ITMA 2019
New 3D braiding machine and mixed reality learning environment for the weaving process
Digital retrofitting of a 3D braiding machine for the production of three-dimensionally reinforced ceramic turbine components
Developed from an existing conventional mechanics, a 3D braiding machine was digitized and rebuilt according to industry 4.0 standard. This enables, for example, the prototyping and production of three-dimensionally reinforced ceramic components. As a virtual micro factory, the processing of very sensitive or brittle fibre materials can be simulated in an appropriate software environment. Subsequently, the process data is generated and the production is mapped in the real machine. The process stability is thus almost doubled, the machine speed could be increased by 150 percent. The location-independent simulation and control software (open source) allows extremely flexible process planning and control of the process chain with a mobile terminal - in our application for the production of a textile preform for a ceramic component in turbine construction.
The exhibit demonstrates on the one hand the successful digital retro-fitting of analogous machines and on the other hand the holistic (virtual and real) process design for the processing of sensitive fibre materials, which are used in highly efficient energy conversion as lightweight construction materials.
For further information please contact martin.kolloch@ita.rwth-aachen.de.
Mixed-reality learning environment for weaving process
Training and qualification of new and existing employees are important prerequisites for a company's success, especially for machine and textile manufacturers. The ITA has developed a learning environment based on a 3D model of a tape loom using mixed-reality technology. Mixed reality is the combination of data from reality with artificial 2D or 3D objects (virtual reality).
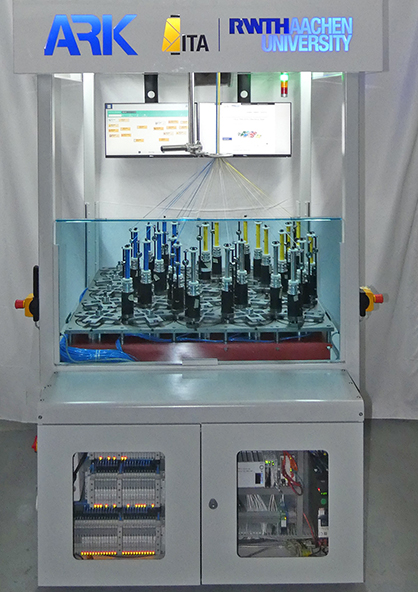
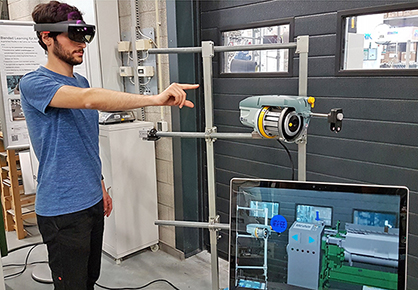
The 3D model of a wide loom is presented to the employee in the room for illustration using mixed-reality technology. Mixed reality glasses transfer step-by-step work instructions for setting up the machine to real machine components. Now, for example, the employee can interactively correct a process error that led to a machine standstill on the 3D model without any further assistance being required. In this example, it is the breakage of a weft thread.
A new feature of this model is the interaction of real and virtual machine parts within an application using mixed-reality technology.
The target groups for this learning environment are in particular textile and textile machine manufacturers as well as textile training institutions.
The learning environment described above can be viewed in the shop window of the Mittelstand 4.0-Kompetenzzentrum Textil vernetzt in the Digital Capability Center in Vaalser Straße 460 in Aachen, Germany. An individual application can be developed within one to six months, depending on the level of detail and the scope of the mixed-reality applications. For further information please contact arash.rezaey@ita.rwth-aachen.de.
ITA looks forward to seeing you at ITMA in the Under Linkway booth D221 (UL D221)!