Recycling / Circular Economy
Re-fresh global and Soex join forces to establish the first complete textile waste recycling circuit
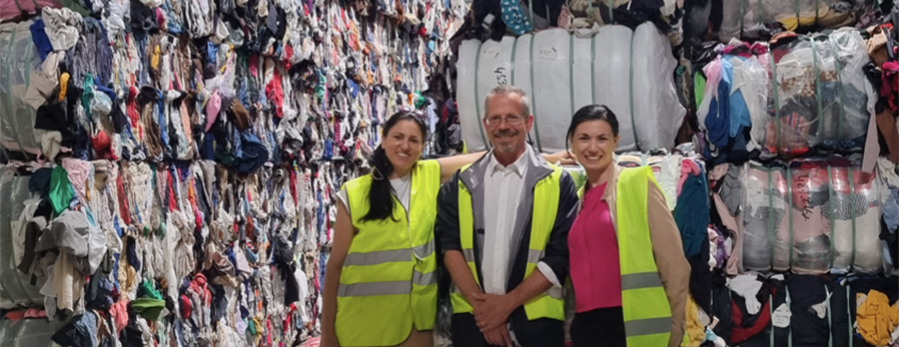
First product samples produced for the volkswagen group
The partnership between Re-Fresh Global and SOEX marks a significant milestone in the global effort to make the textile industry more innovative, sustainable, and environmentally friendly. Within this collaboration, Re-Fresh Global produced Re-SanPulpTM, an upcycled polyester fabric that was used to produce first demonstrator parts for the trunk of a current model of the Volkswagen Group.
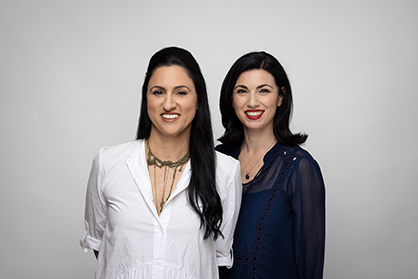
At the heart of this collaboration, made possible with the support of the Volkswagen Group Innovation and especially Konnect, the Volkswagen Group Innovation Hub in Tel Aviv, is the creation of a closed-loop textile waste recycling system. The automotive industry, facing significant environmental challenges, is one of the sectors that can benefit greatly from Re-Fresh Global's end-to-end solution.
A cornerstone of this collaboration is the establishment of a closed-loop system for textile waste recovery. This means that the material from the worn textiles used for the production of the Volkswagen demonstrator parts was not simply discarded after the clothing’s lifespan but was instead reused, recycled, and reintegrated into a value-adding production process. This innovative approach underscores the commitment of Re-Fresh Global and SOEX to a sustainable future.
"We are thrilled to be a part of this historic moment in textile recycling," said Viktoria Kanar, CEO of Re-Fresh Global. "This partnership underscores our dedication to creating sustainable solutions and reducing the environmental footprint in our industry. We firmly believe that this is just the beginning and that our collaboration with SOEX will drive further innovative developments."
SOEX brings its extensive experience and expertise in textile recycling to the partnership. Combined with Re-Fresh Global's SMART-UP Microfactory, which was implemented here as a pilot project, an upcycling process has been put in place to transform used textiles into high-quality raw materials, reducing resource consumption. Using the resulting raw materials, known as multifunctional fibers (Re-SanPulp), a product for the automotive industry was created for the first time. This end-to-end solution serves as a prime example of a closed-loop economy, from recycling textile waste to a finished product.
The next step in this promising partnership is the construction of Re-Fresh Global's end-to-end solution on the SOEX site, the SMART-UP Microfactory, where the full textile waste conversion process will be developed. This includes processing all types of used textiles, both from synthetic and natural sources, into high-quality raw materials in order to reduce resource consumption. For the first time, a product for the automotive industry was created from the synthetic raw materials, so-called multifunctional fibers (Re-SanPulpTM). The materials obtained from natural fibers, Re-ThanolTM and Re-NanoTM, are also used in a number of manufacturing industries as an alternative to virgin materials. This end-to-end solution is a prime example of a closed circular economy, from recycling textile waste to the finished product.
Roland Hovestadt, CEO of SOEX Textile Recycling Company, sees the establishment of international flagship projects as a significant opportunity for the entire textile industry: "By investing in the advancement of recycling processes and promoting innovative solutions like those offered by Re-Fresh Global, integrated into existing recycling processes, we can lead the entire industry towards a circular transformation. In the end, everyone benefits because this is how we remain sustainable for the future."
Both companies plan to expand their collaboration and apply the insights gained from this project to other areas of the textile industry. In Europe alone, approximately 7.5 million tons of textile waste are generated annually. The textile industry ranks as the fourth-largest global contributor to climate change. Re-Fresh Global's method can recycle up to 98% of the textile waste generated. The EU has already presented regulatory drafts, and the industry can expect strict requirements. The goal is to develop the textile industry into an integral part of a circular economy. The Extended Producer Responsibility (EPR) for textiles, which includes guidelines for product recycling, is already legally established in some European countries.
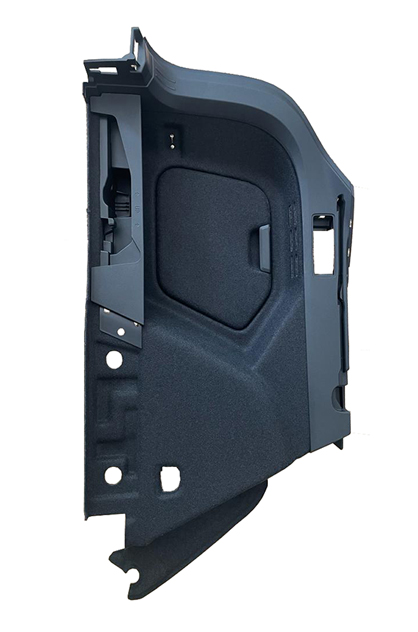
In this context, the significance and advancement of sustainable practices in the textile industry become particularly evident. Their promotion is essential for a sustainable future.