India ITME 2012
Virtual Reality provides deeper insight into the manufacture of fibers, yarns and nonwovens
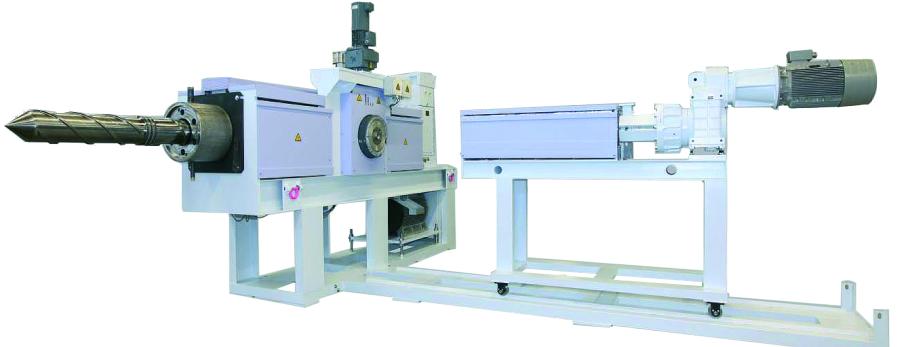
With its Virtual Reality Showroom, first unveiled at the ITMA in Barcelona, the market leader in all matters relating to manmade fiber production is offering a completely revolutionary perspective on processes, machines and systems: an experience rather than merely a view. Virtual reality will enable the trade visitors to “embark” on a journey through the production processes and systems, practically taking them from the raw material all the way through to the finished yarn package.
The benefits of this innovative presentation method are clear to see: customers can explore the entire system, whereas individual components, at most, could be shown to date. Furthermore, users can control the view in accordance with their specific requirements, explore key components in greater detail and examine the insides of the systems. In addition to the 300 ton/day staple fiber system, the melt-blown system and the BCF system S+ from Oerlikon Neumag, the program now also includes Oerlikon Barmag’s technology for the entire process chain – from the melt to the yarn and from the poly-condensation system all the way through to the finished FDY package.
Focus on industrial yarns
The textile machine builder will be placing the information spotlight on industrial textiles both with the Oerlikon Barmag filament yarn systems and the spunbond system from Oerlikon Neumag’s non-woven portfolio. Potential applications include geo-textiles, roofing, carpet backing, filtration systems and automotive applications such as seatbelts, airbags and tire cord, for instance. There is currently considerably more movement within the non-woven market and – in terms of growth rates – this will in turn overtake those of hygiene products in the future. In view of the numerous infrastructure projects, the Indian market offers huge potential particularly for geo-textiles.
Sustainable technologies
Sustainability is also a hugely important trade fair topic for the manmade fiber specialists at the Oerlikon Group: energy efficiency and CO2 emissions during the filament yarn spin-dyeing process using the Oerlikon Barmag 3DD mixer are also important factors here. To this end, a piece dyeing process requires around 30 times as much energy as masterbatch dyeing processes, while also emitting approximately 30 times the amount of CO2. Incidentally, the dyeing masterbatch results are more even, which is why textiles dyed using this method are the preferred choice in the particularly critical automotive sector.
One important competitive advantage of the Oerlikon Neumag 300 ton/day staple fiber system is the considerably higher per-ton fiber profitability vis-à-vis smaller systems, an achievement that is predominantly down to the superb energy efficiency of the new large-scale system. Experience acquired by a Chinese customer reveals production costs that are at least 25% lower and a three-fold increase in the output.

Pic: Oerlikon Neumag’s S+ is the latest three-end system of the BCF carpet yarn systems market leader
In the carpet yarn sectors, the focus is on the BCF system S+. Once again, efficiency – in addition to productivity – is the primary character trait of the new standard machine of the BCF systems market leader, Oerlikon Neumag. As the successor to the S3 and the S5, it combines the benefits of a fast, efficient and user-friendly machine with tried-and-tested components.