Weaving
Toyota Industries has begun production of new JAT810 Air Jet Loom
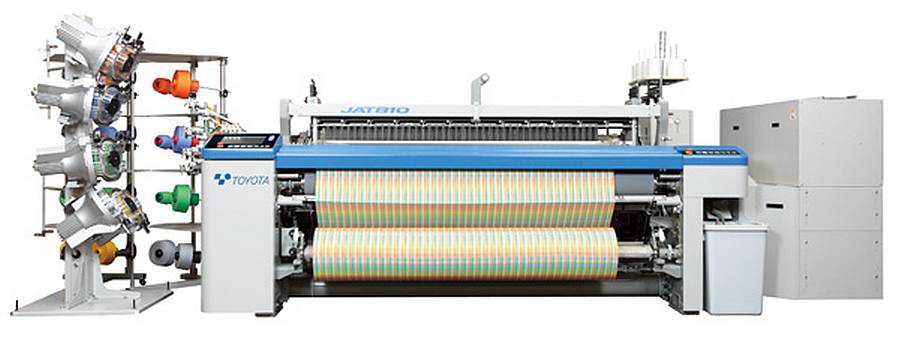
The JAT810 has been comprehensively designed for greater energy savings, higher productivity and improved ease of use.
As electricity and labor costs are rising in emerging nations such as China and India, which constitute the main markets for air jet looms, demand for products with greater energy savings and increased productivity is expanding.
In order to meet these market needs, TICO has adopted a new weft insertion system which has produced a 20% reduction* in air consumption compared to the previous model. The weave assist system, the “New WAS,” incorporating expertise gained by TICO over many years, and a factory management system, “FACT,” that enables centralized management of the entire factory, also contribute to increased productivity. In addition, TICO has developed its own original electronic shedding device, the “E-shed,” which provides high speed weaving as well as versatility.
As a corporation supporting the clothing aspect of people's need for food, clothing and shelter, in the nearly 90 years since completing the first Toyoda Automatic Loom, Type G, TICO has been continually striving to develop looms that produce high quality textiles at a low cost, based on the concept of Jidoka (Automation with a human touch).
With the JAT810, TICO is continuing its contributions to development of the global textile industry, responding to customers' demands quickly and with meticulous attention to detail, through the industry's leading service network extending around the world.
Main Features
20% reduction* in air consumption compared to the previous model, through an innovative weft insertion system
1) New sub-nozzle
Weft insertion with less air usage is achieved by the optimization of the air stream angle and TICO's original nozzle aperture configuration.
2) TICO's original reed, “JAT e-REED”
The optimized shape of the reed's tunnel allows the sub-nozzle to be located closer to the reed, thereby preventing the air stream from scattering, which enables air consumption for the weft insertion to be reduced.
Increased productivity through factory management
1) Weave assist system “New WAS”
The “New WAS" system, which incorporates TICO's many years of weaving know-how in digital form, automatically makes optimal settings, enabling the machine to perform the role of a skilled worker.
- Optimal weaving conditions and settings are automatically determined by the “New WAS” simply by selecting the basic conditions (type of yarn, density, pattern) corresponding to a wide variety of textiles.
- An adjustment support function has been added which helps reduce defects in quality, and enables the user to make quick adjustments to the machine setting.
2) Factory management system “FACT”
The “FACT” system can display a wide range of operational parameters and production information for each machine including air consumption according the actual factory layout, thus achieving enhanced productivity through centralized management of the entire factory.
Development of the TICO original “E-shed" electronic shedding device
The independently-driven shedding technology developed by TICO enables faster weaving of complex fabrics, thus achieving both high-speed and versatility.
Adoption of a new function panel
The large 12-inch panel allows large amounts of information to be displayed on a single screen, and adoption of swipe operation provides easier, more visual operability.
* Results vary depending on machine conditions