Dyeing, Drying, Finishing
Expanding options at JPF with Monforts dual heating
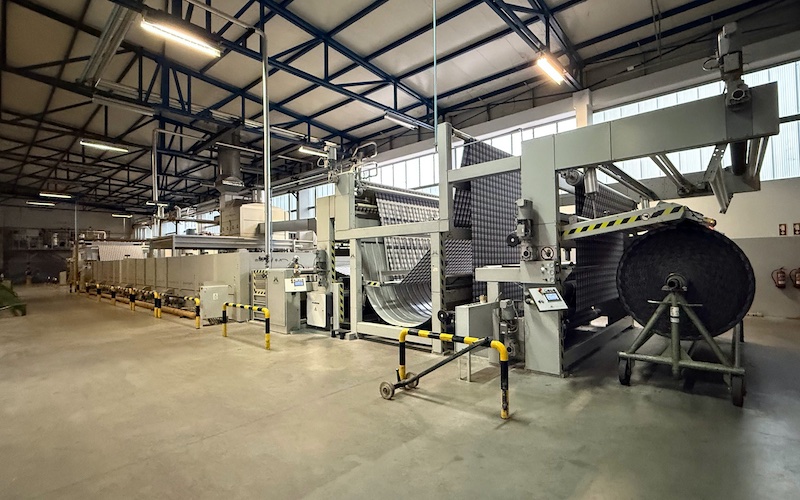
At the forefront of such advances is J Pereira Fernandes (JPF), which has recently expanded its fabric finishing plant with a purpose-built biomass-fuelled boiler room, enabling it to carry out CO2 neutral production via steam heating.
UNESCO World Heritage Site
JPF is located in Guimarães in northern Portugal, which has been listed as a UNESCO World Heritage Site since 2001, ensuring the company must operate to the most stringent environmental standards in terms of all emissions.
Vertically-integrated operations at the Guimarães site span spinning, yarn dyeing, weaving, fabric dyeing and finishing and cutting and sewing, with an annual finished fabric capacity of 5.5 million metres, primarily of 100% cotton goods for the home textiles market.
As a long-standing Monforts customer, a first Montex stenter with a working width of 3.2 metres was installed at the Guimarães site in 1987, followed by a second seven-chamber model with a working width of 3.4 metres in 2020. The company also operates a Monforts sanforizing line.
Steam or gas
With the new biomass boiler in place, Monforts has now retrofitted a dual heating unit to the most recent stenter to fully benefit from the option of operating with either steam or gas.
“We have been retrofitting dual heating units to operational Montex stenters for over a decade now and this is the third unit we have installed in Portugal recently,” says Monforts Area Sales Manager Thomas Päffgen. “It enables biomass-powered steam heating to be employed when processing at up to 160°C, with gas heating required for higher temperatures. In addition to the existing direct gas heating, the stenter frame chambers were each extended by a steam heat exchanger and vents for vapour pressure control.
Competitive advantages
“Energy costs have been seriously compromising our competitiveness with manufacturers in Asian countries and we have taken a wide range of measures to minimise consumption,” adds JPF managing director Sandra Fernandes. “We have made further adjustments to reduce energy on our yarn dyeing machines and other equipment, as well as switching to the most highly efficient motors and pumps across our machine ranges.
“In addition we have inverters everywhere and use economizers and heat exchangers wherever possible, as well as strongly controlling compressed air and steam leakage.”
All facilities at the Guimarães plant are now LED illuminated when natural light is not available and the company’s own solar energy generation provides around 50% of its electricity consumption during the daytime shift.
Know-how
Beyond all of this, however, the company’s long experience and accumulated know-how – JPF was founded initially as a weaver in 1933 and has been fully vertically integrated since 1970 – also contributes to competitive advantages.
“We dye at low temperatures and low liquor ratios and invest and focus on ‘right first time’ to avoid any returns which inevitably entail repeat production runs,” Fernandes says. “We also use suppliers in close proximity to our plant to avoid excessive transportation costs.
“It’s too early yet to calculate the savings we will make directly with the new Monforts dual heating unit and the boiler, because this depends very much on the price fluctuations between biomass and gas, but we are now in a position to choose the most beneficial option on a day-to-day basis. We will continue to invest in energy saving options and I would like to thank Monforts and its local representative Maquicontrolo for their invaluable assistance with this project.”