ITMA Asia + CITME 2024
Monforts is 140 and looking to the future
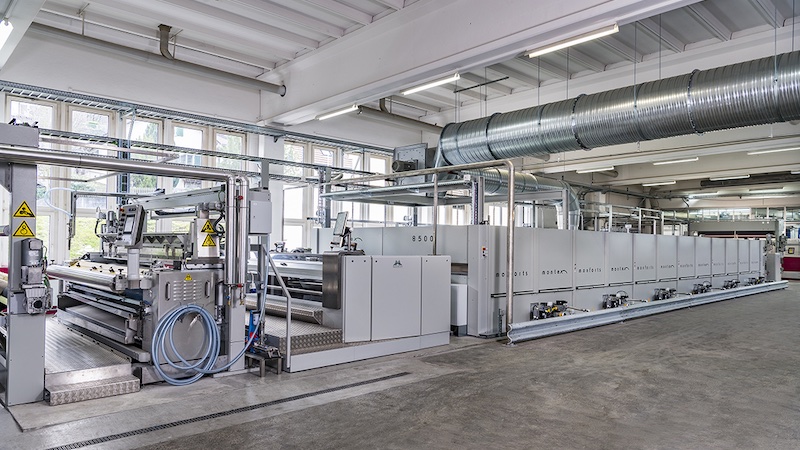
Under the motto, ‘140 Years of Performance, Innovation and Partners’, Monforts is looking forward to further celebrating this milestone with its representatives and customers at the forthcoming ITMA Asia + CITME exhibition in Shanghai from October 14-18, in Hall 5 at stand C09.
“We have moved over the many decades through mechanical and steam-powered technologies to the first mass production lines, electronic drives, special machine construction and highly modular machines,” observes Monforts Managing Director Gunnar Meyer. “Now we are truly in the digital age, and we are committed to investing in the digitalization of our technology, with concepts which assure an overall quality control and energy monitoring.”
International outlook
The first Monforts machines were mechanical napping units for raising the surfaces of cotton fabrics, providing softness and warmth and adding value. By 1893, Monforts 24-roller napping machines were drawing appreciative crowds at the World Fair in Chicago – establishing international trade networks was paramount to the company from the outset.
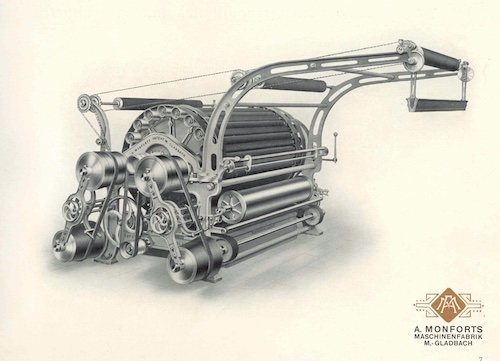
In 1897, August Monforts established an iron foundry equipped with hydraulic casting machines, by which time the company employed 1,200 people. This was followed by the introduction of semi-automatic manufacturing tools – an area in which Monforts achieved a number of firsts, such as the single-spindle lathe which became a big export hit in the late 1930s due to its unique and unmatched precision.
Overseen by successive four generations of the Monforts family, the company’s range of textile machines has been significantly expanded based on decades of accumulated know-how and a dominant position in fabric finishing technologies has been established.
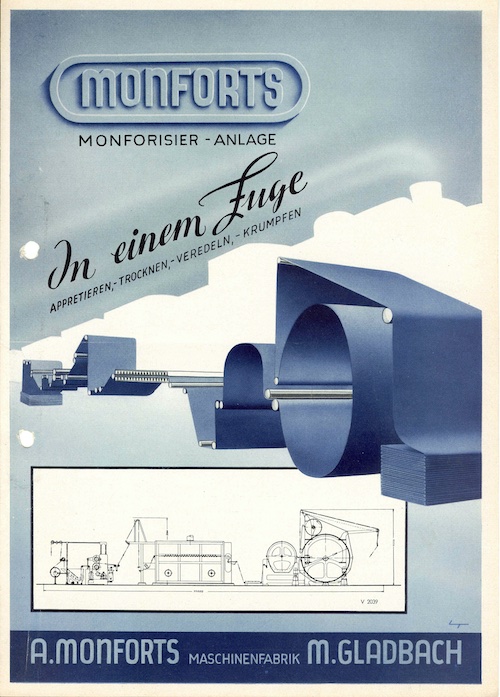
Since 2013, Monforts has been a member of the CHTC Fong’s Group, today one of the world’s largest textile machinery manufacturers.
Industry standard
Monforts Montex stenters – for processes such as drying, stretching, heat-setting and coating – are now the industry standard for the fabric finishing industry, not only in the sectors of denim and home textiles, but also in the field of technical textiles, with numerous patents registered over the course of the decades for premium quality and a number of advantages in terms of production throughput and especially in energy efficiency and savings. The other key technologies in the Monforts range include DynAir relaxation dryers, Thermex continuous dyeing ranges, Monfortex compressive shrinking ranges and Montex®Coat and coaTTex coating units.
ATC
Since its opening in 2013, the €2.5 million Monforts Advanced Technology Centre (ATC) in Mönchengladbach has proved an invaluable resource to customers for achieving new standards in fabric finishing.
Over an area of 1,200 square metres, it houses two full finishing lines, engineered to accommodate an extremely diverse range of processes, in addition to a Thermex range for the continuous dyeing of denim and other woven fabrics, a full colour kitchen and a number of lab-scale systems for smaller batch trials.
“The ATC allows our customers to test their own textiles and technical fabrics on Monforts dyeing and finishing machines under fully confidential, real production conditions,” says Monforts Technologist Saskia Kuhlen. “Using the results from these trials, we are also able to make recommendations for improving many fabric finishes.”
Montex Austria
For over 40 years, Monforts finishing machines have been manufactured at Montex Maschinenfabrik based in St. Stefan, Austria.
“From the outset, we have specialised in all aspects of machine production, including high-precision sheet metal working, laser cutting and welding, and the pre-assembly of machines and components, along with a well-organised quality management and spare parts service,” says Montex plant manager Gert Hanzl. “We work very closely with the Monforts research and development team in Mönchengladbach to take the latest new ideas through testing and prototyping, in readiness for future series production. We are fully exploiting the many new possibilities in the continuous development of design and manufacturing methods.”
While there is standardisation in series-produced Monforts machines, Montex Maschinenfabrik is also increasingly called upon to construct bespoke machines with unique designs, according to the special needs of customers in technical textile or special textiles.
Made to last
“Our machines are built to last and known for their robustness and long service life,” concludes Gunnar Meyer. “Textile companies making major capital investments in new manufacturing lines rely on durability from our production ranges, and it’s for this reason that there are currently an estimated 2,000 Monforts machines in operation worldwide – some of which were first installed over 30 years ago.
“It would not have been possible for Monforts to have thrived for 140 years without successfully and rapidly responding to industry changes and this continues today. I would like to thank all of our dedicated staff in Germany and Austria and our many colleagues and partners around the world for their continuous contributions to ensuring our further longevity.”