Spinning
Brandnew technologies at Igatex 2024 in Pakistan
Saurer’s textile experts will advise Pakistani customers on the best solutions to achieve their goals, whether they need commodity yarns at competitive costs, recycling yarns from OE machines or the finest ring yarns or the highest productivity in their spinning mill. Come to see booth A41-A64 in hall 3 to meet the Saurer team and booth B36 in hall 3 to see the Texparts team!
Fashion starts with Saurer yarns
The story of every garment or interiors basically begins with the yarn. Fancy yarns are innovations in predefined fabric patterns, while core yarns determine the final fit of the material. When developing new machine features, Saurer focuses not only on new technical features but also on developments in yarns and textile technology. Sauer wants to enable customers to create new yarn types, spin new fibre materials or improve the processing of extremely short mechanically recycled fibres.
Autoairo – revolutionising air-spinning
Air-spinning has the highest output of all applications. Towel yarns have with high demands for exceptional absorbency, ease of washing, and sustainability. With Belairo yarn, spun on the revolutionary Autoairo air spinning machine, Saurer is offering towel manufacturers exciting and new economic prospects. Towel, made from Belairo yarn last up to 10 times longer, maintain their superior absorbency and plush texture, and make a positive contribution to the environment. Belairo yarn is also the choice for producing classic polo shirts, offering an elegant look without pilling, even after 500 wash cycles, at a cost-effective price.
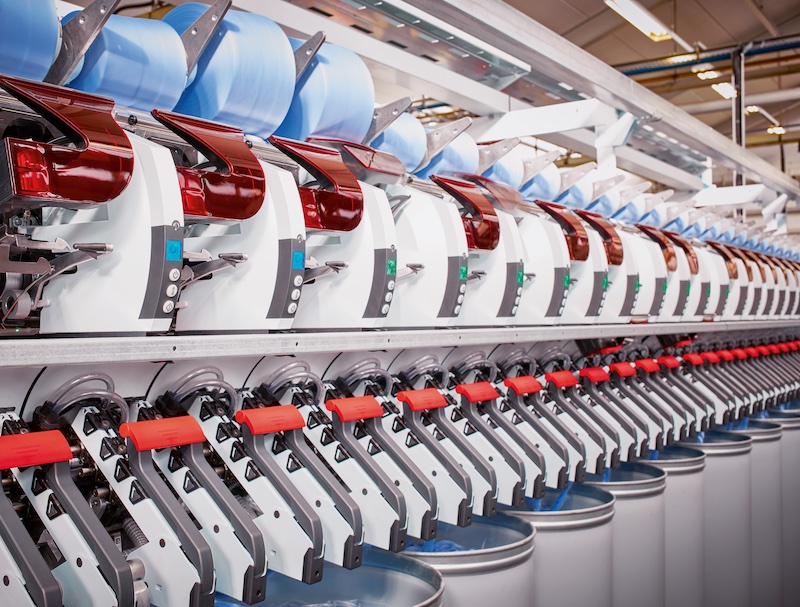
Leading the way for recycled fibres – Saurer Autocoro 11
Saurer's Autocoro 11 in the Recycling Xtreme version is the cornerstone of a fundamental change in short fibre spinning. Autocoro 11 eliminates the worry of yarn breaks thanks to the Synchropiecing 60 seamless spinning technique, the new patented linear rotor cleaning and self-cleaning components that massively increase productivity and save labour costs at the same time.
After raw materials, energy is the second largest cost item in the automatic rotor spinning mill. Minimising these costs directly increases the profitability of spinning mills. Autocoro 11 uses 10% less energy than its predecessor and up to 48% less compared to older rotor spinning machines. The aim of sustainable spinning is to lose as little raw material as possible and, ideally, to spin everything into yarn. The Autocoro 11 with Recycling Xtreme features help to produce the best possible yarn from every blend, both in terms of productivity and quality.
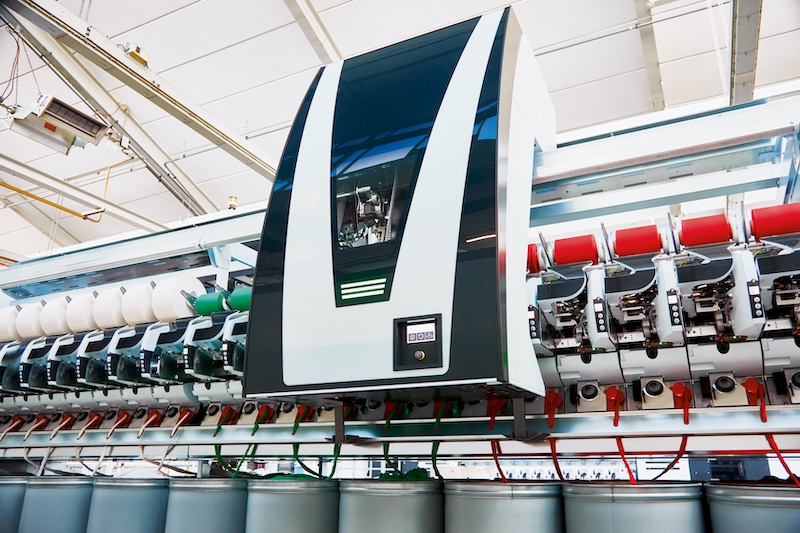
Trends in semi-automatic rotor-spinning with the BD series
The BD series, Saurer's semi-automatic rotor spinning line, has been recognised and used for more than 50 years in spinning mills worldwide. It is the ideal partner in the field of recycling and waste spinning. Rotor yarns spun on BD machines are in line with the current consumer trend towards sustainable textiles. The BD 8 sets new standards in economy and efficiency, making OE yarn production more competitive in all markets. BD 8 is available as a standard model or as an energy-saving model with Twinsuction, reducing energy consumption by 10% compared to previous models.
The unique Digital Joint Spinning In (DigiJSI) technology enables fast, fully automatic machine start-up for up to 600 spinning positions. Start up after a power failure is done within 10 minutes. The flexibility offered by the Multilot, Pilotgroup and Fancynation functions enable Saurer customers to react flexibly to the demands of the yarn market.
The BD 8 is supplied with the most reliable doffer on market having a doffing time of 10 seconds and available with up to four doffers. The doffer unit is available as an option for the BD 8 and as an upgrade for the BD 7. The BD 480 Plus, the entry-level rotor spinning machine, is also available with an automatic doffer unit (DU).
Ring spun yarns are fashionable
The spinning processes is influencing the yarn structure, touch, feel and wearability of the finished product. Think of the exceptional quality associated with premium shirting: it owes much to the time-honoured technique of ring spinning. Ring spinning technology offers a range of flexible options, some of which are unique to ring spinning; ring yarn, compact yarn, fancy yarn, core yarn and even duo-core yarns are possible.
Saurer offers the longest machine lengths up to 2016 spindles with the ZI 72XL, and upto 2056 spindles with the new Zinser 51 enabling higher productivity per square metre of mill area. In line with Saurer's E³ philosophy, energy efficiency has been the focus of the latest developments in ring spinning.
To meet the increasing demand for processing recycled materials, Saurer has optimised the ring spinning machine for processing mechanically recycled fibres. Thanks to its spinning geometry and equipped with the self-cleaning compact device Impact FX Pro, the ZI 72XL ring spinning frame and Zinser 51 both have a high tolerance for short fibres. Compared to rotor spinning, the challenges for ring spinning are higher when processing recycled fibres. In Saurer’s Sustainability Hub in Germany, we are constantly testing new material blends from customers around the world to develop new solutions and yarns.

Yarn quality starts with excellent spinning preparation
Just as fashion begins with yarn, the yarn begins with spinning preparation. The right combination of blowroom and card ensures excellent fibre utilisation and sliver quality, increasing the efficiency of the spinning process and improving yarn quality. Carding is where the base for the best yarn quality is set. Saurer is one of the leading suppliers of carding machines to Pakistan. The portfolio offers different card models, ensuring the right solution for every application. Furthermore, Saurer has cards specially designed for processing recycled fibres.
Autocard SC7 is the next generation of Autocard that creates a value increase within the fibre preparation chain. With its focus on automation, digitalisation, and ergonomics, Autocard SC7 helps spinning mill operators to obtain more production and higher quality with less labour.
Automation is the new normal
Automation is leading to enhanced process control, improved quality, and increased productivity. Automation solutions are increasing the mill’s independence from a scarce resource: manpower. Saurer is one of the pioneers of automation. The Bobbin Transport System (BTS), which links roving frames with ring frames, is already in use for decades; a sophisticated, highly efficient version of the BTS is installed at the spinning mill of Ibrahim Fibres in Pakistan.
At ITMA 2023 in Milan, Saurer presented studies of what will be the new normal in the coming future: AGVs for can transport and sliver feeding for the Autocoro 11 rotor-spinning machine and a piecing robot on the ZI 72XL ring-spinning machine. There is no such thing as a one-size-fits-all automation solution, but rather one that is customised to existing mill structures and customer needs. This is why Saurer has a complete engineering department to adapt our automation solutions to the specific needs of spinning mills.
SUN - Service unlimited
Saurer offers retrofit and upgrade solutions to reduce the energy consumption of existing spinning machines because every Kilowatt that spinning mills can save matters to our planet. Upgrade and retrofit kits are also available for processing recycled fibres. The Saurer service experts will advise customers on retrofit solutions to extend the life of existing Saurer machines and implement new features at the same time.
Texparts offerings
The team of Texparts will be present on booth B36 in Hall 3. Discover the latest Texparts product innovations for the textile industry: For ring-, compact- and rotor-spinning we offer a lot of components: such as high-quality drafting arms, long-lasting rings and travellers and energy-saving Eshape spindles, which can save upto 6% energy.