ITMA 2019
“MAKE IT YOURS"
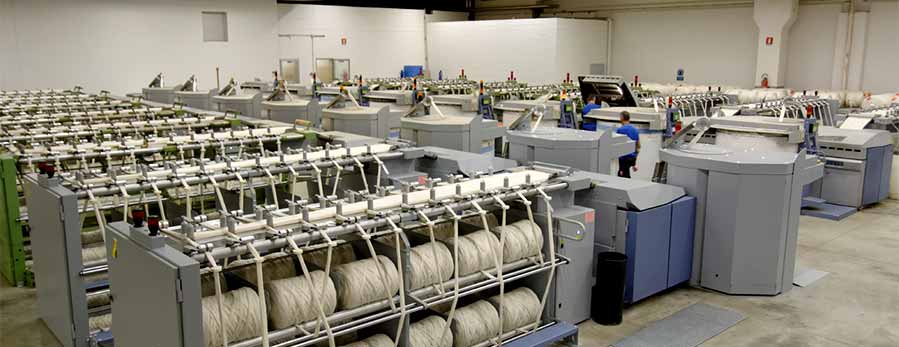
French Machinery@ITMA 2019
French Textile Machinery Manufacturers are offering hardware, software and services.
“In fact, she adds, often, even before the investment decision is made, the machinery manufacturers’ R&D teams work directly with the customers to design specialty machines”.
R&D and service are embedded in the French Textile Machinery Manufacturers’ DNA. It has always been. Remember that Jacquard, the star of the textile machinery invention was French! The manufacturers are agile SME’s run by entrepreneurs with long term objectives. The managers have very often a long history and strong ties with their companies. Then, in such SME’s the information flows very rapidly between the commercial, technical and research departments. This is how it should work and it does. It allows to go much further than purely commercial relationships with the customers; trust and confidence are not buzzwords.
That’s why France is the sixth textile machinery manufacturer worldwide with an annual turnover of about 1 billion Euros (1,15 billion US dollars). They are particularly strong in long fibre spinning (wool, acrylic ...), yarn twisting and control (including technical yarns), space-dyeing, heat setting for carpet yarns, carpet systems, dyeing and finishing, felts and belts for finishing processes, nonwovens, air conditioning of textile plants, and recycling processes of textile materials.
Evelyne CHOLET concludes “We have worked hard to welcome our customers on our booths at ITMA, and surprise them; my message to them about our machines is: make it yours!”
Here are some examples of the French exhibitors:
NSC SCHLUMBERGER Hall 6 Stand A 107
NSC, global specialists in machines for processing long staple fibres such as wool and wool-like fibres, are pleased to welcome their visitors to the forthcoming ITMA on their 500 m2 stand and show them new versions of NSC’s core machines:
The ERA combing machine in a multi-servomotor drive design. With this new drive, most of the settings will be possible via the main control screen. A wide range of materials have been tested on this new ERA combing machine and results are promising mainly for delicate material which has to be processed in a gentle manner. Also, despite the additional motors, power consumption remains low.
The GC chain gill also benefits from additional axes driven by servomotors which allows more settings on the main control screen.
For its FMV vertical rubbing frame, NSC has also developed a multi servomotor drive for the axes. The bobbin build-up also benefits from a servomotor-controlled drive.
All these new servomotor drives will allow more precise settings than using standard gearboxes which will enhance textile quality.
Furthermore these new drives and technology allow recipes to be saved on each machine, data exchange between machines will be possible through a Manufacturing Execution System (MES - Industry 4.0), as is remote access to the machines in case of incidents through an Ethernet connection.
All these new technologies on NSC machines follow the global trend towards user-friendly, tool-less machines, with accurate settings via the control screen to enhance textile quality.
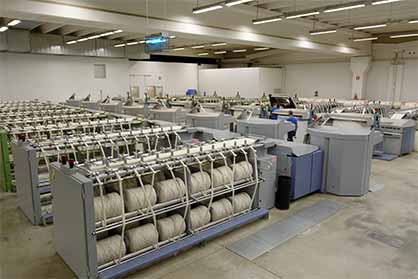
LAROCHE Hall 5 Stand C 106
At ITMA, LAROCHE, world leader in fiber processing equipment, will display the following machines:
Airlay type “Flexiloft 2600” with improved web uniformity and weight range. From 2.4 up to 4.0 m, the Laroche Airlay can run all types of fibers (synthetics, natural, recycled....,) and blends of fibers and solid particles (foam chips, plastics, wood chips). This allows to make smart products from renewable resources and from wastes that are otherwise discarded. Thermobonding or needle punching trials can be run in the technical center with a Schott and Meissner oven or with an Andritz needle loom.
Tearing machine type “Jumbo 2000” for high capacity recycling of all types of textile wastes including post-consumer clothing and carpet wastes.
New generation of ultra-high-speed Edge trim opener type “Nextrim 500” for on line or off line recycling of light weight nonwoven edge trims.
The LAROCHE teams will be available to show samples and discuss their latest developments in:
- decortication and refining of bast fibers for technical applications, - new generation fiber blending and dosing lines,
- 3D web forming,
- automotive waste processing.
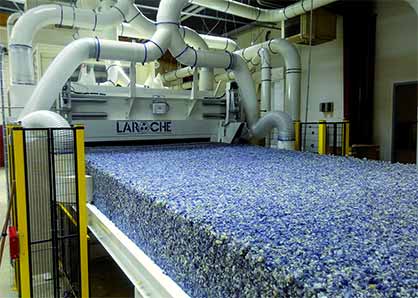
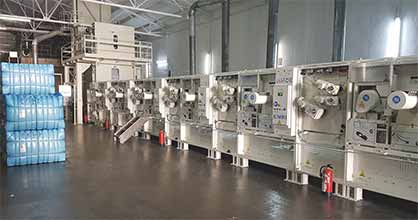
SUPERBA Hall 6 Stand D 206
Carpet designers and manufacturers are looking to differentiate themselves.
Thanks to the latest version of the MCD3 Space-dyeing machine, combined with the new MF400 texturization device, and a heat-setting line, it is now possible to produce carpet yarn out of polyester, polyamide, polypropylene, acrylic, viscose or wool, in one continuous single-step-operation, more energy efficient, web connected, and almost pollution-free.
With the ‘one pile – one color’ process, or thanks to the new ‘bi-color printing’ technology, the space-dyeing process has been renewed and undergoes a new boom. This technology enables to get yarn directly usable in carpet and rugs to realize innovative design. It is now possible to obtain up to 15 different color shades on the same yarn in one single working pass.
To bring more value to the yarn, it is also possible to insert the texturization device MF400 between the dyeing machine and the heat-setting line in a one-pass process.
To fix the dyestuff in the fiber and lock the twist, the heat-setting lines are directly connecting to the upstream processes, thus producing a soft-touch and durable carpet yarn. Whatever the fiber type, Superba is proposing the right solution:
The TVP3 with its saturated steam under pressure process is the right choice when pinpoint effect and durability are the dominant requirements sought for PA, PET, PP or wool and blends.
For acrylic, the saturated steam at atmospheric pressure at 100°C will be used: the LV3 line for raw yarn, or the DL5 line for space-dyed yarn.
At the line outlet, the B401 automatic winder, that can handle up to 96 bobbins, is the perfect solution with the highest rate of automatic doffing success and a proven reliability.
Each of these processes are now linkable to VANDEWIELE Texconnect system in order to optimize raw material use, plan maintenance operations, and thus reduce downtimes, waste, environment impact and increase energy savings.
At ITMA, SUPERBA will unveil a new innovative global process from the creel to the winding.
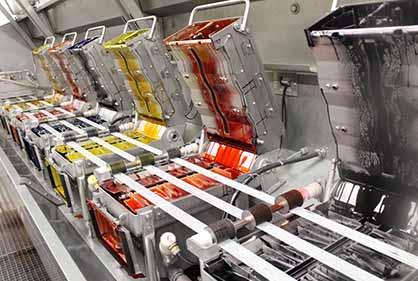
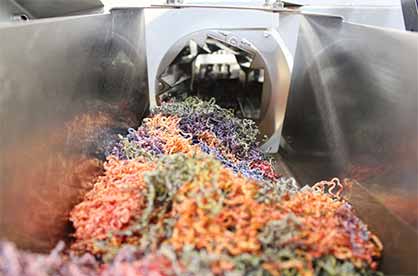
FIL CONTROL Hall 6 Stand B 203
The sensor expert, FIL CONTROL develops and produces yarn sensors and yarn cutters for the textile machinery industry.
With FIL CONTROL headquarters in France and Fil Control subsidiary in China for the Asian market, the company is staffed with the most competent team members in order to provide all customers with the highest quality products at the best price. The company puts all its effort and energy to understand and design technological and commercial answers to the textile industry’s constant evolution. All around the world, major textile manufacturers are trusting Fil Control’s solutions in its 3 major fields:
- yarn cutters, which can satisfy all kinds of personalized and bespoke demands,
- yarn sensors, utilizing capacitive, optical, reflective, piezoelectric and strength gauge technology,
- hall effect sensors, installed on numerous different kinds of application, such as motor rpm counting.
At ITMA a new step forward in the optical detection R&D will be unveiled. Indeed, it enables to detect yarn thinner than ever before, with to-and-fro motion but also with linear motion.
On top of all, the visitors will discover how the sensors and communication programming ability will follow the textile machinery manufacturer development into industry 4.0.
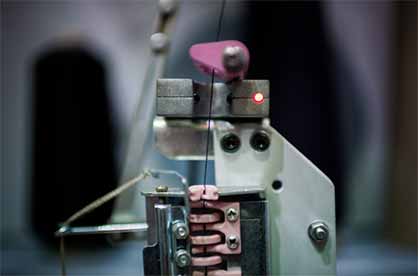
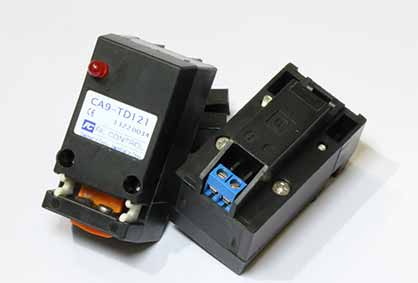
PETIT SPARE PARTS Hall 6 Stand B 202
PETIT Spare Parts holds the exclusive worldwide trade of the original spare parts for all ICBT fine count machines. Its technical staff received their training from the historical manufacturer, now gone. Petit does not only sell parts from catalogues, but provides solutions, whatever the equipment, whatever the location.
PETIT has more than 20,000 spare parts references in stock, at carefully studied and negotiated prices, as well as all the necessary drawings for the realization of parts conforming to those of original. No copies or forgeries!
Built on our experience in covering, twisting and texturizing as well as export skills, PETIT Spare Parts, a company of the PETIT SA group, specialized since 1946 in the trade of accessories for all textile machines, all brands combined, can thus meet all the customers’ requests, at national and international levels, for the maintenance of the equipments: diagnosis, repair, dismantling, remantling.
PETIT Spare Parts is a company that combines historical know-how and worldwide logistics expertise to support its customers on their way to success.
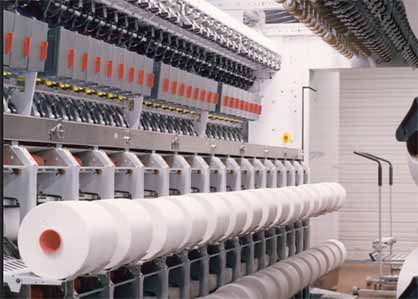
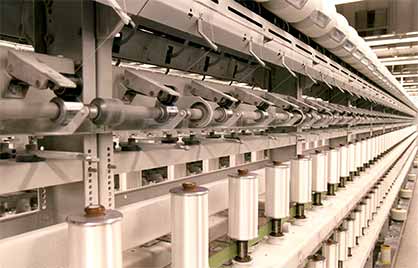
AESA Air Engineering Hall 8.1 Stand B 211
With offices in France, India, Singapore and China, AESA is a worldwide leader in air- engineering for all textile production processes of natural fibers, man-made fibers and filaments in their different stages: spinning, knitting, weaving, hosiery, different types of nonwovens and fiber productions, as well as dyeing and finishing.
AESA supplies air conditioning, ventilation and waste collection systems. In order to reach a lighter footprint with general production benefits and cost savings resulting from a better energy and environmental efficiency, customers are using AESA know-how and experience of many years in design and implementation of air handling systems.
With the regional offices and sales agents being present in most major countries, AESA provides a network of service centers close to customers.
Established systems like AESA-Flexicontrol in spinning and weaving factories, allowing fully automatic adjustment of consumptions to the actual needs, as well as the Weave Direct systems offer substantial reductions in power cost combined with more accurate room and process conditions.
The user-friendly and accurate Digivent control and monitoring system is communicating in interactive screen functions and is allowing a wide usage of recorded data for analysis, statistics and housekeeping.
EBELMANN Hall 4 Stand B 210
Sspecialized in hard materials' machining, 80 % of EBELMANN’s production is dedicated to the textile industries (special cutting devices). Thanks to constant technical innovation, equipped with fully digitized machining centres at the leading edge of technology, Ebelmann contributes, with its customers and partners, to the enhancement of their production resources by offering reliable high-performance solutions like special cutting devices specially drawn for industrial textile machines.
EBELMANN offers a manufacturing service and a re-sharpening service for all types of cutting devices (made in tungsten carbide, high speed steel and ceramic).
For technical fibres as Kevlar®, carbon or glass, EBELMANN manufactures very special scissors, with carbide tungsten blades, in association with polycrystalline diamond inserts.
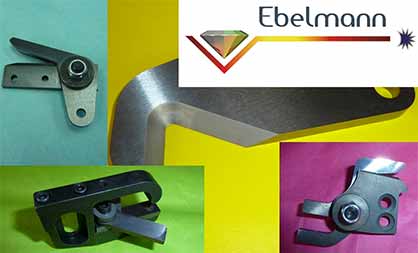
MALLEIN Hall 4 Stand B 213
MALLEIN is a specialist of the beams for warping and weaving, able to answer to all needs of the textile activity. The entire integration of its aluminum foundry and all of its production facilities allow Mallein to answer to all specific enquiries particularly thanks to its know-how in special aluminum alloys.
MALLEIN will exhibit some of its new aluminum canisters at ITMA, canisters that are improving each year, in order to produce them stronger and with a great geometric precision. It will also propose a flange development for the big barrels that are adapted for delicate fibers such as carbon.
MALLEIN is certified ISO 9001 V 2015, ISO 14001 V 2015 and OHSAS 18001 V 2007.
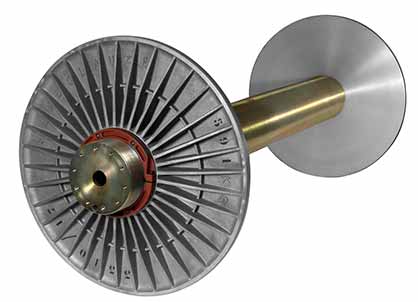
ALLIANCE Machines Textiles Hall 2 Stand B 318
More air, less water are used in ALLIANCE machines granting quality as well managing more and more savings in treatment costs.
At ITMA, the Rotora dyeing machine, by means of a rotating beam, will be shown with an integrated drying device. This combination will allow «wet» treatment for both standard and technical fabrics and to achieve drying inside the machine before off loading.
Riviera Eco Green: « round » type dyeing machine with very low liquor ratio (1 :2 to 1 :3). Thanks to its air blowing system, tubular or opened knitted as well as woven fabrics can be dyed free from creases marks. Machines from 10 to 1000 kg capacity, storage baskets in various widths can be delivered, allowing dyeing of very light fabrics (100 g per meter) as well as very heavy ones (2000 g per meter).
All the machines like Futura (long type dyeing), Zephyra (finishing machine for fabrics in rope form), Labojet as well as machines with very large capacities will be presented in details thanks to augmented reality system with 3D lenses.
The customers will be offered to use a software to estimate very precisely their own annual savings thanks to Alliance machines.
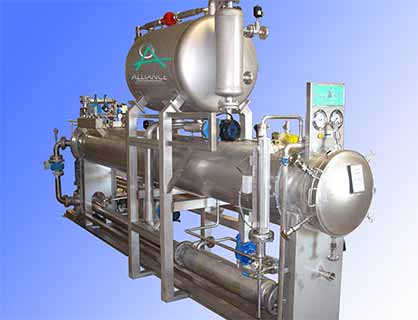
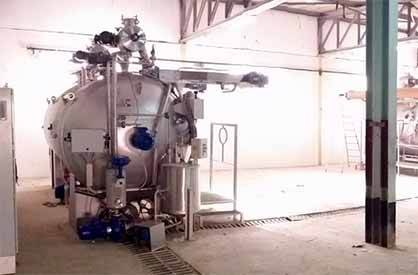
ROUSSELET Centrifugation and CALLEBAUT de BLICQUY Hall 2 stands B 316-317
- Rousselet Centrifugation is a specialist in batch or continuous hydro-extractors.
- Callebaut de Blicquy in dyeing or bleaching autoclaves as well as up-stream and down-stream equipments (press for cake, energy recovery equipment, cake breaker...).
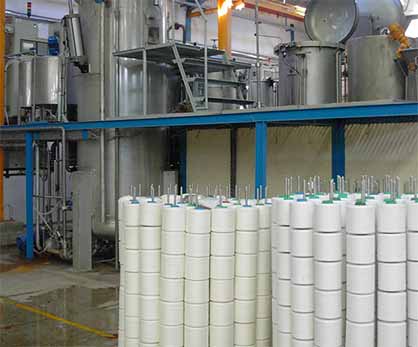
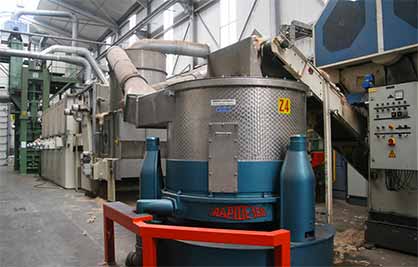
On their combined stand, they will be exhibit:
- one autoclave from Callebaut de Blicquy type V18-27 for bleached cotton cake diam 1,600 x height 2,700 mm, cake weight 1,600 kg,
- one continuous impregnation vat from Callebaut de Blicquy for continuous bleaching for cotton or fiber treatment, capacity 150 kg/h,
- one Optilab from Callebaut de Blicquy, unique lab scale dyeing equipment,
- one ADP from Callebaut de Blicquy, equipment to be integrated on dyeing autoclave for cycle optimization allowing savings on water, energy and dyeing products,
- one continuous hydro-extractor from Rousselet Centrifugation type SCPC150VxTE for hydro-extraction of short textile fibers in loose stock after treatment, capacity 1,000 kg/h of cotton,
- one batch hydro-extractor Rousselet Centrifugation from type SC120Vx, polyvalent hydro-extractor for garment, fabric or hosiery, capacity 110 kg of dry textile,
- and, a very “real” mock-up of dyeing house, complete from bale to bale, with all the required process machineries for a daily production of 30 metric tons/day of acrylic fibers in loose stock form or tow.
DOLLFUS & MULLER Hall 2 Stand C 202
The endless felt and belt manufacturer, Dollfus & Muller manufactures specialized endless felts and endless belts especially for the finishing and nonwovens factories.
Dynajet is a sales department of Dollfus & Muller specialized in fabrics for ink jet printers and wide widths fabrics for theaters and events.
The product range includes :
- compacting felts for knit finishing,
- sanforizing felts for denim and woven fabrics finishing,,
- printing dryer belts for textile printing,
- sublimation blankets for transfer printing,
- decatizing felts for wool finishing,
- dryer belts for thermo-bonding ovens,
- tensionless dryer belts for knit finishing.
Dollfus & Muller offers greatly improved compacting felt for knit finishing with major evolutions. The compacting felt quality brings a special care to the fabrics thanks to its smoothest surface, has an excellent guiding and the best compacting rate.
The Dollfus & Muller sanforizing palmer felts are ideal for denim producers.
Furthermore, Dollfus & Muller manufactures durable printing dryer belt qualities. These print dryer belts are the extremely durable specially designed for pigment printing of bed sheeting. Dollfus & Muller has its exclusive print open mesh belt designed for the production of fine fabrics, scarves, flags; these belts have special non marking surfaces which can avoid as well the particles on the back side.
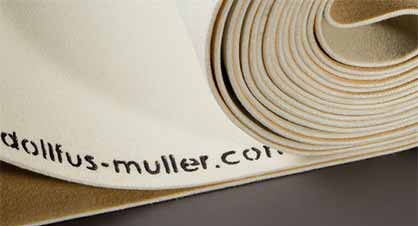
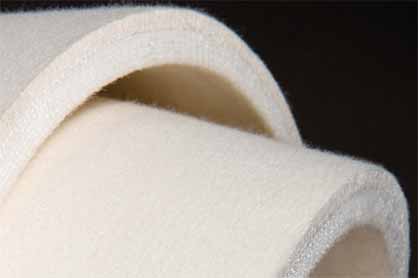
SPOOLEX Group Hall 1 Stand B 209
SPOOLEX group features different brands:
CALEMARD is the converting machinery division. It has focused its activities on highly technical cutting applications. Always based on modular design each equipment is multi-purposes and can convert thick or thin materials into pads or spools of wide or narrow strips. The expertise has allowed to develop and equip machines with sensitive web tension control and guiding systems, to manage high, low and even extremely low tension on the same machine. The result is compact rolls with consistent tension, clean and straight edges for easy use on the downstream product manufacturing process.
DECOUP+ is the specialist in ultrasonic cutting and welding. The technology performs clean and soft edges, without fraying, over thickness, burning or yellowing, but also strong and regular weldings without any additional material. Ultrasonic can be used on any synthetic fabrics. Quick and aesthetic, this technology allows a direct use of the final product. Decoup+ offers compact and ergonomic devices used at any step of the production process: from looms, to final make-up operations.
ROLL CONCEPT is the industrial rollers division. It designs and manufactures industrial rollers, cylinders and winding cores. Specially engineered to improve process performance and increase line speed on web handling and converting industry, their lightweight precision rollers and winding cores ensure the users easy installation, easy handling and durability.
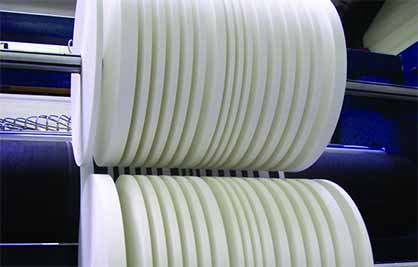
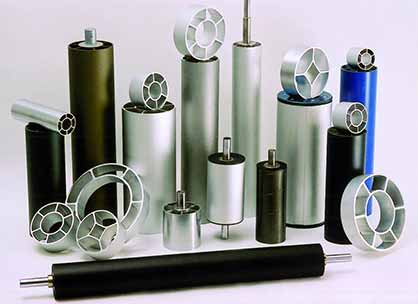
SCHAEFFER Productique Hall 8.1 Stand A 104
In the era of industry 4.0, intensive dematerialization, digital tools are an essential asset to meet new market expectations: traceability, sustainability and flexibility.
SCHAEFFER Productique will present exclusively at ITMA a new business process management tool. Dedicated to textile companies, it will bring more efficiency and flexibility: cloud integration, artificial intelligence, self-adaptive, user-oriented.
A true 4.0 economy management system, it communicates with the standardized platform for digital services and traceability EcolTex® (eBIZ 4.0 - European approval).
ITMA is an opportunity to show the power of this tool designed with the most advanced technologies. It is accessible to large groups as well as small and medium-sized textile companies. This will allow them to better satisfy their market while minimizing the required resources, thus combining performance, ecological footprint and inter-business networking, CSR management and a first step into the world of circular economy.