Dyeing, Drying, Finishing
Van Clewe converts Brückner POWER-FRAME ECO stenter to cogeneration with micro gas turbine
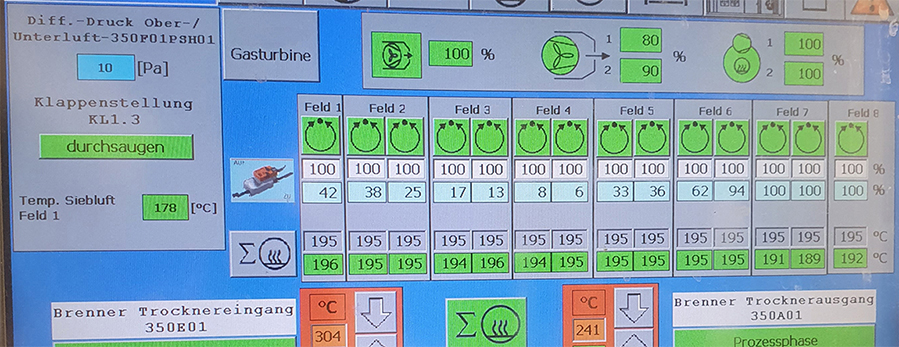
Founded in 1954 and family-run in the third generation, the contract manufacturer Van Clewe supplies customers throughout Europe and the world. The company produces 100% of its products at its site in Dingden (North Rhine-Westphalia, Germany). Sustainable management is a major concern at Van Clewe and has been a lived theme for decades.
Electricity and gas are the main drivers in production. Van Clewe is constantly working on measures to avoid unnecessary consumption of these valuable resources. For the past 12 years, Van Clewe has been operating a combined heat and power gas engine. The main advantage of this technology is that the electricity generation works simultaneously with the electricity demand of the production. An additional PV system ensures that the company can operate without externally supplied electricity during the day, weather permitting. This is an important factor for a textile finishing plant when the heat requirement for dry and wet processes is covered by combined heat and power plants.
Brückner, a mechanical engineering company and system supplier with over 70 years of experience in the textile finishing sector, has always focused on being particularly innovative and economical in all areas. On this way everything is questioned and again and again one dares to go new ways to increase the energy efficiency of the machines. Already in 2014 - 2015, the advantages of cogeneration in textile dryers were explained and discussed at a symposium at Brückner. In the meantime, the energy issue has taken on an unprecedented explosiveness and the idea of cogeneration is becoming more and more interesting due to rising energy prices and impending bottlenecks. Cogeneration always makes sense when heating with fuels instead of electricity and is a must for self-generation based on microturbines to be efficient.
Van Clewe already had a Brückner belt dryer with vertical chain of the type POWER-FRAME ECO and in memory of the presentation in 2015 at Brückner, Van Clewe and Brückner closely cooperated to integrate a micro gas turbine in industrial scale and to integrate it into the processes based on the experiences at that time in the pilot plant at Brückner with this technology and with courage to take risks by Van Clewe.
The special feature of the innovative ECO technology of the Brückner stenter consists of the combination of through-suction drying and subsequent air impingement. At the same time, the exhaust air heat is optimally utilized by flowing hot circulating air through the cold and usually wet fabric entering the dryer. In addition, the energy potential of the exhaust air is even better utilized by integrated heat-recovery systems. The preheated fresh air is fed to a central gas-fired combustion chamber and metered to the individual thermal chambers as process air. The central combustion chamber also allows direct integration of a combined heat and power unit / micro gas turbine. The hot turbine exhaust air is used directly for the process and the electricity generated covers the power requirements of the stenter.
Due to its design, the Brückner POWER-FRAME ECO is particularly well suited for the integration of a micro gas turbine. However, integration is also possible with other Brückner stenter types. The hot exhaust gas of the microturbine must then be distributed into several compartments, comparable to the integration of an air-to-air heat-recovery system.
At Van Clewe, additional gas is burned using the gas turbine, but on the other hand the gas consumption at the stenter itself is very much reduced, so that no more gas is consumed overall. The big advantage is that electricity is also generated. The micro gas turbine at Van Clewe has an output of 200 Kwh of electricity generation, which is more than the stenter itself consumes in operation. This creates independence from the electricity supplier and electricity does not have to be purchased at expensive conditions.
A micro gas turbine can - if the company itself generates electricity by wind power or like Van Clewe by solar energy - be used as redundancy in case of wind failure or at night. A cogeneration unit (turbine or engine) can also be powered by biogas, which is locally available or can be procured in the form of bio-LNG. Future considerations involving hydrogen may take the microturbine to a completely CO2-free level, provided the hydrogen is "green" produced. But it will certainly take some time before hydrogen is commercially available.
Van Clewe is very satisfied with the performance and the conversion of the Brückner POWER-FRAME ECO. Ansgar van Clewe, Managing Director: "The turbine runs at 100% power almost without exception. The operating personnel has no additional work with the turbine and the control is very simple. In drying processes, the front burner is switched off and the process-relevant parameters are controlled with the rear compartments. If a higher drying capacity is required, we switch on the front burner. Then the gas turbine still runs at 100 % power."
Axel Pieper, CTO of Brückner says: "We are proud to have taken an important innovative step years ago, which today, with the discussion on energy efficiency and green hydrogen, opens up a further opportunity to save energy and thus contribute to avoiding CO2 emissions and counteracting climate change."