Recycling / Circular Economy
Breaking new ground in Turkey’s textile industry
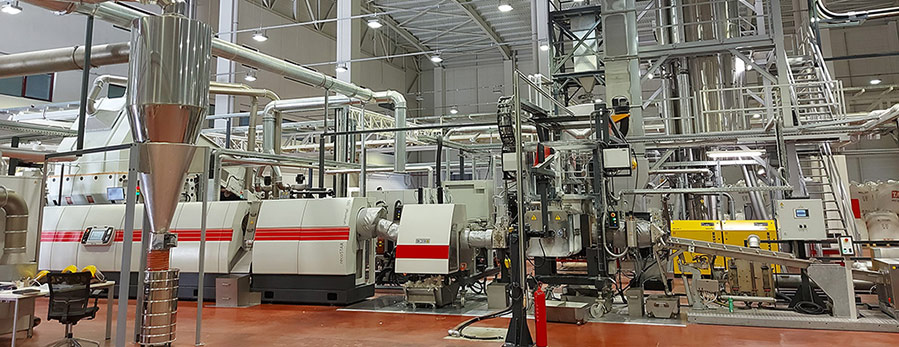
Korteks, one of the world’s biggest yarn producers based in Bursa, Turkey, has started the production of recycled polyester filament yarn in its production facility using a Starlinger recycling line.
Korteks uses the polyester regranulate at a share of 100 % for its new polyester filament yarn line it is going to market under the name “TAÇ Reborn”. With this investment, the company has made an important step towards establishing a circular economy in the Turkish textile industry.
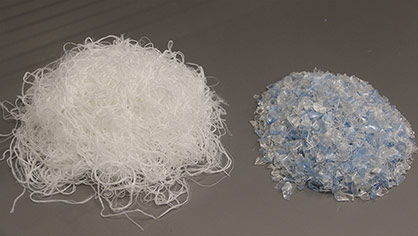
“We have been in extensive cooperation with Starlinger for a long time” said Baris Mert, General Manager of Korteks. “Thanks to their unique and innovative recycling technology we can offer new products in line with the circular economy model. That's why, as Europe's largest integrated and innovative polyester yarn producer, we are very pleased to work with Starlinger, the market leader in PET and polyester recycling and refining.”
Rapid Sleeve Changer: Finest melt filtration for perfect yarn
The Starlinger recycling line is the first of its kind in Turkey and is equipped with special components for filament yarn recycling. A RSC (Rapid Sleeve Changer) candle filter developed by Starlinger ensures finest melt filtration down to 15 micrometer. It has been specially designed for polyester recycling and reaches an output of 1000 kg/h. For continuous operation the filter elements are changed “on the fly” without interrupting production, which significantly limits melt loss.
The viscoSTAR SSP unit at the end of the recycling process guarantees consistent IV increase according to the first-in-first-out principle. This makes sure that the produced regranulate has the ideal properties required for filament yarn production. The technical configuration of the line does not only allow the processing of a polyester fiber/PET flake mix as input materials, but also 100 % polyester filament scrap or 100 % PET bottle flakes.
With the new recycling facility, which comprises a total closed area of 17,000 m² and has a monthly production capacity of 600 tons, Korteks was able to reduce the production waste at its virgin PES yarn site to zero.
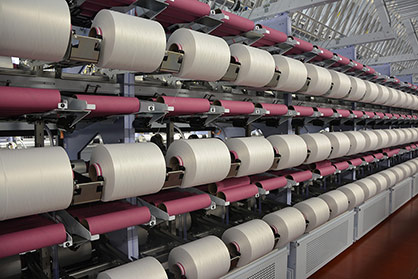
A paradigm shift in synthetic fiber production
“We are proud to be a partner in Korteks’ quest for more sustainability in the textile business”, said Paul Niedl, Commercial Head of Starlinger recycling technology. “Turkey is a significant global player in this industry. If more and more Turkish textile manufacturers start using recycled materials, this will be an important signal for the sector and a big step towards a circular economy. We support this development with our extensive know-how in synthetic fiber recycling and supply the fine-tuned and reliable recycling technology required in this field.”
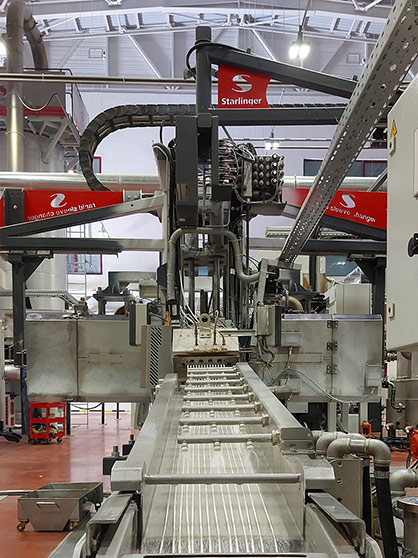
Korteks expects the recycling market in general to grow as there is increased acceptance for recycled products in the society, and predicts the need for recycling solutions also for other synthetic and natural fibers.
“At Korteks, we always aim at sustainable growth that reduces environmental impact and creates value. For this reason, we are gradually expanding our product range in sustainable and smart textiles every day”, said Baris Mert. “The period of the pandemic that the world has been going through has once again strikingly revealed the necessity of building a sustainable living together. The textile industry is also deeply affected by this big transformation on the globe. We believe that those who can manage this change well will also set the global textile agenda in the future. With this belief, we carried out the polyester recycling facility project with an investment of 10 million dollars. Thanks to this project, we broke new ground in Turkey and can produce polyester filament yarn from 100 % PET bottles. Having Starlinger at our side as a business partner gives us strength in our long-term journey towards sustainability.”