Dyeing, Drying, Finishing
Tintoria Finissaggio 2000: Innovative textile company invests in the latest Mahlo development
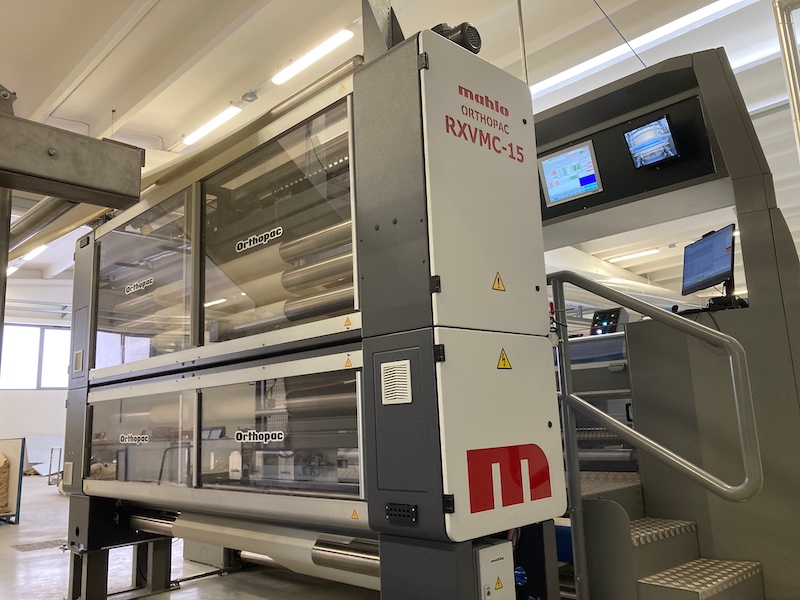
Today it offers the complete range of dyeing of all types of fibres, finishing, digital printing, lamination and membrane lining. These processes are used to give fabrics certain properties, such as colour, pattern, softness, shine or waterproofness.
With over 100 employees, Tintoria Finissaggio's company philosophy is based on three cornerstones: sustainable innovation, high human capital and first-class customer service. The latter is guaranteed above all by customised production and rapid response to new requirements. The company serves a wide range of customers in various industries, including fashion, home textiles, automotive and technical textiles.
At Tintoria Finissaggio 2000, customers benefit from the fact that all processes are handled under one roof, from design support to the finishing of fabrics, combining decades of experience with the new possibilities of lamination and digital printing. The dyeing plant in Masserano is a state-of-the-art facility that fulfils the strictest environmental standards - to name just one example. In general, Tintoria Finissaggio 2000 continuously invests in state-of-the-art technologies and production facilities in order to achieve high-quality results while ensuring sustainable production processes.
The upgrading of new equipment is therefore another part of the company strategy. Tintoria Finissagio 2000 also focused on innovation when equipping a new stenter frame. The company opted for the latest development from German machine manufacturer Mahlo GmbH + Co. KG: the Orthopac RXVMC-20 automatic straightening system. The new straightening concept is specially designed for processing textiles with high distortion dynamics, i.e. textiles with highly variable distortion. The automatic straightening system can eliminate these distortions in textile webs even faster and more precisely than any other system on the market. "We have paid particular attention to the straightening mechanism and its interaction with the probe system's analysis electronics," explains Mahlo Sales Manager Thomas Höpfl. Two individually controlled and driven straightening modules with a total of three bow and four skew rollers ensure that bow and skew distortions are corrected in small steps. The control concept is also new. A scanner group at the infeed of the straightener detects distortions even before they reach the correction rollers. This means that the rollers are brought directly into position and the fabric is corrected from the very first centimetre. A scanner group at the outfeed also recognises any residual distortion, which is then corrected on the second straightening module.
Just a few months after commissioning, it is clear that the decision in favour of the new Mahlo concept was the right one. The owners Dino Masso and Marco Bardelle emphasise: "We had high hopes for the new Orthopac RXVMC-20 straightening system from Mahlo and our expectations have been exceeded by far. The results have fully convinced us. Mahlo also offers outstanding customer service and provided us with excellent support and training during the first few weeks of using the new technology."