Texprocess 2017
Pfaff, Dürkopp Adler, Beisler and KSL will present state-of-the-art industry 4.0 Solutions at Texprocess
This year the topic „Industry 4.0“ will be in the focus of the presentation. On the booth visitors can gain a live impression of the advantages offered by the networking of up to 1,500 sewing machines and the real-time analysis of all machine and production data – and see how simple and user-friendly such a system is structured. Also the replacement of the operator by a robot will become reality within the near future. A study shows how several working places are linked by a robot gripping arm so that sewing is done fully automatically.
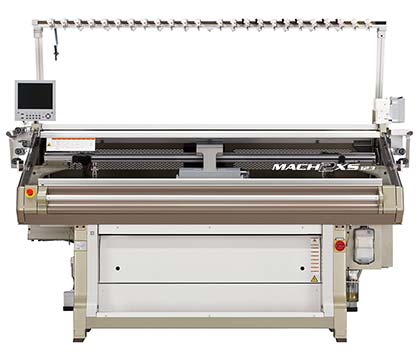
Pic: Premium Generation (c) 2017 PFAFF
At this year's Texprocess DÜRKOPP ADLER AG will demonstrate its strengths with regard to the automation and digitization of industrial sewing technology by the novelties to be shown and underlines its leading position in the world of sewing technology.
The latest PREMIUM generation of the flagship M-TYPE makes it possible to network sewing places, e.g. in the automotive or home upholstery production, and machines can be adapted to different requirements via a central server. Thus, the individualised production in the Industry 4.0 era is as easy as never before. These digitally controlled machines are now available in all types of construction as flat bed, cylinder arm and post bed machines.
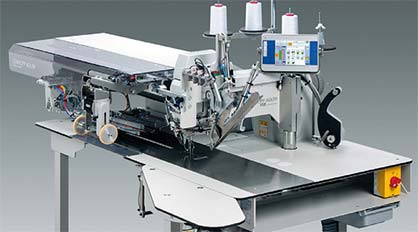
Pic: Da755 S (c) 2017 PFAFF
With the launch of a new generation of automats for piped pockets Dürkopp Adler has realized a milestone in the field of automated clothing production. The new class 755 for right-angular piped welt pocket openings with and without flap makes it possible to reduce the time needed for the conversion to other needle distances by up to 80% and to increase the output PREMIUM generation by up to 28.5%. Maximum seam quality, networkability for Industry 4.0 solutions and even better operability in comparison to the predecessor improve the process quality and make the machine one of the most important components of the classic production of men's garments.
At the Texprocess PFAFF INDUSTRIAL will show flexible and high-performance sewing and welding solutions to process technical and non-technical textiles and leather. The presentation of the latest jeans solutions that offer the customer a real increase in quality and output will be one of the focal points. Without a doubt, the new PFAFF 3589 is the fastest pocket setter on the market. The PFAFF 3589 ensures consistently high quality and performance – even when using two sewing heads with different colored threads. During an 8-hour operation, up to 2,600 medium-sized jeans pockets may be processed. The PFAFF 3589 yields top sewing results on modern stretch jeans. The new PFAFF 3589 is another milestone in the history of PFAFF pocket setters.
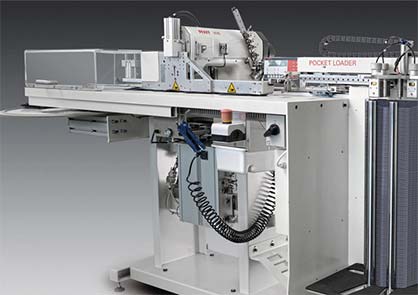
Pic: Pfaff 3538 (c) 2017 PFAFF
The PFAFF 3538 pocket hemmer automat shown at the fair will feature a new fully automated pocket loader. Once the magazine (with up to 500 pocket cuts) has been stocked, the machine works completely without an operator. This way, one operator is able to look after several machines. Using the PFAFF 3538, an output of approx. 16,500 pockets within 8 hours is possible. The automat guarantees a smooth and absolutely straight pocket hem. The machine is equipped with an automatic chain cutting and suction device (= Plus-version).
The special “curved version” of the PFAFF 3819 waistband machine which was specifically designed to process fashionable ladies’ jeans is an absolute world debut. For ladies’ jeans the waistband is usually divided into straight and curved seam sections to achieve a perfect fit that is perfectly molded to the female anatomy. Using the PFAFF 3819, it is for the first time ever possible to program and realize straight and curved seam sections with just one machine. An innovative puller system in combination with intelligent machine software is the core of this innovation. Using a knee switch, the various seam sections (straight and curved) may be called up. The “curved” PFAFF 3538 permits the production of a perfectly curved waistband in ONE operation with just ONE machine.
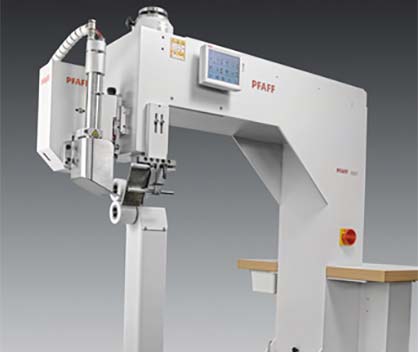
Pic: Pfaff 8321 (c) 2017 PFAFF
For more than 30 years PFAFF INDUSTRIAL has been building class 8362 mobile hot-wedge welding machines. In Frankfurt the company will present the PFAFF 8362i, a completely new generation featuring electrical wedge movement, automatic detection of the end of the weld seam and an intuitive software for many innovative programming functions. The machine is able to create many different seams such as lap welds, hem welds and welted seams. For the first time ever, a long-arm version of the proven PFAFF 8312 ultrasonic welding machine featuring an arm space of 1,000 mm will be shown at the trade show. PFAFF INDUSTRIAL will show the PFAFF 8321, a heavy-duty version (big heavy-duty housing/ height of the postbed 750 mm. arm space 750 mm) of a programmable hot-wedge/hot-air machine to process rubber boats, containers and inflatable objects.
Texprocess 2017 is the perfect platform for KSL (Lorsch) to demonstrate the range of products of automated sewing systems to an international audience with an increasing demand for automation solutions in a growing number of segments.
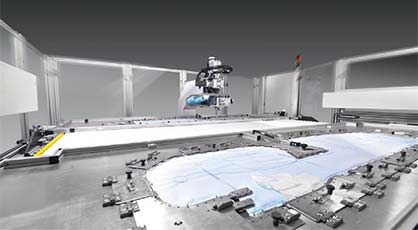
Pic: KSL KL110 (c) 2017 PFAFF
As a trade show highlight PFAFF INDUSTRIAL and KSL will show a joint “robotics” innovation. The system accomplishes a fully automated bobbin change on the PFAFF Plusline 2481 using a handling robot. The required bobbin change is done via a changer magazine with 8 bobbins with the robot autonomously exchanging the entire magazine. Additionally, the robot guides the item to be sewn past the sewing head. Thus operator intervention is greatly reduced. The system combines PFAFF INDUSTRIAL’s sewing competence with KSL’s handling know-how and sets new standards in automated textile production. It shortens production cycles, prevents standstills and significantly increases productivity. This solution is another step towards operator-less production. The KL 110 CNC sewing unit head bag equipped with barcode scanner system to acquire data in multiple applications for direct analysis on the HMI-operator panel will be presented in the airbag segment. This freely programmable CNC sewing unit with turning head is offered in either one or two needle design and sewing speed up to 3,000 stitches per minute. It is used for the servo controlled sewing of high quality safety, functional- and decorative seams. Due to the tangential orientation of the sewing head into any direction, sophisticated PFAFF 8321 KL 110 top-quality seams may be sewn using lockstitch or chainstitch. The integrated template changing system saves a lot of space and allows an overlapping workprocess.
In the tire cord segment KSL will exhibit the KL 624 long-arm feed-off arm sewing system with 10 needles for linear sewing of light-weight belts and tire cord material. In addition, a KL 950 classic multi-needle sewing unit for multi-functional sewing and a material passage width of 1,200 mm will be shown. It is equipped with a height-adjustable top transport system and fournisseurs for consistent thread tension.
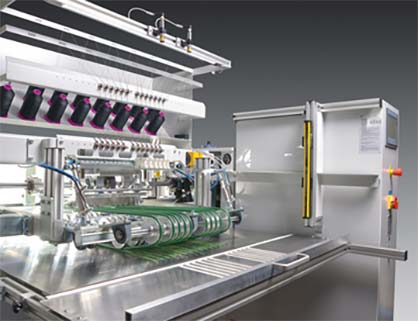
Pic: KSL KL950 (c) 2017 PFAFF