Weaving
Clever energy-saving solution at no extra cost
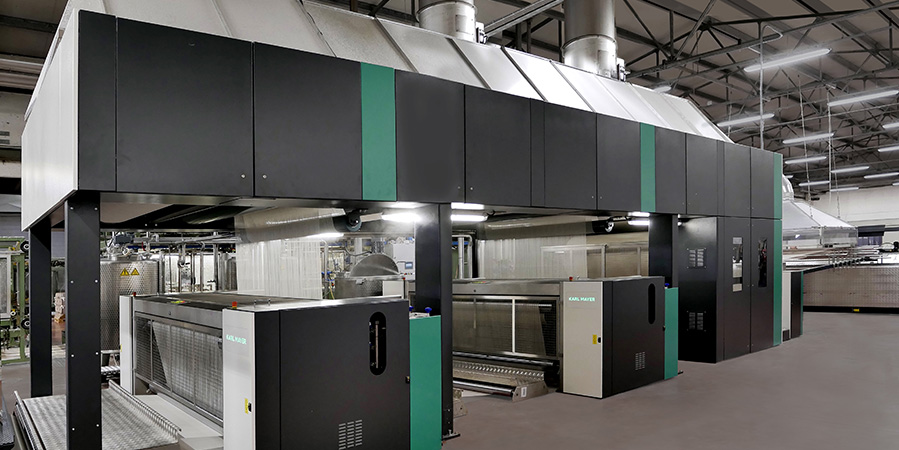
Ulrike Schlenker from KARL MAYER GROUP spoke to Karl-Heinz Vaassen, Head of Textile Drying at KARL MAYER, about the background, benefits and technical details of the innovative solution.
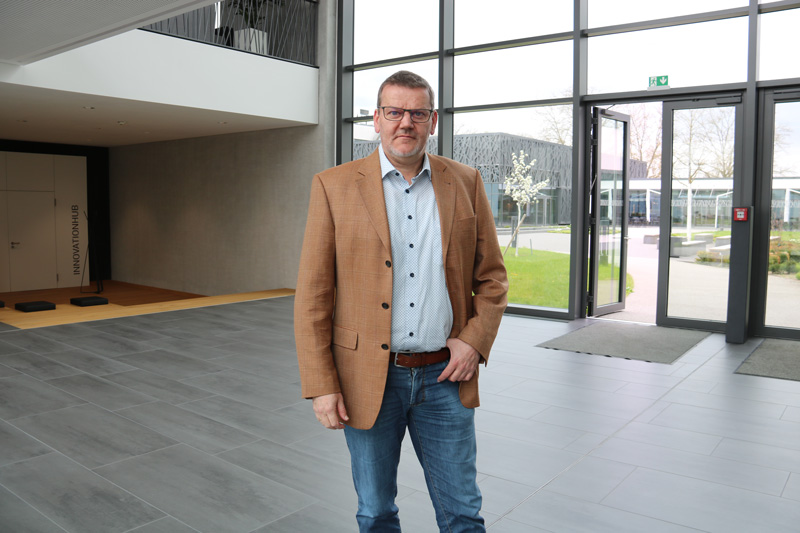
US: Can you briefly describe the principle behind CASCADE?
KHV: At its core, CASCADE is about making optimum energy use of the steam that is made available to our cylinder dryers as a heat source - which is achieved through multi-stage (cascading). In conventional systems, utilization only takes place in a single stage: the steam conveyed into the drying cylinders changes phase, but the medium maintains its temperature - the outgoing media flow is now liquid (condensate) and therefore "used up" for further utilization with the required high temperature uniformity. Nevertheless, the remaining heat content is too valuable not to be reused within the machine. This is precisely where CASCADE comes in with genuine in-machine energy recycling: From the condensate that cannot be used for heat transfer, we generate steam again in stage 2, which we then process in the direct subsequent stage 3 to make it "suitable for dry cylinders" and feed it for direct inline use.
US: How does the customer benefit from this inline energy recycling?
KHV: This enables our customers to save considerable costs. We have calculated various practical scenarios and identified annual savings potential of up to USD 16,800. Of course, the actual cost reduction depends on many technical parameters, especially the number of cylinders and the process pressure used.
When developing CASCADE, it was therefore important to us that the customer can precisely monitor the benefits of the solution. That's why we integrated a measuring cell into the system. The sensor provides the customers with real-time data on the amount of steam recycled, which they can view on a dashboard at any time and convert into CO2 equivalents saved. This transparency about the real reduction in consumption is a real advantage!
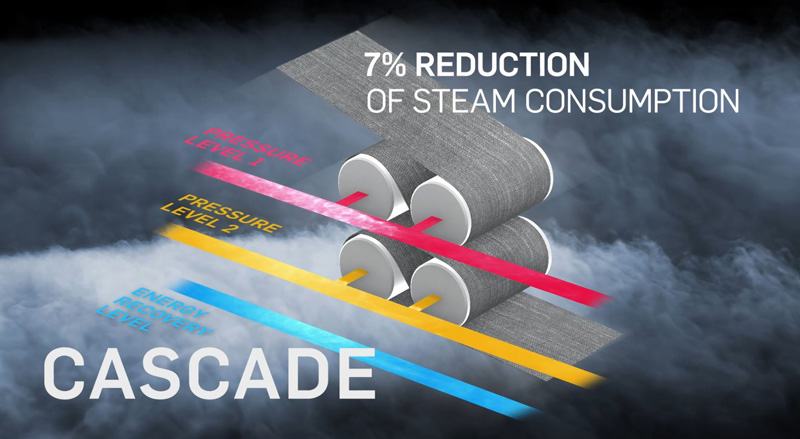
US: Reusing the steam used in drying processes is an obvious idea. Was it as easy to implement as it sounds?
KHV: We didn't reinvent the wheel, but we did redesign it for our purposes. After extensive research, I was inspired by solutions from the paper industry. Paper manufacturers have to work with an oversupply of steam due to the process and recycle energy as standard to avoid otherwise unacceptably high losses. Our cylinder dryers have massively lower steam flows, work classically without these excess steam quantities and therefore require a specific recycling concept optimized for textile technology. The idea for this had been on my mind for some time.
As a textile mechanical engineer with a long-standing passion for thermodynamics, I have already developed numerous thermal systems for the textile industry. However, the task of developing a system for the circulation of steam flows in cylinder dryers was new and challenging for me. CASCADE is a unique solution for which we have applied for patent protection.
US: What does the launch of CASCADE look like? What strategy are you using to launch the solution on the market?
KHV: As a family-owned company, we assume social and ecological responsibility. For us, sustainability is not just lip service, but a focus of our innovations. That is why we have integrated CASCADE into the standard equipment package of our PROSIZE® and BLUEDYE. The customer receives the additional benefit in terms of costs and CO2 footprint reduction at no extra charge.
In order to make CASCADE known in the market, we had the solution in our trade fair luggage for ITM from 4 to 8 June 2024 in Istanbul and will show it at ITMA ASIA + CITME from 14 to 18 October in Shanghai. We look forward to many interesting discussions about it. If you have any questions or would like to know more, please feel free to contact me directly. I can be reached at karl-heinz.vaassen@karlmayer.com
US: That is a valuable offer. Thank you very much for the interesting conversation!