ITM 2024
DiloGroup at ITM and DiloGroup’s In-house Exhibition
In addition to the five days in Istanbul, Dilo invites customers for a tour of DiloGroup’s headquarters in Eberbach to demonstrate relatively shortly after ITMA 23 its range of latest machine and line innovations which have been specifically prepared by the deputy CEOs Rebekka and Riccarda Dilo and their strong team from the sales, R&D and technology departments.
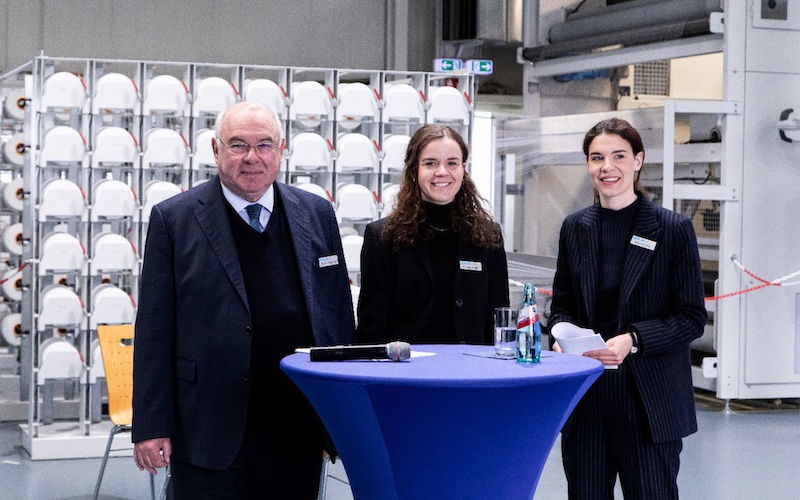
The complete lines and individual machinery are on display in a space of approximately 3.100 m2 to include the MicroPunch S research and demonstration line for needling lightweights in a range of 35 up to 160 g/m2including the MultiCard MCRR CC with FRS-P feeder which was returned from ITMA and reinstalled for the product development of hygiene, cosmetic, medical and technical lightweight nonwovens. This line is accompanied by a Hypertex line for the production of lightweight sandwiches of reinforced nonwoven layers to increase strength and stiffness in MD and CD directions for use as needled filtration and roofing material as well as shoe and garment applications. The layered mesh of filament or yarn is laid inline between a base and a cover of pre-needled material with speeds up to ca. 40 m/min.
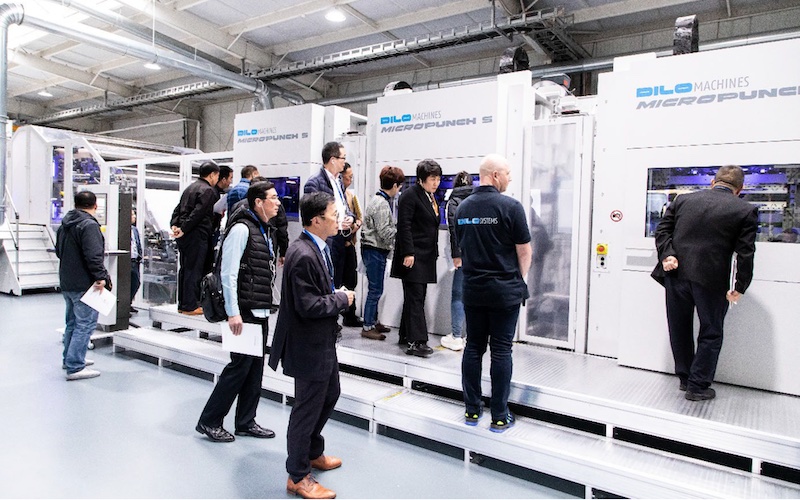
The MicroPunch S intensive needling line can thus be combined with the Hypertex process to include all areas of applications for lightweights needled from fine fibre.
In Technology Centres I and II three complete nonwovens lines are on demonstration including a 7 m wide needling line consisting of the VQC Card (Quadro), the high speed DLSC three apron layer capable of ca. 200 m/min infeed speed and the 7 m wide pre-needler.
Also, the HyperPunch machine in 3.5 m is included.
The aerodynamic web forming section “additive manufacturing” is on display through the 3D-Lofter which comprises a series of individual web formers programmable to lay down additional fibre material. This either in an
1. IsoFeed function to improve the regularity of a flock matt by up to ca. 4 - 5 % CV to feed cards more consistently.
2. Reinforcement function of needled substrate used as car interior linings of deep moulded pieces in order to strengthen locations in the felt plain where stress or strain concentrations take place. Using this method, fibre savings can be achieved of approx. 30 – 40 %.
3. An additional feature of the 3D-Lofter is the widely enlarged patterning capability of needled felts for automotive applications or wall and floor coverings. The 3D-Lofter offers sliding colours (“Colour Slide”), geometric patterns or inscriptions for achieving most modern design styles. The 3D-Lofter in combination with the DI-LOUR process, which was also demonstrated by the DI-LOUR IV double structuring system, is offering a joint technology which is particularly interesting for lightweight moulded car velours.
Textile products also on display can be given as samples along with technical literature.
At ITM the DiloGroup is looking forward to discussing together with its customers from Turkey and the region current needs and demands for preparing a more sustainable and successful future by innovations.
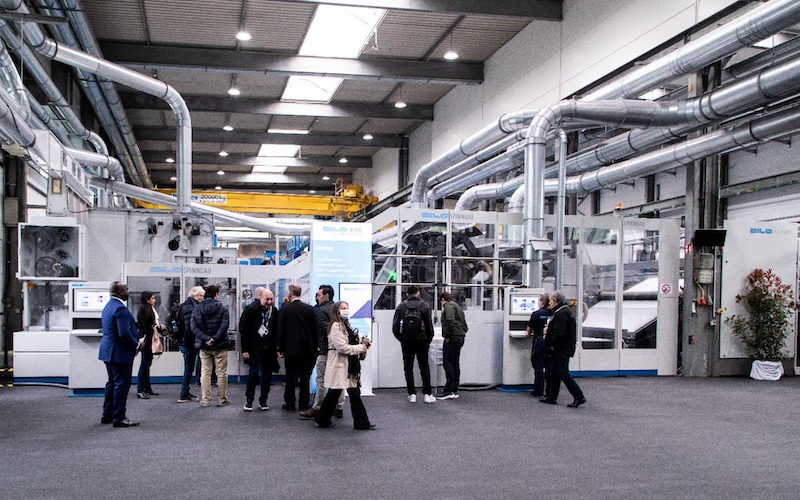