Composites
DORNIER presents new developments of its machines and systems for composite series production at JEC World 2024
In addition to established applications in the aerospace industry, fibre composite solutions are also playing an increasingly important role in sectors such as construction, energy and automotive. DORNIER has developed the production system PROTOS® (Polymer and Roving to Sheet) to enable companies to economically manufacture fibre composite structures suitable for large-scale production. PROTOS® systems can be used to produce thermoplastic fibre composite components based on unidirectional continuous fibre reinforcements (UD tapes) and organic sheets with very good drapability in high quality.
This is also interesting for companies in the automotive industry. "We want to enable automotive suppliers to produce customised and series-produced fibre composite components on an internationally competitive basis – with the desired geometry, the right mix of fibres and matrix as well as optimal mechanical properties," explains Klingele. In addition to the technology centre at Lake Constance, a tape weaving machine has therefore recently been made available for test runs at the US subsidiary of Lindauer DORNIER for interested parties – also from other industries. It can be used to process binder-fixed, fully impregnated tapes and other tape-shaped materials into semi-finished textile products. "In terms of flexibility and costs, it makes a big difference whether you buy finished sheets and then thermoform them or whether you produce them yourself with PROTOS® exactly as required," confirms Oliver Meier, VP of American DORNIER Corporation. With this new offering, we are acknowledging the great importance of the American market and invite our customers and OEMs to visit us in Charlotte, N.C. to discover this powerful technology for themselves," he adds.
Series production of lightweight components on DORNIER systems
With the production system TRITOS® (Textile Roving into Three-dimensionally Oriented Structure), DORNIER proves that complex 3D fabrics with very good damage tolerance and high dynamic load-bearing capacity can also be reliably manufactured in industrial production areas with high cost pressure. Highly specialised suppliers use TRITOS® systems to produce 3D fabrics with thicknesses of up to 100 mm for high-performance applications. "Economical series production of high-quality, customised composites is becoming increasingly important in many industrial branches," says Josef Klingele, Head of the Composite Systems product line at DORNIER.
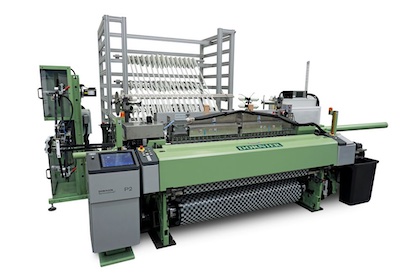
News on the P2 rapier weaving machine
Variants of the DORNIER P2 rapier weaving machine which were specially developed for composites will also play a role at JEC World 2024. On the P2 Roving, the global benchmark for production systems for high-quality fabrics made of carbon, glass and aramid fibres, it is possible to produce technical reinforcing fabrics for high-end applications extremely economically thanks to its high insertion capacity and its patented and maintenance-free DORNIER SyncroDrive®. With the new integrated electronically controlled ECW+ cloth winder, high winding qualities can be achieved on a reproducible basis.
The P2 Mono Roving guarantees reliable production from heavy tow to speciality fabrics made from the finest ceramic threads. In combination with the DORNIER Zero Twist Feeder and special Zero Twist technologies for weft insertion, the P2 Mono Roving ZT allows the twist-free insertion of two weft colours at high speed and with a wide variety of patterns. Thanks to its innovative modular design, fibre composite manufacturers can use the P2 Mono Roving ZT to flexibly process a wide range of tape-shaped materials.