Dyeing, Drying, Finishing
Grupo Kaltex benefits from Monforts upgrades
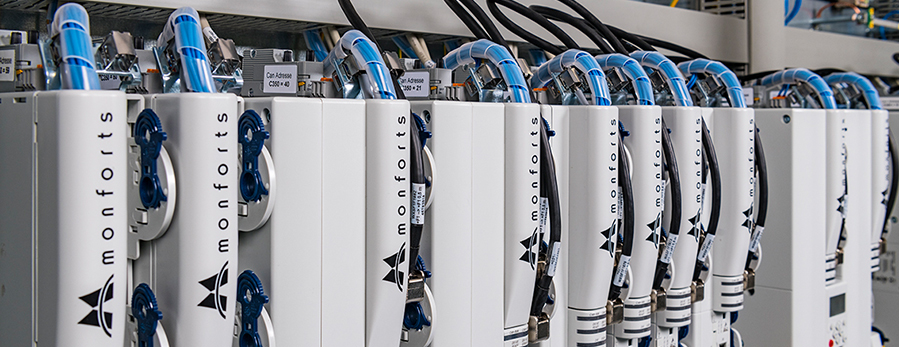
Textile companies making major capital investments in new manufacturing lines rely on durability from the company’s production ranges, and it’s for this reason that there are currently an estimated 2,000 Monforts machines in operation worldwide – some of which were first installed over 30 years ago.
This doesn’t mean, however, that they can’t benefit from many of the advances in performance and automation that have subsequently been made by Monforts.
Impact
“Our machines are known for their robustness and long service life, but the retrofitting of specific modules with new control and drive technology – going far beyond the basic replacement of spare parts – can have a significant impact on the performance of an existing line,” says Monforts marketing manager Nicole Croonenbroek. “If you’re attending the ITMA exhibition in June this year, please come and visit us in Hall 18, stand B106, where we’ll be happy to discuss the range of modifications and modernisations that can be made to improve existing lines at any time.”
A good example of what can be achieved is the major modification project Monforts has recently undertaken for Grupo Kaltex, in Mexico City, Mexico, on a Montex stenter that was first commissioned back in 1995.
Grupo Kaltex is a fully vertically integrated textile organisation with divisions manufacturing synthetic fibres, yarns and fabrics. It also has garment and home textiles divisions exporting internationally.
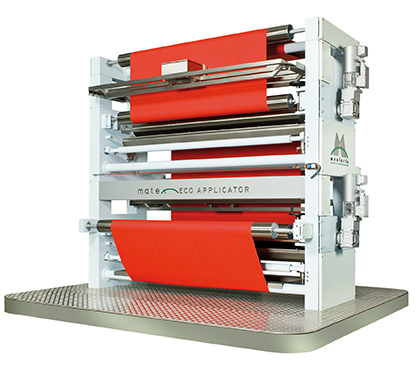
The recent modifications carried out by Monforts at the Kaltex finishing plant consisted of the exchange of the complete switch cabinet – pre-assembled and tested in Germany – and the replacement of all control panels to the latest technical specifications, with new frequency converters, transport drives and a gearbox, along with modifications of the circulation fans. In addition, the Montex stenter has been equipped with full PLC control, 24-inch touchscreen PC control and the very latest Monforts visualisation software.
Energy optimisation
“The machine is now running perfectly on the electrical side and unplanned stops have been completely eliminated,” reports Alejandro Matus, administrative manager of finishing at Kaltex. “In addition, we are achieving significant energy savings.”
Monforts is increasingly being called upon to advise its existing customers on new options for energy optimisation such as the Monforts universal Energy Tower– a flexible, free-standing air/air heat exchanger for recovering the heat from the exhaust air flow of thermal processes. This can result in a 30% reduction in the energy consumed by a line, depending on the exhaust air volume and operating temperature.
A Monforts Eco Booster, completely integrated into the chamber design of the Montex stenter, is another retrofitting option. As a single state-of-the-art heat recovery system with automatic cleaning, it can be added to existing ranges. For ranges of up to eight chambers only one module is necessary to achieve significant energy savings.
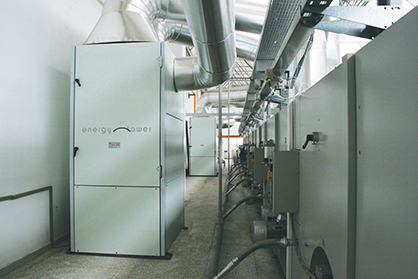
In addition, the Eco Booster consumes only minimal amounts of water during the cleaning cycle and the entire process is controlled and monitored automatically.
The Matex Eco Applicator is an alternative to the conventional padding process for energy-conscious finishing and achieving considerable savings in the drying of treated fabrics. The precise amount of chemical can be applied to the fabric so that less drying capacity is required in the stenter.
“Compared to a new machine, upgrades are a low-cost investment that deliver clearly defined benefits,” Nicole Croonenbroek concludes. “With almost 140 years of experience, Monforts is the right partner to assist valued customers in offering retrofits to help with enhanced production, sustainable operation and energy savings. All the above measures can also be applied to second-hand Monforts machinery.”
Further details of the Monforts retrofitting programme can be accessed at:
www.monforts.de/en/spare-parts-modifications/