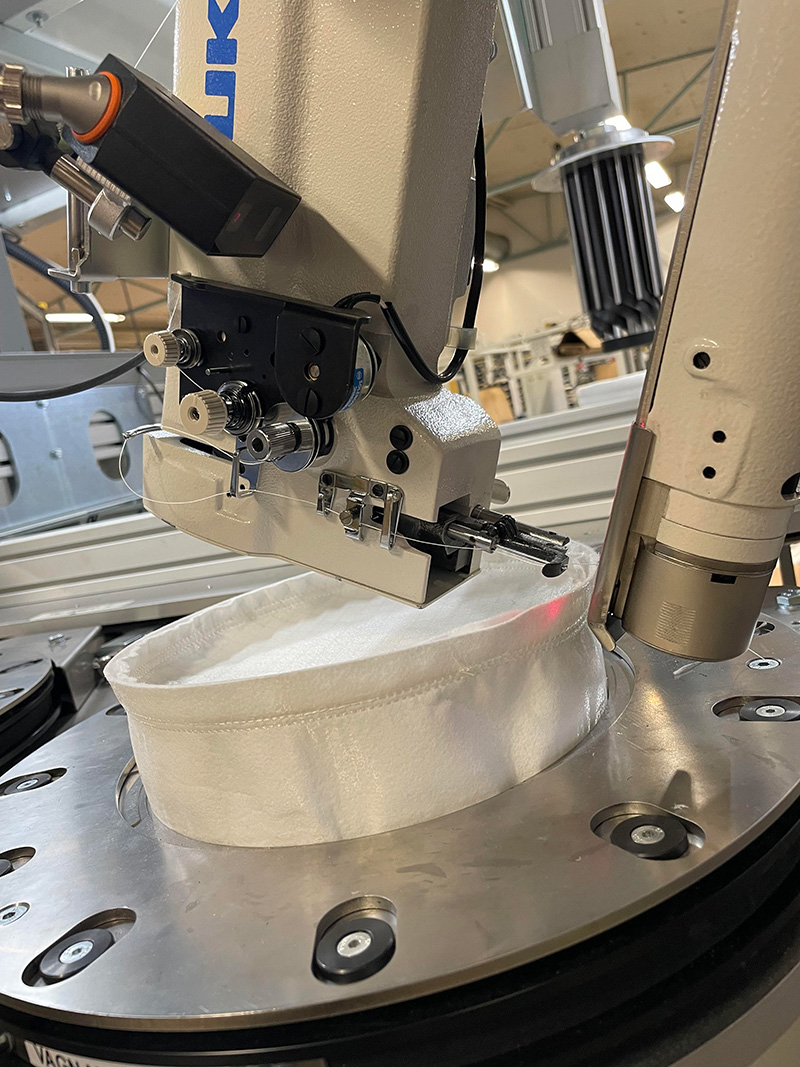
Under the radar
Filter bags are employed in a wide range of industrial processes and while they may be largely under the radar as products, they represent a pretty significant percentage of overall technical textiles production.
They are used extensively, for example, in foundries, smelters, incinerators, asphalt plants and energy production plants. Other key manufacturing fields – often where dust is generated – include the production of timber, textiles, composites, waste handling and minerals, in addition to chemicals, food production, pharmaceuticals, electronics and agriculture.
As a further example of the scale of the industry and the high volumes of fabrics involved, one supplier has delivered a single order of 30,000 filter bags to be used for flue gas cleaning at a European power plant. The bags can also be anywhere up to twelve metres in length and frequently have to be replaced.
Many fields
“I continue to be surprised by the many fields of industry our TMAS members serve, and where automation can make the difference,” said TMAS Secretary General Therese Premler-Andersson. “The innovations coming from our companies are far-ranging and characterised by an advanced grasp of automation techniques and the need for more sustainable processing methods that is being demanded by their customers. There will be much more of this in the coming years.”