ITMA 2015
iNTERSPARE is very pleased with its ITMA participation
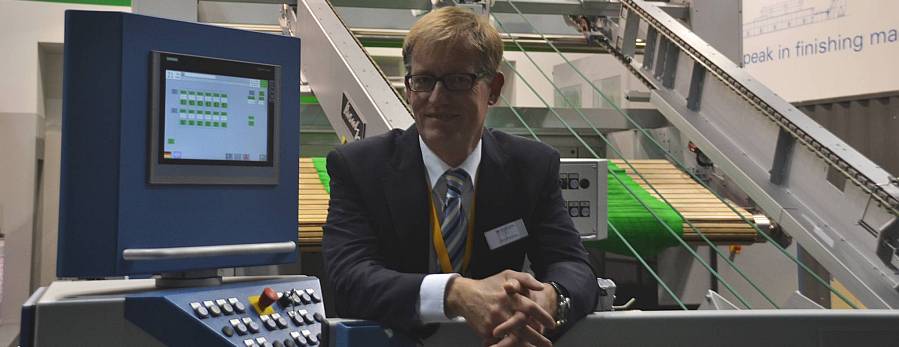
„The ITMA and above all the feedback on our stand and our presentation as a textile finishing machine manufacturer was simply overwhelming“, says iNTERSPARE director Dirk Polchow. „For us it was really an enormous recognition of our work just to see so many happy faces. All visitors to our stand were full of praise on how we tie in with the tradition of Artos and Krantz and can offer these high-quality machines in quantities again. And they were also surprised at how we have now established ourselves as a machinery manufacturer“, he added.
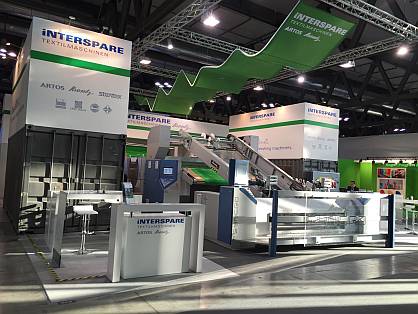
Pic: iNTERSPARE booth on the ITMA 2015 in Milan
iNTERSPARE had used the ITMA, as the showcasing platform of the textile machinery industry, to present the latest version of the legendary Krantz Syncro. The shrink dryer - as a further development of the Haas Aerovar shrink dryer – has always been an excellent example for German engineering creations. In particular, the extraordinary quality of the results and the high production rate, based on the optimal interplay of many sophisticated and patented components, cause the Syncro is considered by experts as the best shrink dryer in the world.
The exhibited advanced next-generation iNTERSPARE Krantz Syncro was adapted to current market trends and customer requirements by iNTERSPARE. An example are next-generation circuits and control units which improve operation even further. Another is the newly developed lifting doors which significantly facilitate the cleaning of the machine, thus reducing maintenance costs and which are available as an option for the Syncro. Further modifications address the increased demands for sustainability and energy efficiency. Here, iNTERSPARE has expanded the Syncro with numerous particularly energy-efficient next-generation components. A particular mention should be made to the state-of-the art motors in EU energy efficiency class IE3 (Premium) and also next-generation control cabinets which are not yet available on the open market.
The Syncro’ s unbeatable performance can be admired especially during the drying of knitted fabrics in tubular or open width form up to all fabric weights. Also in drying of woven fabrics outstanding results will be achieved. The diversity of the Syncro is unique. Without problems it is possible to drive with one or more slim or wide fabric layers side by side. Additionally processes such as drying, shrinking, intermediate drying or drying for formation of fabric can be proceeded here on only one production line.
The shrink dryer allows long reaction times and high overfeeds up to 200 % on the screen belt. This causes a slowly and gentle drying with an optimal stress relieving in the fabric. The drying can be regulated exactly for each special requirement of the fabric because of different selection possibilities of many parameters.
“The many advantages of Syncro are of course well-known all over the world and are even acknowledged by our competitors “, says Dirk Polchow in reference to the quality of the machine. “Therefore the interest of the visitor is often focussed on questions relating to availability, delivery times, to our production and also to the price. From the supply of spare parts our customers know that we do not make any compromises regarding quality and for our machines it is exactly the same. What's important to us is that our customers believe in us and know that we are already well established as a textile finishing machine manufacturer and that we wish to further develop ourselves as well as our machinery portfolio. And I think we were able to underline this impressively at the ITMA.“
Announcement of new construction project at the ITMA press conference
The interest in iNTERSPARE and the iNTERSPARE Krantz Syncro that was exhibited was also very intense at the first ever press conference to be carried out. Around twenty journalists from key media in the global textile industry attended the conference and wanted to know how the company had developed from a successful supplier of spare parts to an established manufacturer of textile finishing machines in recent years and how the vision for the future looks. In response to this, director Polchow announced among other things the new construction of an assembly hall at the iNTERSPARE premises in Reinbek (Germany) which should be completed in summer 2016 and in which the machines shall be manufactured in the future as the available space no longer suffices.
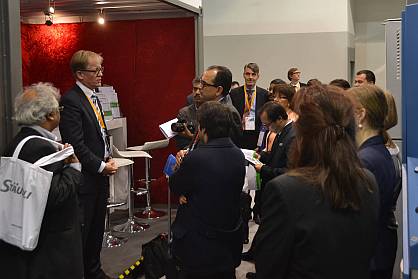
Pic: Managing Director Dirk Polchow during the press conference with about 20 journalists from the trade press
Current machinery range
The current machinery range of iNTERSPARE Textilmaschinen includes the Krantz Syncro shrink dryer and the Krantz K30 stenter, both belonging to the Krantz product line. In the Artos product line, iNTERSPARE Textilmaschinen offers the Artos Unistar stenter, the Artos Vari-Flex dyeing padder and the Artos Uni-Flex impregnation padder.
Extensions, modernisations and upgradings of existing installations
Another topic which took up a large part of discussions at the IMTA stand was the modification, upgrade and modernisation of existing installations of the product lines Artos und Krantz. There is a 5-digit number of existing systems from the Artos, Babcock Krantz, Stentex, Hacoba, Müller und Famatex product lines at textile companies in 116 countries. A lot of these systems, installed by Artos, Krantz, Deutsche Babcock Textilmaschinen and Moenus over the past 50 years, are still used for drying and finishing textiles. Based on a growing need for productivity as well as sustainability, modifications and upgrades offer textile companies an excellent alternative to jumping to the current state of the art with manageable investments.
iNTERSPARE has already carried out upgrades successfully in recent years, for example a tenter frame in the iNTERSPARE product line Artos for Dutch textile company Vlisco Group.
A consequence of a modification may be for example improved energy efficiency. Not only is greater economy attained but also an improved ecological performance - very important for sustainability strategies by textile producers and the satisfaction of the demands of larger brands and retailers. Other modifications include for example the extension of the machine for enlarging production capacity. Alternatively, supplementary component sets increase flexibility and economic efficiency.
Equally interesting are conversions enabling installations to be adjusted to changed specifications. Examples of these are conversions of heaters from oil circulation systems to gas heating or exchanging lubricated tension chains for modern lubrication-free chain systems. More extensive alterations such as the conversion of stenter frames for woven goods for the use of knitted fabrics are also possible.
Updating can also prove economically advisable. This can be achieved by converting from S5 to S7 controls or replacing a PIV transmission with individual drives.
INTERSPARE has all the technical drawings of the machines available and is subsequently able to submit constructive and well-informed proposals.
Smart Order System: an app for ordering spare parts
The visitors to the stand also took pleasure in the new version of the „Smart Order System“ smartphone app and were impressed by how easy it is to use. The iNTERSPARE app liberates customers from all research for the correct spare part allowing the customer to save time and money. The only thing the customer has to do is to install the app and to send a picture of the part which needs to be replaced. Shortly after the customer gets any Information and an offer by iNTERSPARE.