ITMA 2023
From Jacquard’s lightbulb moment to TMAS at ITMA 2023
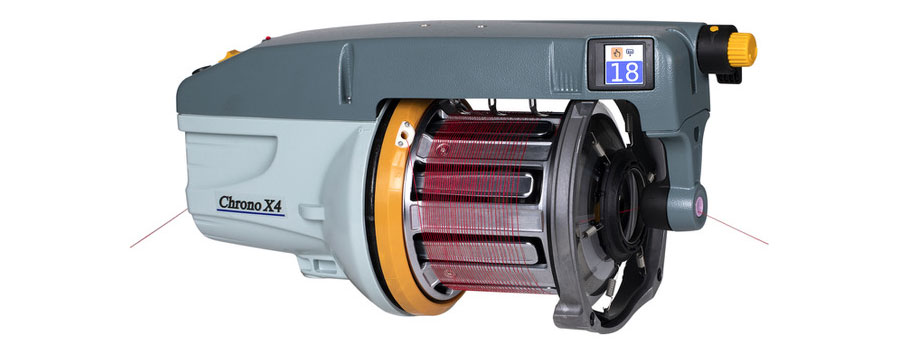
“Today, everyone is talking about digitalisation, but there is a strong case for considering the weaving process as the digital forerunner over 200 years ago,” says TMAS secretary general Therese Premler-Andersson. “When Joseph-Marie Jacquard invented his loom controlled by perforated cards and the first automated machine for which elaborate patterns were stored on them in ones and zeros, he arguably set the ball rolling for binary computer programming and all that has followed. There is certainly a direct line from Jacquard’s lightbulb moment to the latest innovations that will be displayed by our weaving technology members at ITMA 2023.”
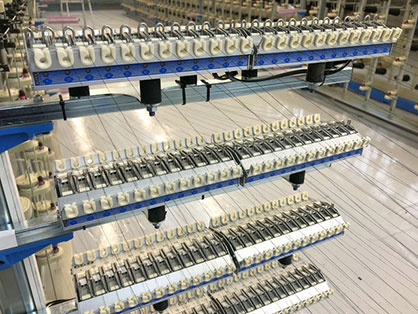
Know-how from Vandewiele Sweden
Vandewiele Sweden AB, for example, benefits from all of the synergies and accumulated know-how of the Belgium-headquartered Vandewiele Group – one of the market leaders in comprehensive weaving technologies (Hall 10, stand B201). This TMAS member has been the market leader in weft yarn feeding and tension control units for weaving looms for many years, supplying systems to the majority of the leading weaving machine manufacturers, as well for retrofitting in working mills around the world.
In Milan, Vandewiele Sweden will present its latest X4 yarn feeders with integrated accessory displays with which current settings and any alarms can be easily monitored and any required changes seamlessly carried out.
X4 feeders are available in three different versions – with an integrated
tension display (TED), with integrated active tension control (ATC), or with quick release, which enables weft tension settings to be transferred from one machine to
another, enabling a fast start-up the next time the same article is woven. The position of the S-Flex Tensioner is constantly monitored by an internal sensor – even if adjustment is made during power off.
With the ATC-W active tension control, the required tension is easily set and monitored on the integrated display. Once set, the system constantly regulates itself, ensuring consistent yarn tension during the weaving process which is constantly and accurately measured by the ATC sensor unit, sending a signal to the ATC operator unit resulting in consistently stable yarn tension at the required level. Quick release meanwhile provides a quick and easy way to change the brushring or tensioner.
Vandewiele Sweden is also launching its own e-commerce platform for ordering the market’s leading range of textile accessories at ITMA 2023
Wide width from Texo
TEXO AB (Hall 6, stand B301) has meanwhile seen a surge in the demand for its Compfelt weaving looms for press felt base fabrics.
“These are far from standard machines,” explains TEXO president Anders Svensson. “Off-the-shelf industrial weaving machines generally range in their working widths from 1.9 to 3.2 metres, with those purpose-built for technical applications such as geotextiles extending to wider widths of six metres and beyond. Meanwhile, one of the machines we have recently successfully delivered and commissioned has a working width of 23 metres.”
The demand for such machines comes from the suppliers of paper machine clothing (PMC) to paper mills, who in turn operate colossal machines for paper manufacturing.
All paper machines require a regular supply of PMC fabrics which are employed in three separate areas of the paper machine – the forming section, the press section and the drying section.
“Although the PMC business represents a small proportion of the total cost of manufacturing paper, it can have a significant impact on the quality of the paper, the efficiency of a machine and machine production rates,” Svensson explains.
TEXO Compfelt weaving machines are specifically employed for the production of endless (tubular) woven base fabrics for the press section of paper machines, where water is mechanically removed from the newly formed sheet of fibres.
Eltex EyETM
Eltex of Sweden AB will be running live demonstrations of the latest version of EyETM – a versatile multi yarn tension monitoring system – at ITMA 2023, in Hall 6 at stand A210.
The Eltex EyETM system is being widely adopted by weavers but unlike weft break sensors that are fitted solely on the weft insertion systems of weaving machines, it monitors the warping process prior to weaving. This means that instead of
monitoring only the six-to-eight weft yarns fed by the weft insertion system, the EyETM system is monitoring literally hundreds of yarns in real time on a warping creel.
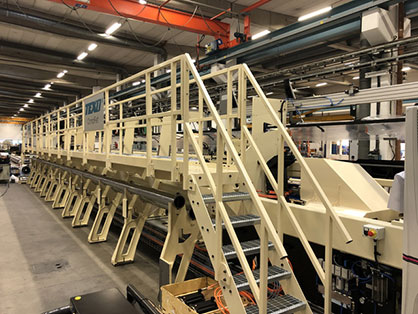
“Several hundred yarns can be fed from the creels during the warping process compared to only a few weft insertion yarns during weaving,” says Peter Wiberg, responsible for marketing at Eltex. “Our motto is ‘No Loose Ends’ and that’s exactly what we can guarantee with our system.”
With warping that can operate at speeds of 500 metres a minute, the yarn tension values from all yarns are continuously updated and displayed on a screen with pre-set warning levels indicated in red. When tension reaches outside the pre-set stop level, the machine is immediately halted, with indications both on the sensor’s LEDs as well as on the screen.
Bedrock
“Weaving remains the bedrock of the textile industry and the potential for continuously improving the process remains virtually limitless,” concludes Premler-Andersson. “This is a key area for specific TMAS members, as will be demonstrated in Milan. We look forward to meeting you there.”