Knitting & Hosiery
Managing energy instead of wasting it
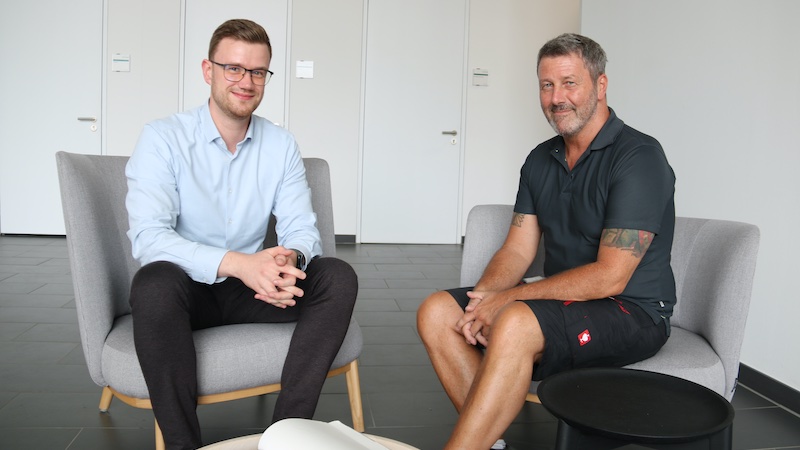
Energy Efficiency Solution from KARL MAYER helps save energy - initial practical experience
To ensure that they can use the EES easily, KARL MAYER has translated the operating manual into six languages and developed a tutorial which can be found on the KARL MAYER Academy online platform. The explanations start with information on opening and configuring with customer-specific data. All display options and search functions are then presented. The final chapter focuses on analyzing energy consumption, costs and CO2 emissions.
In addition, further optimizations for the EES are on the way or have just been completed. “We are currently introducing a timer function feature. The complete integration of EES as a further solution in our Customer Portal has already been finalised. Just like the Dashboard and CORE LITE, the EES can now also be accessed in this way. This makes it even clearer and easier to use,” says Markus Bahde, Product Owner Digital at the KARL MAYER GROUP.
The innovative mechanical engineering company is working with its customer RÖKONA on the new energy management solution. The warp knitting specialist develops and manufactures technologically sophisticated textiles for new products and applications in Germany, focusing consistently on customer requirements and relying in particular on technical innovations. In July, KARL MAYER Sales Manager Julian Schubert spoke to Stefan Passauer, Production Manager Warp Knitting at RÖKONA, about his involvement in the development and optimization of the EES.
JS: Why did you decide to work with KARL MAYER as a pilot customer in the development of the EES?
SP: We are primarily concerned with the issue of sustainability. Protecting the environment and natural resources plays a central role in our corporate policy. We have had an integrated environmental management system certified to ISO 14001 since mid-2023 and take a precautionary and planned approach to environmental issues. Every contribution counts, especially when it comes to energy. A special team at our company monitors energy consumption in all process steps of our fully integrated production.
In addition, our customers are increasingly demanding verifiable contributions to climate-friendly production. Brands in the automotive sector in particular are demanding documented data, for example on the reduction of CO2 emissions per m² of fabric. With the EES, we can determine the required values, store them in a master database and compare them as proof of improvements. This also helps us with environmental audits.
JS: What exactly does the collaboration in the EES project look like?
SP: We were involved in the development right from the start, contributing our wishes and participating in the ideas generation process. Brainstorming started at the beginning of 2023. The following March, we installed a current measurement device on the first machine, an HKS 3-M ON, and began monitoring the data via the web browser. At the same time, we discussed potential improvements with the experts from KARL MAYER on an almost weekly basis. In August 2023, we connected the new HKS 4-M ON field test machine, which is already equipped with the EES, to the KM.ON cloud via the k.ey device and included it in the pilot project. Three more machines followed later, including a double raschel machine. In April of this year, we moved the system from a development server to the KM.ON infrastructure. The machines are now integrated into normal production operations with the EES.
JS: With four machines in the test, you can certainly already get a good idea of how the EES works. What experiences have you had?
SP: The solution works for us! It operates very reliably and delivers data that is easy to understand and provides valuable information. The various analyses are particularly important to us, for example comparing the costs and consumption of a machine over a certain period of time or when working with different items. It is also possible and useful to compare several machines with each other. We have found that the HKS 4-M ON produces with the highest energy efficiency. The HKS 3-M ON is the fastest machine that we have integrated and monitor in the EES.
JS: What further developments would you like to see? What else should the EES be able to do?
SP: We still have ideas for further optimization of the display. We would also like to be able to enter specific input via the web browser in order to link and save article data with the corresponding operating data. Most recently, we have co-developed a function for automatically switching the machine to standby mode. This is already working very well and is a huge relief for us. Previously, we only switched the machines to standby mode at the weekend using a timer, manually for each individual machine. The EES now enables automatic shutdown according to a schedule of production and heat-up times, which can be entered on the display of any mobile device or computer. This means that we can also use shorter interruptions in operation, for example when changing articles, to save energy.
JS: This means that you are already well on the way to saving energy. I wish you continued success and thank you for the interview.