Dyeing, Drying, Finishing
New Montex leads the way for Brazilian home textiles specialist
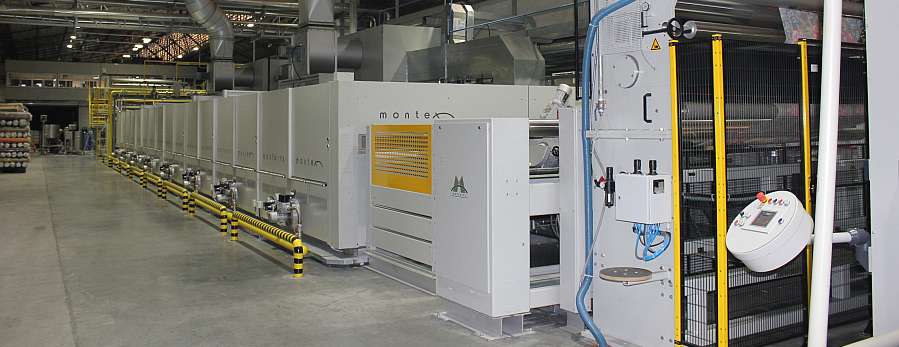
Currently producing 1500t/month – predominately home textiles for the domestic market – Döhler has, according to the Managing Director, Ingo Döhler, ambitious plans underway to double production within 5 years.
“We are constantly seeking new technology and solutions to further improve our production techniques,” he added. This includes the recent installation of the first Monforts stenter, a Montex 6500.
“With a finishing department comprising 10 older, locally produced stenters, we recognised the need to look at the latest technology in the marketplace,” he added. “We therefore placed the order for an 8-chamber Monte 6500 through local representative Euro-Texteis. Installed in a line incorporating a coating and flocking arrangement at the stenter infeed, the Montex has introduced wider fabric working at faster speeds."
“It has already provided energy saving of around 18% and increased production by as much as 30% with fabric widths of up to 3.20m.” he said.
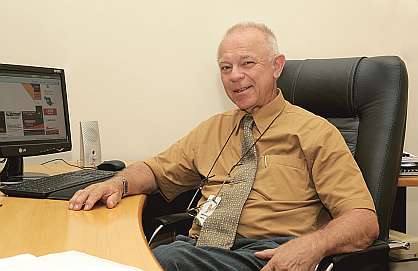
Pic: Ingo Döhler, Managing Director
Family-run
Döhler was founded in 1881 by Ingo’s great grandfather Carl Gottlieb Döhler, a German immigrant. Today, the company remains a family concern, with 10 family members – 6 as directors and 4 in production roles.
Led by President, Udo Döhler and Ingo Döhler as managing director, as the 4th generation, the newest 5th generation members are already working in the company.
Home textiles specialist
Some 60 years ago the company opted to specialise in home textiles, today producing a comprehensive range of curtains, upholstery, table cloths, bed linen, terry towels, kitchen towels, vertical blinds and mattress covers.
“This wide range allows us the flexibility to meet, for example, seasonal high demands for certain products.”
In the finishing department, the fully integrated vertical operation purchased its first stenter in 1958, a Brazilian Texima. Today with 10 units, the management recognised the need to modernise its facility and recently installed the first Montex 6500. With finishing on a wide range of fabrics including 100% cotton, cotton/polyester, cotton/viscose, viscose/polyester blends, linen, plus aramide and polyamide for military uniforms and raincoats.
The full coating and flocking configuration is able to undertake a variety of repellent coating and incorporates air knife techniques for table cloths and upholstery. Water proof production is also assured for a wide range of garden/poolside furniture fabrics.
The range of fabrics handled through the Montex varies with weights of 120g/m² for mattress covers up to 800g/m² for terry towelling.
Montex line
“By incorporating the coating and flocking units into the inlet feed of the Montex 6500 we are able to carry out virtually every application required,” explained Ingo. “The older stenters are virtually only able to finish one particular product.
“The Montex therefore makes us very flexible. For example, one of the older stenters also includes a coating and flocking unit, but it only accepts widths of up to 1.50m. The Montex with a working width of 3.20m opens new market opportunities for us. "
Another new product made possible for Döhler, thanks to the new Montex, is a 2.80m wide blackout curtain fabric, soon to be introduced into the market.
“Currently a blackout curtain this wide must be imported,” claimed Ingo, “We will be the first Brazilian company to offer this product.”
The Montex is also proving its versatility with curtain fabrics running at speeds of 40m/min compared with 27m/min on the older stenters.
Having started work in the company at 13 after school hours, today, more than 60 years later, Ingo has witnessed many changes to production.
“For a long time I thought that changes in the printing department were the most significant, but I can see that today the Monforts technology has to be the most dramatic change in our business,” he confirmed. “It is just impossible to overestimate the importance of this new machine and the benefits it has opened up for us.”
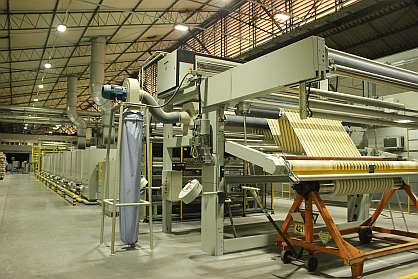
Pic: The new Montex 6500
Working 24/7 the finishing department operates a 3-shift system each day to meet the increased production.