Spinning
Asteks prepares its customers for the industry of tomorrow with the spirit of innovation
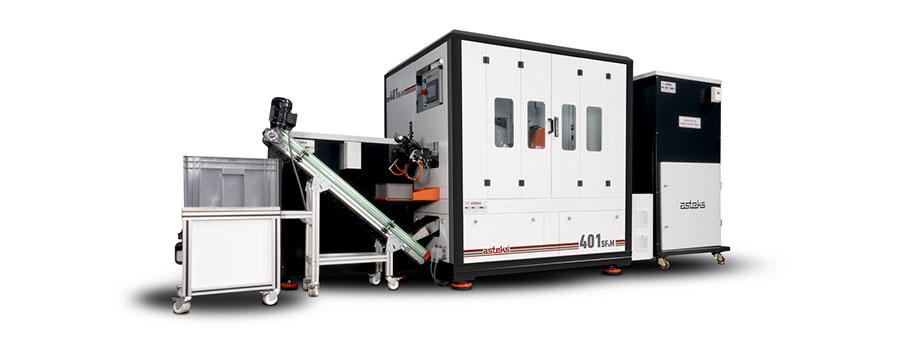
Aprons, cots and grinding technologies specialist Asteks has succeeded in becoming one of the leading partners of the textile industry with its innovative vision in its sectoral journey that started in 1970. Today, the company continues its production in its modern facility with an area of 11 thousand square metres in Istanbul and exports to the leading markets of the global textile industry. After the restructuring in 1997, Asteks accelerated its R&D activities and thus went beyond being a mere supplier of intermediate goods and became a technology manufacturer.
Asteks R&D and Technical Support Engineer Mesut Yüksel said that innovation has always been one of the fundamental building blocks of the company and pointed out that the investments made in this field will shape the future of the company. Yüksel disclosed; “We do not view innovation only to increase market share in competition and to improve product and service quality. Innovation for Asteks also has a special importance for increasing efficiency in production processes and reducing costs. Transformation and change in the textile industry is faster than ever and continuous innovation is inevitable to keep up. We continue our efforts to keep pace with change for a sustainable life and to be a part of this transformation with our products that have gained value through innovation.”
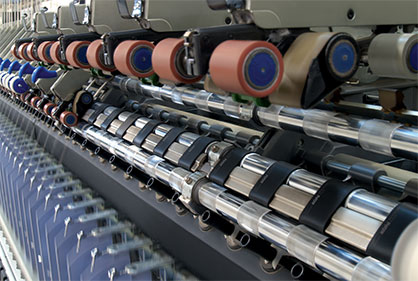
R&D department, established 15 years ago, turned into a centre for new solutions
Mesut Yüksel, recalling the restructuring in 1997, said that aprons and cots production technologies were purchased from Switzerland, which is famous for its engineering, and ISO studies were carried out during this period. Yüksel stated that R&D studies started about 15 years ago in order to meet demands increasing and diversifying continuously, to be competitive in the market and to offer new products, saying; “Asteks recognised the need for an interdisciplinary structure while establishing its R&D department for innovation activities. For this reason, industrial, chemical and mechanical engineers as well as spinning technologists began to work in a coordinated manner here. As a textile engineer, I have been involved in this team since 2019 in order to develop the technical aspect as well as the practical potential of the researches.”
Explaining that R&D activities focus on both the development of products in the existing field and pioneering new solutions for new application areas, Yüksel stated that Asteks continues these activities uninterruptedly with a significant R&D budget. He noted that Asteks has now turned into a technology developing company thanks to these activities carried out 100% in-house, and added that the new generation aprons and cots attract attention in the market with their increased performance and durability, and the grinding machines with their high automation features.
Yüksel shared the following details about the product development process; “Firstly, there is the Needs Analysis phase. Here, evaluations are made within the framework of feedback and demands from the customers. The second stage, design, is concerned with product design and prototypes are produced. In the development phase, the product is manufactured and tested. Products that successfully pass these processes reach the Marketing stage. Here, marketing strategies of the product are created and introduced to prospective customers. In the fifth and final stage, Distribution, the product now meets the market commercially and after-sales services begin.”
The grinding department is digitalised with Asteks solutions
Mesut Yüksel stated that in addition to the aprons and cots that enabled them to become the leader in the Turkish market, their recent developments in cots grinding processes have also received great acclaim and recognition from textile manufacturers, and emphasised that their work in this field has not lost momentum. Drawing attention to the increase in automation in cots grinding machines, Yüksel said that the grinding process has become faster and easier, while the grinding quality has reached a certain standard. He disclosed; “As of today, our new generation of cots grinding machines are highly automated and digitalised. With each new model, we increase productivity and quality while strengthening automation to avoid manual problems in the grinding process. The software in our machines is completely developed by engineers within Asteks. As a result, we have developed more compact models with each new solution and have become an indispensable partner for the cots grinding departments of spinning mills. This is basically the result of our R&D and marketing success.”
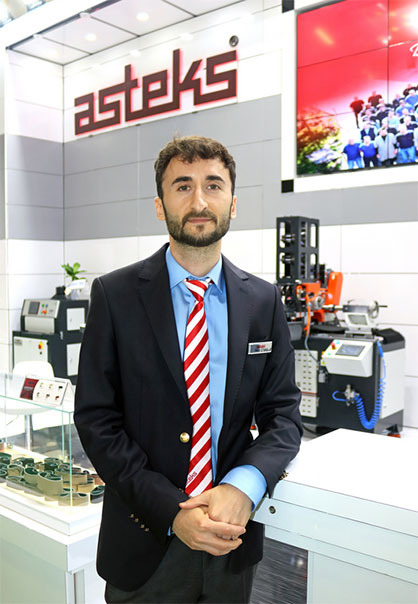
Yüksel, explaining that their R&D activities are not limited to grinding, stated that they have also implemented an important innovation for all industrial enterprises with the Industry 4.0 concept. He noted that the 101-AGV Automatic Guided Load Transport Vehicle, developed by Asteks with the participation of engineers from different disciplines, is an ideal logistics solution for facilities working in large areas, saying that they offer savings and cost advantages to businesses. Yüksel expressed that textile manufacturers also demand innovations in shorter periods of time due to the acceleration in the final consumer and retail segment, and that Asteks meets these demands with its own know-how and production capability.
“Our customers are also our R&D partners”
Mesut Yüksel disclosed that the majority of Asteks's current customers are yarn manufacturers and added that due to the wide variety of fibres processed in spinning, there is a need for different types of aprons and cots and this demand continues to increase. Yüksel stated that it is important for these products to be able to work in accordance with variable parameters, and explained that the characteristic properties of the fibres that aprons and cots can work with are determined and the first tests are carried out in Asteks’ own quality control department. He shared the following details:
“After the tests such as strength, tensile strength, friction coefficient and surface smoothness, trials are carried out in the field and we continue to improve our products with the feedback we receive from our customers. For example, customer demand played a major role in the creation of the S/CTA type apron. The climatic conditions of the mills, the machines on those aprons and cots to be used and the properties of the fibres to be processed were tested in real values in the field. We found that strengthening the rubber structure of the product with carbon reinforcement prevented wear problems and we immediately started to implement it. The Uster test results showed that we were successful in this regard and we achieved customer satisfaction. The development story of our E-750 drafting cots with late contamination feature was similarly developed in the field. Our customers, whom we see as a partner in the product development process, enable us to do better, even to see the new demands that will emerge in the market early and to move forward. Therefore, I would like to thank all our partners and customers for their trust in us.”
Yüksel relayed that there have been demands for sustainability and greener textile production methods in recent years and that technological researches have started in this direction, and said that Asteks has carried out significant researches on these issues and started to offer solutions that create extra value added to the market. He stated that they bring together the latest and competitive Asteks solutions with the industry at the exhibitions they attend, adding that they will show their innovation power to the global market by participating in the ITMA 2023 exhibition to be held in Milan between June 8-14.