Nonwovens / Technical Textiles
Lightweight material for a difficult task
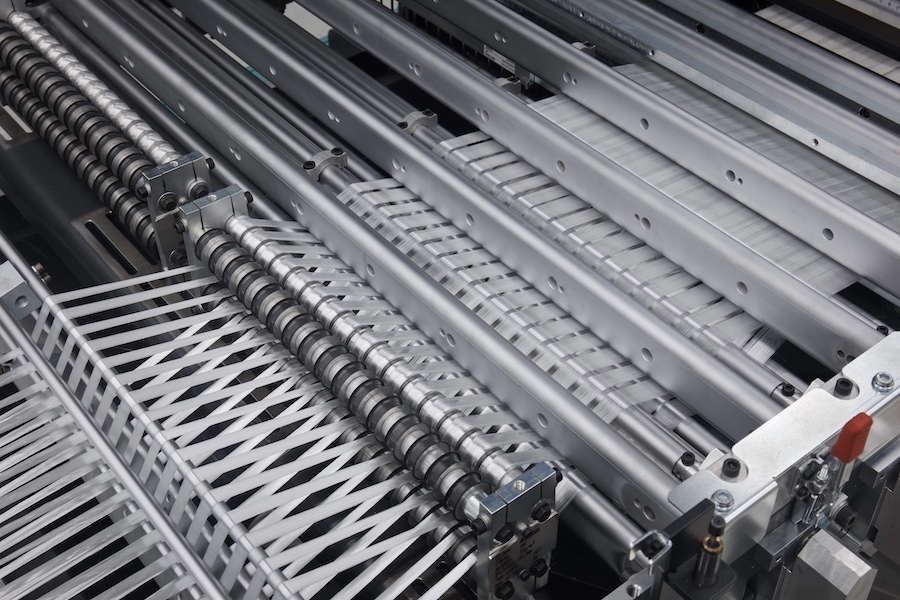
Production of UHMWPE non-crimp structures for personal protective equipment using KARL MAYER composite machines
“We are receiving more and more enquiries from Europe about bulletproof protective waistcoats,” says Dr Jürgen Tröltzsch, Special Specification Project Manager at KARL MAYER's Technical Textiles business unit.
He and his team have already been successfully developing solutions for the production of extremely high-performance yet lightweight multiaxial non-cromp fabrics for textile protective applications for several years. A low weight is important for the wearing comfort of protective equipment. Products made from aramid fibres, a high-strength polyamide, are already established on the market. These fibres are spread into thin tapes using the UD 700 fibre spreading machine, fed to the COP MAX 5 multiaxial warp knitting machine at constant tension in a two-stage process and consolidated into high-quality fabrics by means of stitch-bonding. The process already enabled individual layer weights of just 90 g/m².
The experts at KARL MAYER found that it was still too heavy, as up to 70 layers of tape are combined at different angles depending on the protection class.
In another project, ultra-high molecular weight polyethylene (UHMWPE) fibres were used. Compared to aramid, these fibres have a lower density and a high tensile strength of over 3.5 GPa. Despite their lower material usage and weight, UHMWPE fibres offer the same energy absorption when hit by bullets and other projectiles as aramid /1/.
Production of extremely light fibre layers
The process for manufacturing UHMWPE tapes is similar to that for aramid processing. In a first step, the fibres are spread into single-layer tapes using the capabilities of the UD 700 fibre spreading system. The spreading tests at KARL MAYER were extremely promising. Due to its good spreading behaviour, the UHMWPE fibre can be used in high count and still be spread into extremely thin, lightweight layers.
“We have produced layers with a thickness of just 40 to 50 µm and a maximum of two individual filaments on top of each other. This makes weights per unit area of less than 30 g/m² per layer possible,” says Jürgen Tröltzsch, delighted with the success.
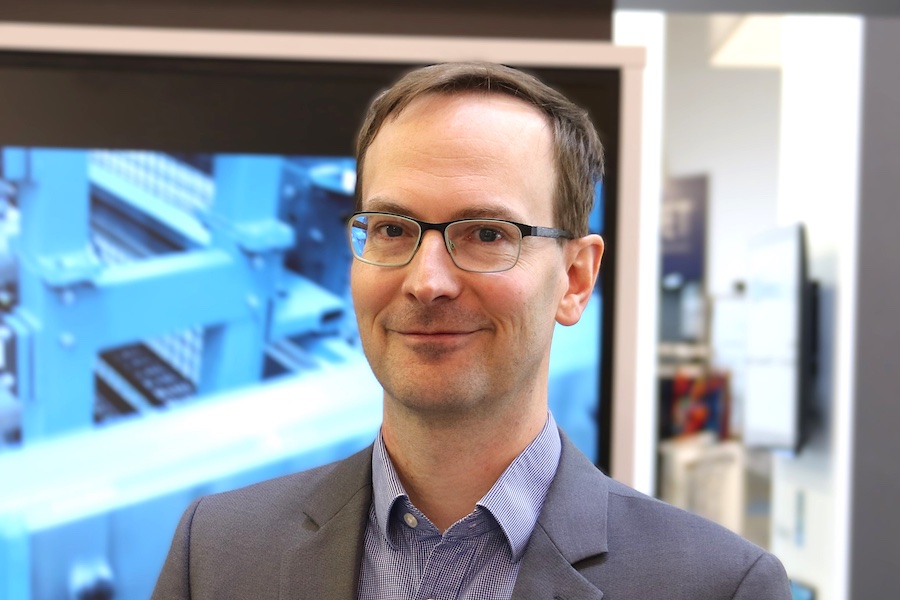
Due to the low weights per unit area, the filaments must be fixed in position directly after the spreading process so that no lanes are created during further processing. Laying lanes are break-in points for the projectile and are therefore an exclusion criterion. A wafer-thin polymer film, 10 µm thick, was laminated onto one side of the unidirectional single-layer tapes made from spread fibers as a fixing material. This allows the strength potential of the fibres to be used to the maximum in order to do justice to the price of the yarns.
A module for film feeding and heating was integrated into fiber spreading machine for the required connection of fibre layer and film. The tests for this also delivered encouraging results.
In a second step, the unidirectional single-layer tapes are joined in 0° and 90° angle layers on the COP MAX 5 to form layer stacks, so-called cross-plies, and bonded using the wrap knitting technique, as has already been tried and tested in aramid processing. Up to six layers can be stacked automatically. In particular, the system for automatic stacking of layers in different angular orientations has already impressed customers who visited KARL MAYER to find out about the possibilities of multiaxial technology for use in the protective equipment sector. In practice, the layer stacks are still often created manually.
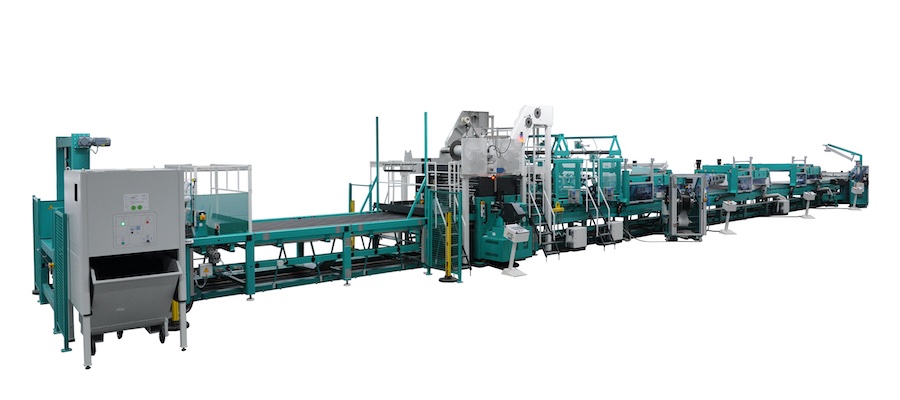
Successful tests
Cross-plies made from UHMWPE fibres were already comprehensively tested in 2021 by the Mellrichstadt State Procurement Office in accordance with the internationally used US NIJ Standard 0101.06. The tape layer package had a total weight of 6,000 g/m² and an angular arrangement of the fibre layers of 0°/90°. The perforation and backface signature test was successfully passed.
The advantages of KARL MAYER fibre spreading technology for the production of protective textile layers at a glance
+ sophisticated fiber spreading technology for highly aligned and homogeneous fiber orientation
+ use of higher yarn counts possible
+ lower material costs per kg
+ creel with less bobbin positions, less space requirement, less yarn loading effort
+ material combination of fibres and film:
+ no liquid chemicals required for embedding the fibres
+ no energy consumption to evaporate water