Spinning
Tatham save big money on yarn spinning costs
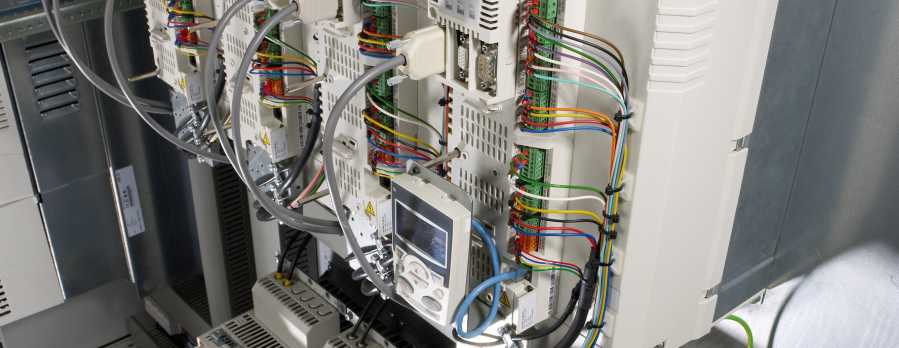
ABB low voltage AC drives were used by Tatham Ltd to achieve the huge savings for their customer who produces cloth used in tennis balls and billiard tables. The woollen spinners were using eddy current drives to power and control its four carding engines. These operate on the principle of a slipping clutch for speed variation. This has the disadvantage that the motors are turning continuously, even when the machine is not in production, making them extremely inefficient - although the motors were turning for over 7,000 hours, only around 1,620 hours of this time were spent in actual production.
The original set up used a 15 kW motor, a 25 kW motor and two 7.5 kW “Tandem Motors” to drive various sections of the machine. These motors where also driving the machine sections directly, shaft to shaft, meaning that the motors where continually running at full load current and sometimes overheating.
The new system uses 11 kW AC drives and motors, reducing the on time, when the motors are switched on, to just over 3,500 hours. Together with the reduced power usage, the solution achieved yearly energy savings of 540,000 kWh. This has reduced the energy bill for the machines by £27,000, while cutting CO2 emissions by 292,000 kg/year. Payback for the system was just over 10 months. Tatham’s engineers conducted an energy survey and designed a new drive system based on four ABB machinery drives using ABB Direct Torque Control (DTC). DTC allows complete synchronisation of the machine sections, giving highly accurate control and improved product quality.
In the new control arrangement, 11 kW geared motors and associated gearboxes were fitted on the scribbler, carder and eccentrics sections, along with an additional 4 kW motor and gearbox on the doffer. The gearboxes ensure that the correct power is delivered to the rollers while allowing the use of a smaller motor. The AC drives are also run at 40 Hz, allowing further energy savings.
The low voltage AC drives display data that inform users of the “On Time”, when the motors are switched on, “Run Time”, when the motors are driving the rollers, and “Kilowatt Hours Used”, making it easy to compare the operation with the previous situation.
The new motors also run cooler than the previous set-up, resulting in reduced maintenance and improved reliability.
ABB (www.abb.com) is a leader in power and automation technologies that enable utility and industry customers to improve their performance while lowering environmental impact. The ABB Group of companies operates in around 100 countries and employs about 130,000 people.