ITM 2022
Baldwin’s sustainable TexCoat G4 finishing system to be showcased at ITM and Techtextil
Non-contact precision-spray system supports textile finishers managing high energy and chemical costs
With a cost-sensitive global economy and an increased focus by brands and consumers on the environment, customers are placing a premium on sustainability in textile production. TexCoat G4’s non-contact spray technology offers numerous advantages compared to conventional methods of applying finishing chemistry. With Baldwin’s innovative system, the chemistry is precisely distributed across the textile surface and is applied only where it is required, on one or both sides of the fabric. The non-contact technology eliminates chemistry dilution in wet-on-wet processes, allowing full control of maintaining consistent chemistry coverage rates. Plus, pad bath contamination is eliminated, and changeovers are only required when there is a change of finish chemistry.
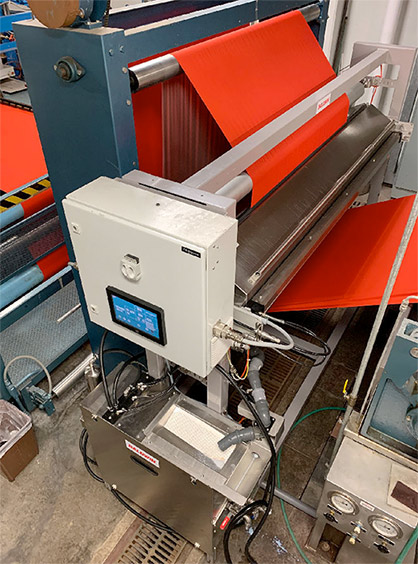
More specifically, with Baldwin’s TexCoat G4, textile finishers can expect unprecedented tracking and control of the finishing process for consistent quality. Changeovers are easily and quickly performed, thanks to recipe management, including automated chemistry and coverage selection. Furthermore, the system offers automated speed tracking, fabric-width compensation, and real-time monitoring to track system uptime, performance and chemistry usage, as well as active care alerts.
In addition, the TexCoat G4 system can process a wide range of low-viscosity water-based chemicals, such as durable water repellents, softeners, anti-microbials, flame retardants and more. Baldwin’s innovative technology utilizes the same chemicals used in the traditional pad bath, and no special auxiliaries are required. The recipe is adjusted by increasing the concentration and reducing the pickup by a corresponding amount, so that the same level of solids is applied. Some applications, such as durable water repellents, are only applied on the face of the fabric, instead of the traditional method of saturation through dipping and squeezing. Drier fabric entering the stenter means lower drying temperatures and faster process speeds. Single-side applications also open up the opportunity to process back-coated or laminated fabrics in a single pass of the stenter, instead of two passes.
“We are looking forward to very busy exhibitions, especially with sustainability challenges being such a high priority for fabric producers and brands,” said Rick Stanford, Baldwin’s Vice President of Global Business Development, Textiles. “Energy and chemical costs are skyrocketing, and our TexCoat G4 is the ultimate tool to assist manufacturers in managing these costs in the finishing department.”