Textile chemistry
EMPA introduces friendly fibers for textiles without PFAS
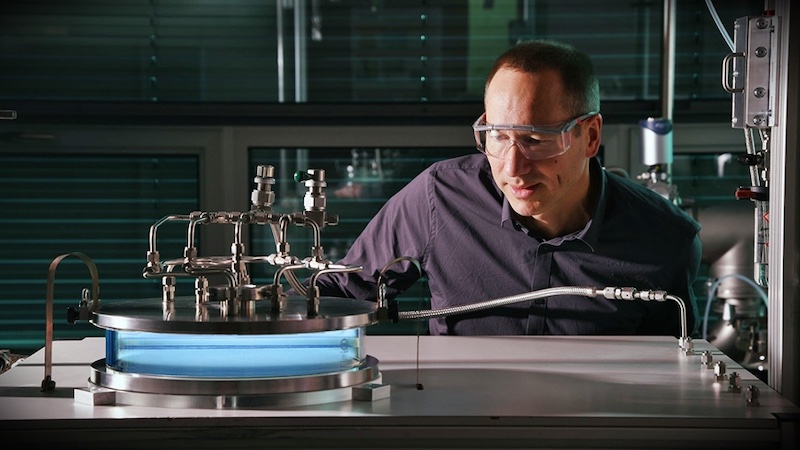
If swimming trunks are to retain their shape after swimming and to dry quickly, they must combine two properties: They must be elastic and must not soak up water. Such a water-repellent effect can be achieved by treating the textiles with chemicals that give the elastic garment so-called hydrophobic properties. In the 1970s, new synthetic fluorine compounds began to be used for this purpose – compounds that seemed to offer countless application possibilities, but later turned out to be highly problematic. This is because these fluorocarbon compounds, PFAS for short, accumulate in the environment and are harmful to our health (see box). Empa researchers are therefore working with Swiss textile companies to develop alternative environmentally friendly processes that can be used to give fibers a water-repellent finish. Dirk Hegemann from Empa's Advanced Fibers laboratory in St. Gallen explains the Innosuisse-funded project: "We use so-called highly cross-linked siloxanes, which create silicone-like layers and – unlike fluorine-containing PFAS – are harmless."
Shrouded in plasma clouds
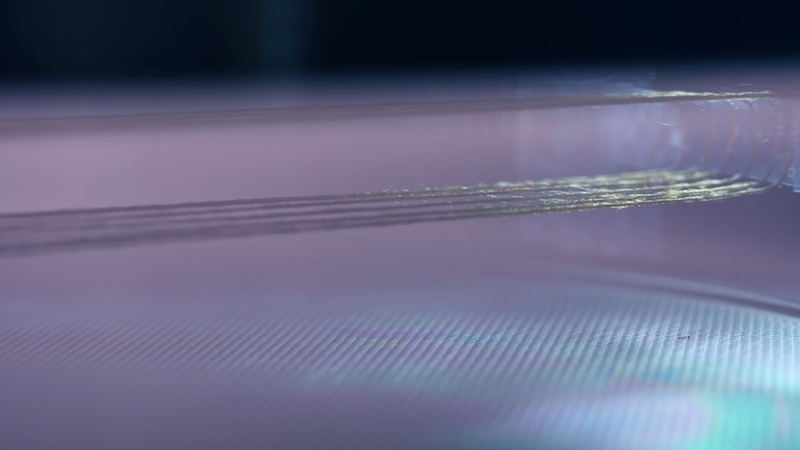
Empa's plasma coating facilities range from handy table-top models to room-filling devices. For the coating of textile fibers, the siloxanes are atomized and activated in a reactive gas. They thereby retain their functional properties and enclose the textile fibers in a water-repellent coating that is only 30 nanometers thin. Fibers coated this way can then be processed into water-repellent textiles of all kinds, for example garments or technical textiles such as upholstery fabrics.
The advantage over conventional wet-chemical processes: Even with complex structured textiles, the seamless distribution of the hydrophobic substances is guaranteed right into all turns of the intertwined fibers. This is crucial, because even a tiny wettable spot would be enough for water to penetrate into the depths of a pair of swimming trunks, preventing the garment from drying quickly. "We have even succeeded in permanently impregnating more demanding, elastic fibers with the new process, which was previously not possible," says Hegemann.
Great interest from industry
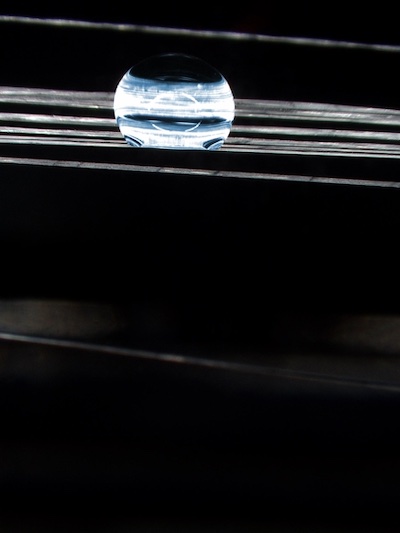
In initial laboratory analyses, textiles made from the new fibers with an environmentally friendly coating are already performing slightly better than conventional PFAS-coated fabrics. They absorb less water and dry faster. However, the miraculous properties of the fluorine-free coating only really come into their own after the textiles have been washed several times: While the performance of conventional PFAS coatings in stretchy textiles declines considerably after repeated wash cycles, the fluorine-free fibers retain their water-repellent properties.
Hegemann and his team are now working on scaling up the fluorine-free laboratory process into efficient and economically viable industrial processes. "The industry is very interested in finding sustainable alternatives to PFAS," says Hegemann. The Swiss textile companies Lothos KLG, beag Bäumlin & Ernst AG and AG Cilander are already on board when it comes to developing environmentally friendly fluorine-free textiles. "This is a successful collaboration that combines materials, fiber technology and plasma coating and leads to an innovative, sustainable and effective solution," says Dominik Pregger from Lothos. And Bernd Schäfer, CEO of beag, adds: "The technology is environmentally friendly and also has interesting economic potential."
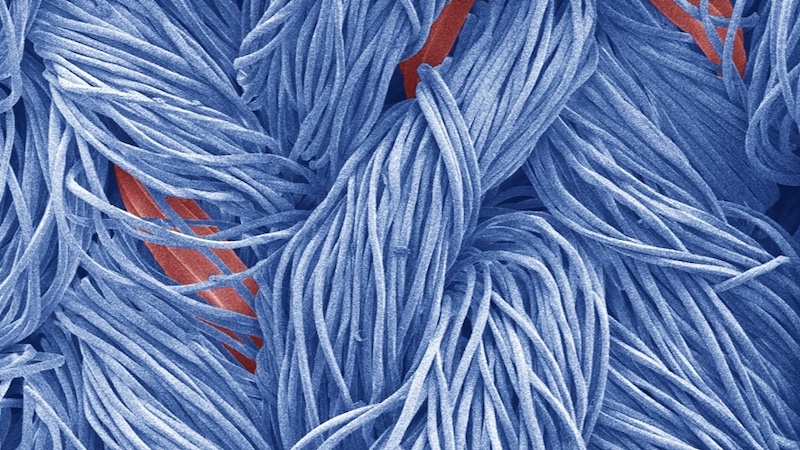