Weaving
Personnel changes at Lindauer DORNIER
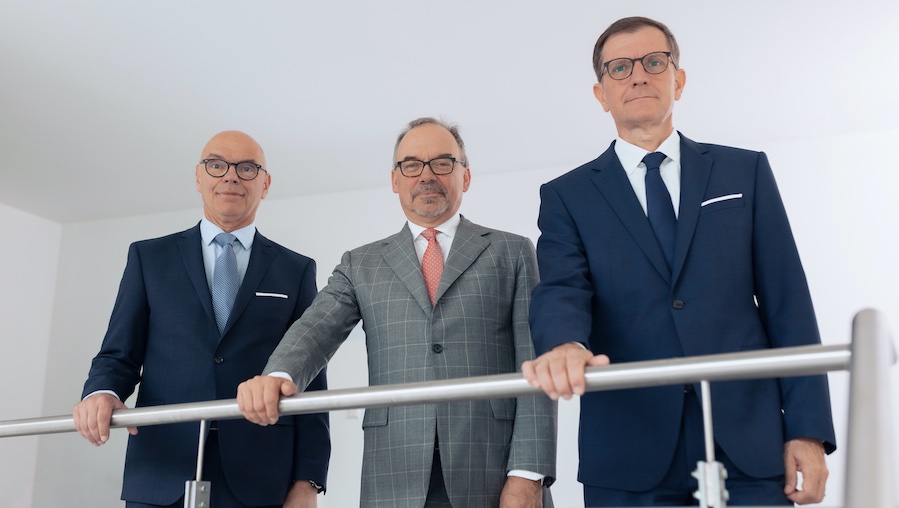
After 35 years in the company, including 25 years as Managing Director, Peter D. Dornier will hand over the operational management of Lindauer DORNIER GmbH on 1 July 2024 to join the Supervisory Board of the family-owned company. His successor as Chairman of the Board of Management will be Andreas Kueckelmann, previously Technical Managing Director at DORNIER. He will be supported by Commercial Managing Director Franz-Peter Matheis.
The planned change at the top is part of a rejuvenation of the operational level aiming to make the traditional family business fit for the future. "By handing over the operational management and making the planned move to the Supervisory Board, I am following DORNIER's tradition of interweaving the established with the new," says Peter D. Dornier." As a member of the Supervisory Board, I will do everything in my power to ensure that Lindauer DORNIER remains an independent, internationally active family business and continues to operate successfully."
Clear commitment to production in Germany
In 1989, after studying mechanical engineering in Esslingen and completing his diploma thesis in gas turbine design at mtu in Munich, Peter D. Dornier joined the family business, which his father Peter Dornier had founded in Lindau-Rickenbach in the summer of 1949 with engineers from Dornier's former aircraft building division. Taking over as speaker of the board of management in 1999 and later on promoted to CEO, he continues to drive forward the technological development of DORNIER, already an internationally renowned mechanical and plant engineering company at the time. He is supported in this endeavour by longstanding employees. "The fact that Lindauer DORNIER has grown from a small sapling to a stately tree in the 75 years of its existence is due above all to the commitment and good ideas of our workforce," says Peter D. Dornier. Today, around 1,000 "Dornianers" work at the company, 63 of whom are trainees. Peter D. Dornier also remains true to the company's clear commitment to producing all of its machines and systems exclusively in Germany. Basis for this are the "Seven Commandments", principles of Lindauer DORNIER GmbH, which he developed with a group of leading employees after joining the company in the early 1990s and which still guide the company today.
DORNIER is currently realising the largest investments in its recent company history in order to make the Lindau and Esseratsweiler sites fit for the future. In addition to modernising the machinery, this also includes new photovoltaic systems on the roofs of the production halls. In the long term, DORNIER aims to cover most of its electricity requirements from renewable sources. The investments in the new training centre at the headquarters in Lindau also show that the family business is serious about rejuvenation. From 2024, up to 75 young people will be trained here on 1,000 square metres as mechatronics engineers, industrial mechanics, machine and plant operators as well as commercial employees and dual university students.
Strategic focus on flexibility and quality
During Peter D. Dornier's tenure as CEO, the weaving machine division has been characterised by the increasing demand for technical textiles. While the manufacture of clothing and home textiles, which are also produced on DORNIER weaving machines, is mainly about mass, the focus for technical textiles for the chemical, automotive and aerospace industries is on precision, quality and maximum production reliability. Under his leadership, the engineering-driven company therefore consistently follows the new credo "Quality creates value" and positions itself as a reliable partner working closely together with manufacturers of high-quality, technically sophisticated fabrics. These manufacturers also appreciate the durability and flexibility of DORNIER weaving machines, which achieve running times of over 40 years. To enable fabric manufacturers to convert DORNIER air-jet and rapier weaving machines more quickly, Peter D. Dornier is driving forward the platform concept. A milestone in this strategy was the market launch of the P2 rapier weaving machine in 2019. Thanks to its modular design, fabric manufacturers can easily adapt it and thus react quickly and flexibly to market fluctuations. "Anything that can be wound onto a yarn spool can be processed on a weaving machine from DORNIER," says Peter D. Dornier, "whether for airbags, protective clothing, vehicle tyres or high-quality textiles made from silk, wool and linen – all these convenient and necessary companions of our modern life are produced worldwide every day using technology from Lindau on Lake Constance."
Part of fast-growing future fields
When Peter D. Dornier took over the business of Lindauer DORNIER in 1999, smartphones, photovoltaic systems and electric cars in large quantities were still visions of the future. Today, DORNIER's Special Machines division designs, develops and builds plants on which the company's customers produce e.g. special films for smartphones, PV systems and lithium-ion batteries for electric vehicles. Peter D. Dornier has thus "interwoven" the traditional family business from Lake Constance with three important and fast-growing future fields. Films for packaging food and medicines are also produced on these plants. Lindauer DORNIER GmbH is the market and technology leader in the field of machines for the production of biaxially oriented polyester film (BOPET). As the company is heavily dependent on the global economy, with an export ratio of over 90 per cent, the special machines division has proven its worth, especially in difficult times. For example, while fewer textiles were woven during the COVID-19 pandemic, the demand for packaging rose sharply due to the higher hygiene requirements worldwide.
Fibre composite components in series production
Peter D. Dornier demonstrated his pioneering spirit by founding the Composite Systems (CS) division in 2014, in which DORNIER bundles its decades of experience in the construction of weaving machines and film stretching systems. Here, the company develops state-of-the-art systems for the scalable series production of high-quality yet cost-effective composite semi-finished products made of carbon, glass and aramid for the growing fibre composite industry – an industry that is also on the rise due to increasing sustainability requirements and the associated demand for weight and CO2 savings. Highly specialised suppliers use CS systems to produce lightweight components for sports equipment, high-performance vehicles and aircraft. In a way, Claude Dornier's grandson is taking the company back to its roots: while the knowledge of the former aircraft engineers around founder Peter Dornier was used in the construction of weaving machines when Lindauer DORNIER was founded, the expertise of DORNIER engineers now flows into the production of components for the latest aircraft.