JEC WORLD 2022
DORNIER presents itself at the JEC world with end-to-end approaches to thermoplastic composites and three-dimensional preforms
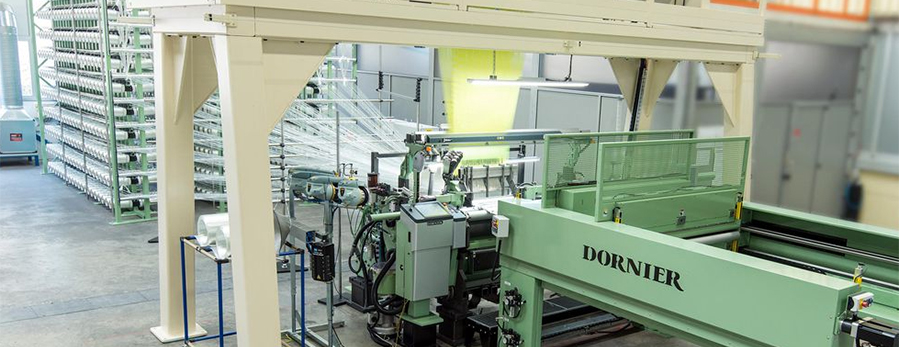
DORNIER presents itself at the JEC world with end-to-end approaches to thermoplastic composites and three-dimensional preforms
PROTOS® Line: With granulate and fiber to the semi-finished thermoplast product
Whether vehicles, airplanes, wind turbines or robots – fiber reinforced materials provide more economic efficiency, sustainability and weight reduction in areas such as e-mobility, energy and mechanical engineering. Semi-finished fibermatrix products based on unidirectional fiber reinforcements (UD tapes) play an important role in this context. The outstanding features are, most of all, short cycle times, good recyclability and easy processing. In order to provide a solution for the low level of availability of suitable UD tapes and prepreg semi-finished products, Lindauer DORNIER has now developed the PROTOS® Line (Polymer and Roving to Sheet). “The integral solution allows tailored manufacturing of high-performance intermediates, products easy to be further processed “, says Dr. Josef Klingele, Head of Composite Systems Product Line. First of all, the Tape Production Line PROTOS® TP produces either dry or fully impregnated tapes and afterwards processes them with the Tape Weaving Machine PROTOS® TW into high-performance semi-finished thermoplastics. DORNIER’s innovative production system is available for customer trials and sampling in the in-house technology centre.
P2 Mono Rapier Weaving Machine: Machine platform for special products
From roving fabric made of heavy tow to special fabrics made of ceramic fibres: Where many special solutions have been used so far, DORNIER is now launching a highly flexible machine platform with the P2 Mono. The new monorapier weaving machine is available in different versions, enabling customers to produce many special products on one platform. “In combination with the DORNIER Zero Twist Feeder, even two weft colours can be inserted twist-free, at high speed and with a wide variety of patterns”, adds Dr. Josef Klingele.
P2 Roving Rapier Weaving Machine: The new standard
DORNIER has acquired the know-how for customized solutions for the composites industry over the course of more than 50 years in which the company’s roving weaving machines have set the international industry standard for the production of high-performance fabrics made of carbon, glass and aramid fibers. Their successor will now be presented in Paris: the P2 Roving. Thanks to its higher frame stiffness, improved filling insertion performance, the maintenance-free, patented DORNIER SynchroDrive® drive concept and an optimized positive center transfer, it is already considered as the most flexible rapier weaving machine in the world. According to Product Manager Michael Langer, its improved shed geometries ensure an absolutely symmetrical warp thread path, which means that carbon fabrics for high-end applications can now be produced even better and more reliably. Furthermore, innovative waste saving devices reduce weft waste and allow an efficient production with optimal use of material.
TRITOS® Line: Simple production of complex fiber structures
In high performance applications, 3D fabrics are superior to layered fiber composite structures due to their good damage tolerance and high dynamic load capacity. “The DORNIER TRITOS® Line (Textile Roving into Three-dimensionally Oriented Structure) combines this material superiority with highly productive, industrial production”, explains Dr. Britta Skoeck-Hartmann, Productmanagement at Composite Systems. With fabric thicknesses of up to 100 mm and the patented DORNIER Weft Saver (DWS), the preform production line TRITOS® PP is ideally suited for the use in areas with high cost pressure.
Visit us in Hall 6 | Booth M72.