ITMA Asia + CITME 2024
Saurer at ITMA Asia 2024 – Leading technology for the yarns of tomorrow
Saurer's spinning and twisting solutions incorporate leading technology for the yarns of tomorrow and offer high flexibility to respond to the changing demands of the yarn market.
Recycled fibres: All the machines can be configured to process recycled fibres and their blends, which will be in high demand in the future. Saurer machines are designed to maximise fibre utilisation to minimise waste in pre-spinning and spinning.
Flexibility and efficiency in yarn production: low pilling yarns, fancy yarns, core yarns, compact yarns, siro compact yarns, high quality twists or sophisticated carpet yarns, and much more can be produced with maximum efficiency.
Saurer yarn brands: To ease marketing, we created yarn brands to be used for free for our customers: Belcoro – for rotor yarns spun on Autocoro, Belleo – for rotor yarns produced on BD machines and Belairo – for yarns supplied from Autoairo air spinning machines.
Fabric samples made from Saurer yarns: The touch and feel of recycled yarns produced is important for the end user and fashion industry. At ITMA, Saurer is exhibiting various end products, such as shirts, T-shirts and hoodies, all made from yarn supplied by Saurer customers.
New Autocard SC 8: High performance. Automated. Monitored.
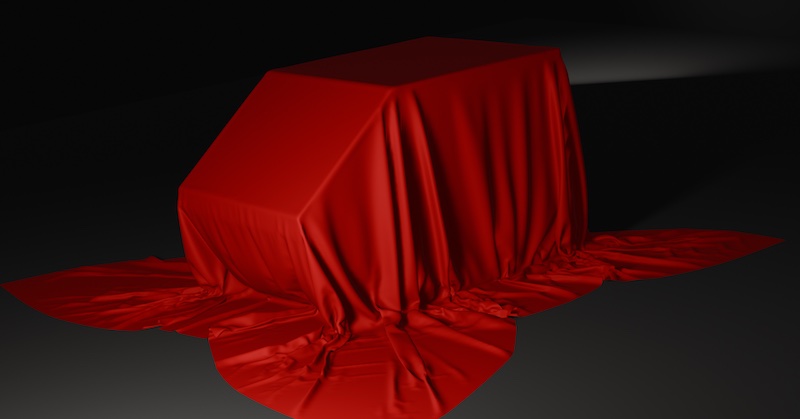
Thanks to the new design concept, with a functional and modern machine design the SC 8 offers a lot of benefits for customers. To achieve highest productivity, the SC 8 owns the largest carding section of the industry. SC 8 has a carding width of 1.38 metres and a carding cylinder diameter of 1.46 metres resulting in an impressive carding section of 4.8 m2. The benefit is better fibre uniformity and careful treatment of the fibres. To keep the carding gap and sliver quality constant, the card does use automated settings and a smart monitoring with integrated temperature detection. Rising temperatures will make the carding gap smaller and lead to quality deviations, which is avoided with the temperature monitoring of the revolving and stationary flats.
Customers benefit from higher material utilisation rates and increased quality thanks to detection and adjustment of fibre dropping. These features are especially beneficial when producing recycled fibres. The pneumatically assisted piecing-up technology simplifies and speeds up the operating process and significantly improves production efficiency. Less skilled workers can easily operate the automated Autocard SC 8.
Zinser 51: High speed spinning. Flexible. Energy-saving.
At ITMA Asia, Saurer will present the flexible Zinser 51 ring spinning machine and demonstrate during the exhibition the production of Siro Compact yarn. The extremely soft touch and smooth surface of these yarns are outstanding in knitwear and highly appreciated in the market. To produce high quality compact yarns or to process recycled fibres, the new Zinser 51 can be equipped with the reliable compact units Impact FX and Impact FX pro.
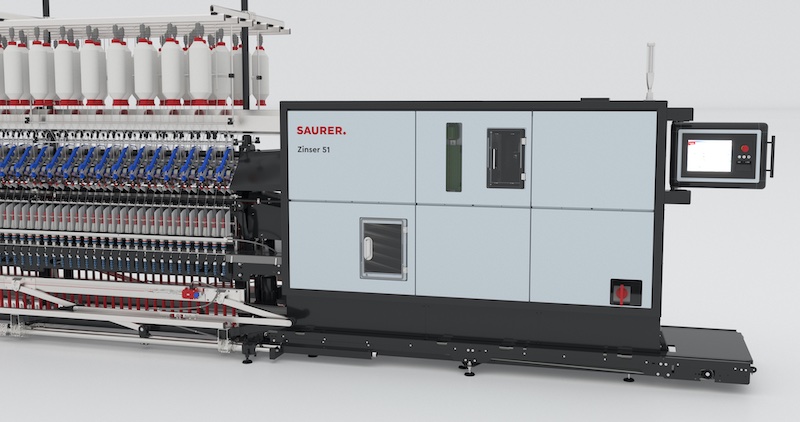
The robust machine design has been developed with a focus on improving efficiency, saving energy and increasing production flexibility. The machine is easy to operate and offers a range of centralised settings that ensure consistent quality along the entire length of the machine. The new NSD-i automatic drafting system monitors all drives along the entire length of the machine and speeds up lot changes. With up to 2056 spindles, customers can achieve maximum productivity. The robust centre drive ensures consistent yarn quality on extra-long machines.
Zinser 51 energy monitoring allows customers to optimise settings and compare energy costs. Remarkable energy savings of up to 10% are achieved with the new suction system, energy-saving drives and self-cleaning waste chamber. High-end components such as the Texparts Eshape spindle and Spinnfinity result in further energy savings of 6% and enable high-speed spinning of up to 30,000 rpm. Flexible, tailor-made automation solutions are available for the Zinser 51, from roving bobbin transport to automated doffing and cone transport systems.
Autoairo: Think progress. For pilling free fabrics. Suitable for cotton.
Saurer's Autoairo air spinning machine spins at the highest speeds and is extremely efficient thanks to the high level of automation built into the machine. Due to its high speed and small footprint, air spinning can be an economical alternative to existing spinning methods. The Autoairo can process carded or combed cotton and cotton blends. Viscose and blends with polyester are also often processed on the Autoairo.
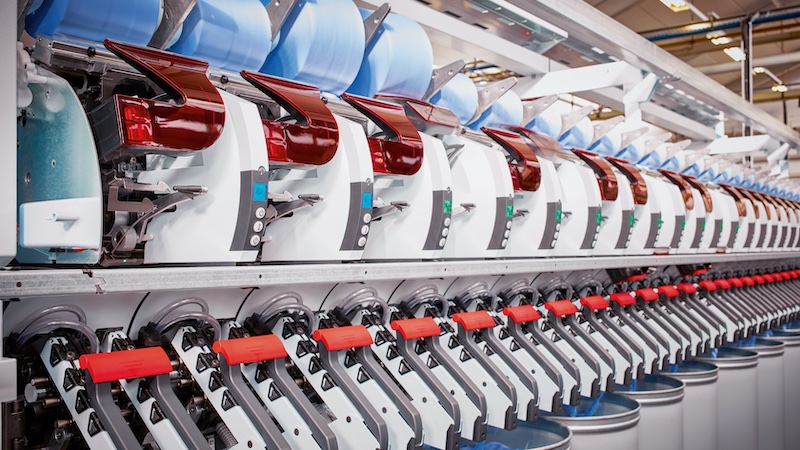
Xinyuan Wang, Sales Manager of Saurer China explains: "The outstanding features of Autoairo yarns are low hairiness and low pilling. Autoairo can also produce conical packages, ideal for use in knitting mills. At ITMA Asia, the Autoairo model will be running with a take-off speed of up to 500 m/min. Don't miss the chance to see this amazing technology producing cotton yarns on our booth in Shanghai. Come and touch Belairo yarns and fabrics, produced on Autoairo.”
Autocoro 11: Fully automated. Energy saving. Ideal for recycled fibres.
The fully automatic rotor spinning machine Autocoro 11 offers an additional 10% energy saving compared to the Autocoro 10 and more powerful automation. Take-up speeds reach up to 250 m/min and rotor speeds up to 180,000 rpm.
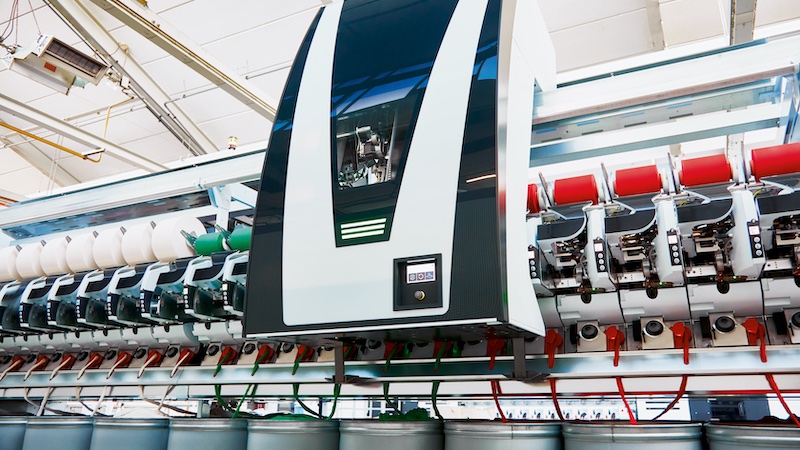
With the Autocoro 11 Recycling Xtreme edition, Saurer offers a solution that is optimised for extremely short mechanically recycled fibres, running with a take-up speed over 230 m/min. Dust and fibre fly make the processing of recycled fibres a big challenge. The secret of the Recycling Xtreme is among others a new cleaning system for the rX yarn guides, special dirt-repellent surfaces for the opening rollers and fibre beard supports which can be easily adapted to very short fibres. The new patented rotor cleaning technology keeps the rotor groove clean, and the new extraction system removes waste even more efficiently.
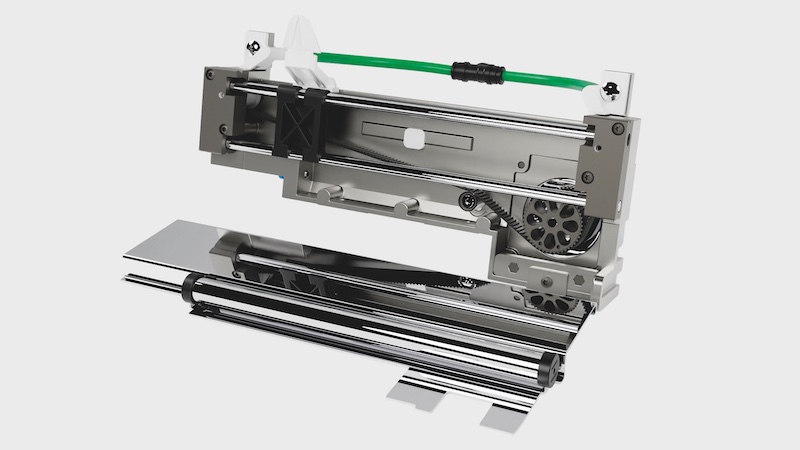
The Synchropiecing 60 technology now increases the Autocoro 11's piecing capacity by 65%, allowing it to maintain high efficiency even with the high breakage rates that typically occur when using recycled fibres and will guarantee a fast machine start. In addition, the Autocoro 11 is equipped with more powerful automation and an LED-based operator guidance system to increase efficiency by speeding up operator interactions. High-quality Autocoro yarns are well known in the market as Belcoro yarns.
BD 8 & BD 480 Plus: Think economically. Energy saving. Ergonomic design.
The semi-automatic rotor spinning machine BD 8 is the ideal partner for economic recycling and waste spinning. The new Twinsuction offers up to 10% energy savings compared to the previous model. The unique Digital Joint Spinning In technology enables all 600 spinning positions to start automatically after a power failure, so that the machine is back in production within 10 minutes. The BD 8 can be equipped with up to four automatic doffer units (DU). The doffer changes the packages without interrupting the spinning process. Take-up speeds of up to 230 m/min, rotor speeds of up to 120,000 rpm, an LED operator guiding system to increase machine efficiency and ergonomic machine operation are additional features of the BD 8. The Multilot, Pilotgroup and Fancynation functions offer customers high flexibility in yarn production.
Belleo is the new brand name for top yarn quality produced in an efficient and sustainable way on BD machines. The needs of the textile industry are Saurer's top priority, therefore the semi-automatic rotor spinning machine BD 480 Plus is available with an automatic doffer for package change. With two automatic doffer units (DU), customers can benefit from increased efficiency and a reduction in workforce.
Texparts. High-quality components. Made in Germany.
With the Texparts product line, Saurer offers high-quality components for the textile industry, including drafting systems and spindles, spinning rings and travellers, as well as bearings for ring and rotor spinning, winders and twisters. Texparts components ensure excellent yarn quality, maximum productivity and, for a range of products, energy savings.
The new Texparts Eshape spindle has a reduced wharve diameter of 17.5 mm. Combined with the Spinnfinity zero underwinding system, Eshape enables remarkable energy savings of up to 6%. Spinnfinity is now also available in a new version for worsted and coarse yarns with an adapted yarn cutter. Texparts offers a wide range of high-quality rings and travellers, which is constantly being expanded to meet the needs of spinning mills.
Sun – Service Unlimited: Service solutions. Lasting a machine’s lifetime.
Saurer offers service solutions for a long and sustainable life for all Saurer machines. Customers can equip existing machines with the latest upgrades to maximise productivity or add new features for recycled fibre processing. The updates and upgrades, smart preventive maintenance services or technology kits with Saurer original parts will keep the mill's production competitive throughout the life of the machines. There are many solutions available to improve the quality, performance and profitability of spinning mills. Discover our rX Recycling Xtreme Autocoro upgrades. Saurer's Customer Support experts will be on the booth to explain the benefits of the various solutions adapted to the specific needs of each mill.
PrimeTwister: Conquer the market. Exceptional flexibility.
At ITMA Asia, Saurer will be exhibiting the PrimeTwister, a state-of-the-art two-for-one twisting system designed for staple fibre yarns, including cotton and cotton blends, as well as sewing threads. This latest iteration offers exceptional flexibility with a wide range of yarn counts, making it an ideal choice for a variety of production needs.
The PrimeTwister features a remarkable reduction in energy consumption of up to 40%, achieved through innovative spindle geometry and advanced spindle bearings. In addition, the high-quality yarn guide elements ensure consistently superior twist quality, setting new industry standards. With its compact design, the PrimeTwister requires less production space. As a result, the PrimeTwister not only minimises building and air-conditioning costs, but also streamlines operations. Its low maintenance and service requirements, combined with reduced assembly and installation times, make it a highly efficient solution for twist manufacturers. Combined with Saurer's renowned reliability, the PrimeTwister is an economical and future-proof investment, and its unbeatable price/performance ratio ensures a high return on investment.
CompactTwister: Reliable. Advanced drives. Energy saving.
The CompactTwister features an advanced spindle and drive design that ensures low power consumption and short doffing times while maintaining a low yarn breakage rate. With balloon limiters, energy-saving spindles, optimised drives and many other innovations integrated into the CompactTwister, significant energy savings can be achieved. Twisting recycled yarns with the CompactTwister increases strength for downstream processing and expands the range of applications for the yarn.
CableCorder CC5: Be ahead with Saurer. For tire cord.
In the field of high-quality tire cord production, the technologically advanced CableCorder CC5 stands out with a host of innovations designed to keep Saurer's customers at the forefront of the industry. Saurer's team of technology experts is dedicated to support customers worldwide in optimising both yarn production and quality. The Saurer CableCorder has always played a vital role in the tire industry, and the latest generation offers users significant competitive advantages: reduced energy consumption, an intelligent spindle concept for energy efficiency, advanced quality monitoring systems, improved ergonomics, and flexible automation and digitisation solutions. The patented energy-saving technology has been further refined with new hardware and optimised software, making the CableCorder CC5 more economical than ever before.
TechnoCorder TC2: For industrial yarns.
The TechnoCorder TC2 can process a wide range of yarns and offers a yarn lubrication device to ease further process steps. The latest feature, PreciWinding, (TC2 Plus) features a newly developed take-up area for producing twist packages of a very high quality.
Processing of glass filament yarns: Unleashed efficiency. Highest quality.
Saurer's CakeFormingWinder is perfectly aligned to customer needs and uses the latest glass filament winding technology to meet the high demands of the market. Its innovative rotor technology and high-speed traversing system enable efficient production of high-quality glass filament packages. Seamlessly integrated into the process chain, the CakeFormingWinder features advanced components such as patented bearings, a water-cooled drive box and automatic greasing systems.
In addition, the GlassTwister is a high-performance ring twister designed for uptwisting glass filament yarns and has gained strong market acceptance. Saurer's twisting systems offer exceptional variability and flexibility, especially for plied and hybrid yarns, with the VGT-P model improving production efficiency and quality. The PreTwister units and the DownTwister machine work together to produce balanced multiple yarns of the highest quality.
Fibrevision: Synthetic yarn monitoring. For DTY, IDY, BCF and POY processes.
Saurer's aim is to guarantee yarn quality in synthetic yarn production from the start of the process to the final package. Saurer Fibrevision has developed yarn quality monitoring and grading systems to minimise waste and maximise quality by detecting and recording every single yarn fault. Quality data is recorded several times per second to optimise production and improve quality. Quality monitoring is equally beneficial for both standard melt spinning processes and the use of recycled synthetic fibres. With the increasing use of recycled material, quality monitoring and grading materials is becoming increasingly important as unpredictable defects occur more often when processing recycled polymeric material.
Fibrevision's Total Quality System TQS® covers a wide range of yarns from polymer spun materials such as POY, FDY yarns to texturized DTY yarns. Depending on the application, industry and requirements, a variety of monitoring sensors are available, each with a specific use in mind: Saurer offers Unitens® tension sensors for monitoring DTY yarns, FraytecFV2® & Univis2® optical sensors for monitoring POY, FDY, IDY yarns and TQS® Spin Finish sensors for oil monitoring of POY, FDY yarns. Each sensor looks for specific quality defects such as broken filaments, interlace level, spin finish and yarn diameter variation. The Fibrevision systems are equally valuable when used for on-line monitoring of each thread line on the machine, providing 100% real-time quality assurance. In addition, Saurer offers off-line monitoring for further laboratory sampling or at-line instruments for product development.?
Automation and digitalisation solutions. For spinning and twisting.
Saurer's automation technologies aim to streamline operations, minimise human error and significantly reduce operating costs. Our automated systems enable yarn manufacturers to optimise their production lines, increase output and ensure consistent, superior yarn quality. Saurer offers a wide range of automation equipment for roving, ring spinning, compact spinning, rotor spinning, air spinning and twisting, depending on the customer's needs. The latest AGVs improve handling in spinning and twisting mills, reducing lead times, increasing productivity and saving on labour costs. Senses is Saurer's digital data analysis tool enabling customers to react faster to quality deviations or reduced efficiency. With Senses, spinning and twisting customers have a digital overview and control of their production machines.