ITMA 2019
iNTERSPARE presents the latest Krantz Syncro at ITMA
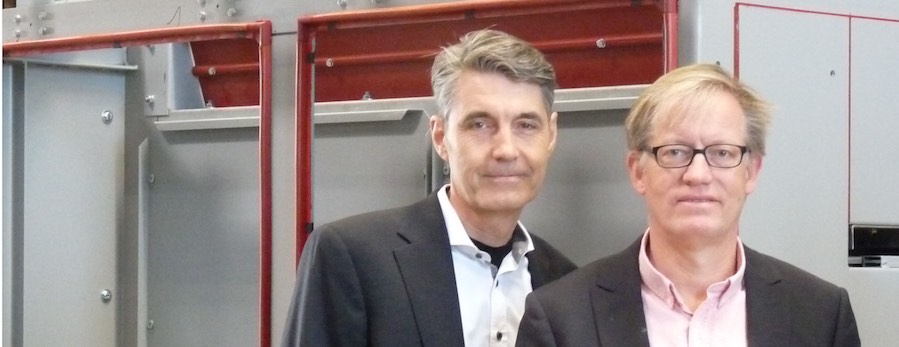
“The requirements in the finishing on premium quality textiles and knitted fabrics are becoming more and more exacting,” says Dirk Polchow, Managing Partner at iNTERSPARE. “Our client’s buyers have very high expectations and we are very happy that we are able to support them still further with our innovations. This means that our clients are capable of fulfilling the requirements far better than their competition. We are looking forward to demonstrating our technical merits, for example the Syncro shrink dryer. With the new Syncro we have further extended our lead in the field!”
KRANTZ SYNCRO
At ITMA, iNTERSPARE will exhibit the Krantz Syncro with an overstretching zone, thereby demonstrating how even the most challenging requirements on modern finishing can be fulfilled on all levels by a superior machine design and the use of the latest technologies. This applies both to the absolute premium quality of the finished goods in connection with the high price-performance ratio and also the current crucial requirements in regard to sustainability, connectivity, and data exchange. Like its predecessor Haas Aerovar, the Krantz Syncro especially reveals its performance capability in the drying of warp knits, as tubular knitted fabrics or cut open, as well as both light and heavy items. However, more and more outstanding results are achieved also in the drying of woven goods. The Syncro has an overstretching zone which allows the fabric to be returned to its basic structure. This means that the elongation of the stitches is reduced in order to achieve the best possible residual shrinkage values. Thanks to the diversity of the Syncro, a smooth operation is possible with multiple narrow or wide material webs (single webs or multiple webs). Furthermore, multiple processes such as drying, shrinking, intermediate drying and effect drying can be carried out here on just one piece of equipment.
The shrink dryer allows long dwell times and high phase leads of up to 200% on the conveyor belt. The result is a even and gentle drying process with optimal release of tension in the material. In addition the ventilation intensity and therefore the material dynamic can be steplessly adjusted. By selecting these many different parameters, the drying can be precisely optimised for the particular requirements of the materials.
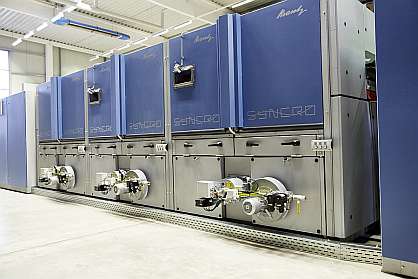
SMART FINISHING - BLUE TECHNOLOGY
The trade fair motto “Smart Finishing - Blue Technology” is directly aimed at the many constructive advantages of the finishing machines from the Krantz and Artos product lines and the example of the Krantz Syncro demonstrates this particularly well. With the Syncro, Smart Finishing is achieved in many ways. Firstly it delivers the highest premium material quality with a particularly soft feel, which is achieved through controlled shrinking and volume development. In addition, the product is also optimised by numerous smart components. In this way, high productivity is achieved with maximum flexibility and profitability.
The Syncro is equipped with the latest measurement and control systems from the Siemens firm, which open up wide-ranging possibilities for use in Industry 4.0 environments.
The Syncro is also smart in terms of maintenance. In this regard iNTERSPARE has enhanced the Syncro in a number of ways. iNTERSPARE is presenting another innovation at ITMA with a fully-automated filter belt cleaning system. An automated filter belt replaces the filter insert here. This eliminates the need for cleaning by employees and the revolving filter belt is automatically cleaned by a traversing vacuum nozzle.
In terms of energy efficiency, the Syncro has likewise already set a real milestone, as sustainability is considered as early as during the construction phase. The patented Econ-Air airflow system makes optimal use of the used heat energy. A true “blue competence” process. Furthermore, it is of course equipped with components, drive units and engines from the latest product generations by Lenze or Siemens, which likewise represent the best possible solution for energy efficiency.
MODERNISATION OFFENSIVE “READY-4-FUTURE”
In the coming years, big changes are coming to the textile industry. Industry 4.0 and IoT are comprehensive concepts for connecting up machines and processes along the textile value chain. These changes will also affect textile finishing and with READY-4-FUTURE, iNTERSPARE has developed a comprehensive concept for their customers in order to optimally prepare them for the coming changes.
More than 15,000 pieces of equipment for textile finishing from the Artos, Babcock (BTM) and Krantz product lines were installed in the last 50 years by Krantz, Deutsche Babcock Textilmaschinen and Moenus. Most of these machines are still used for textile applications and this unusual longevity certainly underlines their sustainability. With the READY-4-FUTURE modernisation campaign, iNTERSPARE is offering its customers the opportunity to continue operating these machines for many more years, by adapting them to the increasing demands using various retrofitting and modernisation modules from the assembly kits. READY-4-FUTURE ensures an evolutionary start to the fourth industrial revolution, contributes to a world that is becoming more sustainable and furthermore also improves profitability by increasing productivity, flexibility and quality. Precisely coordinated modernisation packages with customisable, individual out-of-the-box modules make all retrofitting and modernisation works cost-effective, calculable and quick to implement. The iNTERSPARE experts will happily demonstrate at ITMA how all READY-4-FUTURE packages will recoup costs in just a few years.
In terms of sustainability, for example, retrofitting improves energy efficiency, which not only saves on costs but also improves the life cycle assessment – very important for textile producers’ sustainability strategies and for the fulfillment of the growing demands set by brands and trading firms. The latest generation of control and operation elements in connection with expanded software ensure that all the relevant parameters of the machines are made available in the network, not only the operators but also the data processing and analysis system.
Dirk Polchow has this to say on the subject: “We consider the length of time that our Artos, Babcock and Krantz equipment can be used in production processes to be a true sign of quality. So that this continues, we have developed our READY-4-FUTURE packages. Using these, we can often implement 40 years of technical advancement in less than 4 weeks and optimally support our customers in fulfilling the requirements of the future.”
SMART ORDER SYSTEM APP
Predictive maintenance is certainly the top solution of the future for a smooth operation of machines and one of the biggest advantages of the upcoming Industry 4.0 connection. However, a comprehensive implementation will take many more years, and the delivery and exchange of replacement parts should also function quickly and smoothly until then.
With the SMART ORDER SYSTEM app, iNTERSPARE will be offering a particularly smart and efficient solution in the future. Once registered, iNTERSPARE customers can simply use the app to take a photo of the wearing part or the damage and send it to iNTERSPARE. The app is intended to make life easier for customers and provides a platform for the rapid identification of all replacement parts right there on the machine.
NEW EMPLOYEES
The growth is also being reflected in the employee numbers. iNTERSPARE began as a two-man start-up business and today it has over 70 employees in administration and production. In the last 5 years alone, twenty new jobs were created and the need has still not been met. Currently, iNTERSPARE is looking to recruit more employees in various departments, including a spare parts sales manager for the Central and Middle East region and a commissioning engineer. For both positions, professional and industry experience in machine construction is required. The sales team and production team as a whole are set to be expanded.
NEW COOPERATION FOR CHINA
China is the largest textile producer in the world and is also a particularly important market for iNTERSPARE alongside Bangladesh and India. In order to be in an even better position to address and support textile companies in this very large market, iNTERSPARE is entering into a collaboration with the Chinese firm Shaoxing Hengyuan.
Alongside the Krantz tensioning frames which continue to be produced in Germany, iNTERSPARE is developing a parallel production facility in China together with their partners. In the future Krantz tensioning frames will be produced solely for the Chinese market under the name Krantz Hengyuan.
The staff at iNTERSPARE would welcome your visit to hall 1, stand A131.
For appointment and interview requests, the iNTERSPARE team would be pleased to hear from you. Contact: itma@interspare.com