Other suppliers
Seeing beyond the patterns with Shelton Vision

The patent-pending system has been integrated into the company’s WebSpector platform – one of the most powerful plain fabric inspection systems on the market – and validated through factory trials on a purpose-built full scale in-house demonstration system with sophisticated fabric transport capabilities.
As a result, a first system has already been ordered by a manufacturer of both plain and patterned fabrics, including camouflage, in Colombia.
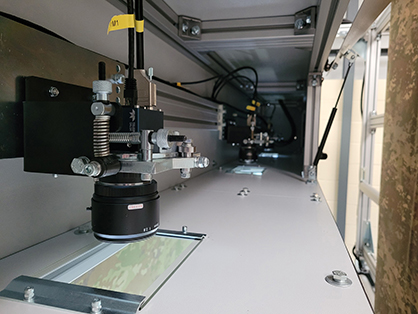
This follows the successful conclusion of a 21-month Innovate UK project in which techniques for the resolution of complex pattern deformations were developed by machine vision and computer scientists in the company, backed up by the machine vision and robotics department at Loughborough University.
Restrictions
Traditional methods for defect detection rely on human inspection which is ineffective, with detection rates under 65%, while the Shelton WebSpector machine vision system offers a sophisticated platform for automated defect detection of over 97%, but until now has been restricted to plain textiles.
“What our new system basically does is essentially make the ‘good’ pattern invisible to the detection software,” explains Shelton Vision Managing Director and CEO Mark Shelton. “Building on our market leading vision system for plain textiles, we have developed template matching techniques for the resolution of complex pattern deformations in order for the system to pick up defects in the pattern as well as underlying defects.”
While pattern matching and neural network approaches have previously been tried for patterned textiles they have failed to provide a practical solution due to the extreme complexity associated with pattern matching on deformable substrates like textiles, as well as the time required to train a neural network for each pattern type.
Challenges
“The challenge is that fabrics are not rigid and can be creased or stretched and are also subject to local distortion,” says Mark. “As a result, inspection without the technique we have developed, would lead to thousands of false positives. Our sophisticated pattern inspection software techniques ensure a clean image, allowing the detection of faults on fabrics running at speeds of up to a hundred metres a minute.”
The full system consists of:
A camera and lighting system for optimum image capture at high speed and associated image processing hardware.
Self-training software utilising statistical analysis to automate the system configuration for new textile products.
An advanced suite of defect detection algorithms for the detection of all textile defect types.
An AI-driven defect classification system which learns and automates defect naming in real time, as well as a real time defect grading capability based on client decision rules.
A system for recording and retrieving complete roll map images for subsequent review and quality control.
The generation of textile roll maps with complete defect data allows for an optimised textile cut plan, improved downstream processing and quality assurance.
“Defect detection represents a major industry challenge,” says Jason Kent, CEO of the British Textile Machinery Association. “The failure to provide textiles within defect tolerance limits can lead to whole batch recalls, resulting in costly customer claims and downstream production delays. Poor defect management is also a major source of industrial waste. The potential addressable market for patterned textile vision systems is estimated to be well in excess of £5 billion when considering on loom, on knitting machine, in process and final finished fabric inspection. No other vision system on the market offers these features for patterned textiles, so it’s a great example of UK innovation at its best.”
Founded in 1940, the British Textile Machinery Association actively promotes British textile machinery manufacturers and their products to the world. The non-profit organisation acts as a bridge between its members and the increasingly diverse industries within the textile manufacturing sector.