Composites
PURCELL – a renewable composite material made of pure cellulose
At the moment the only technically applicable concept entails thermal processing and the use of the remaining glass-fiber waste products after pyrolysis as an additive to cement. There is definitely no recycling, in the true sense of the word. The urgency of the recycling problem is being accelerated by statutory regulations, which force manufacturers to take their products back.
Substitution of GRB construction components
Because there is still no evidence of a real solution for true recycling of GRP materials in the future, the new research project at the ITCF Denkendorf aims towards finding a substitute for these materials. A new, pure, recyclable composite material of pure cellulose presents an alternative. This should ensure a safe, stable and affordable supply of raw materials for the GRP manufacturing industry.
The biopolymer cellulose is used both as a high-strength reinforcing fiber and as a matrix component. In this way, a pure, chemical composite made of cellulose, (“PURCELL”) will be generated, which can be completely recycled by means of technologies that already exist. The purity of the PURCELL composites thereby guarantees a technologically simple recycling process.
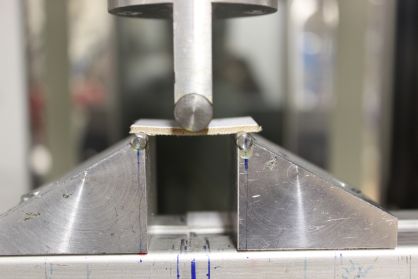
Pic: PURCELL plate during three-point bending tests © 2016 DITF Denkendorf
The laboratory samples that have already been produced indicate that the PURCELL composites have a comparable range of properties, compared to GRPs and that they are already achieving the mechanical parameters of thermoplastic GRP plates, the so-called organic sheets.
Because the new composite materials are made of 100% renewable cellulose, both local wood and local reinforcing fibers such as hemp and flax can be used as a source of the raw material.
The aim of this development is for the new composite materials to achieve all of the technical parameters of standard GRP composite materials. Only in this case will it be possible to substitute GRPs with PURCELL. Although the PURCELL lab samples almost match the properties of GRPs, the range of requirements still has to be extended in terms of larger samples. This up-scaling is a technical challenge, which still needs to be tackled.
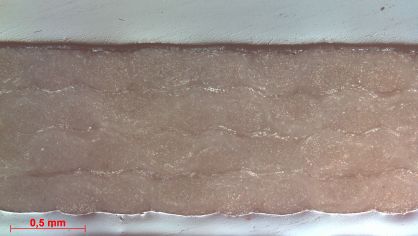
Pic:PURCELL composite panel (cross-section), consisting of 4 layers of woven material © 2016 ITCF Denkendorf
Simple manufacturing process
The manufacture of this new material originated from ITCF’s development work on the environmentally friendly manufacture of cellulose fibers from ionic liquids (IL). During this work, we were able to produce highly concentrated solutions of the poorly soluble cellulose, due to the addition of the new ionic liquids. Due to the highly variable setting options of the flow properties of these liquids, we came up with the idea of applying these spin masses as matrix components in composite materials. As reinforcing fibers, technical cellulose tire cord fibers and natural fibers such as cotton, flax and hemp were used.
The structure of the PURCELL composite materials is technologically very easy to implement: Textiles are coated with the highly concentrated cellulose IL solution. Depending on the desired final thickness of the composite, an appropriate number of layers are applied. Thereafter, the pre-layers of the composite are pressed and the IL is rinsed out with water. Drying and consolidation of the composite takes place in a hot press. The IL is distilled out of the rinsing water for reuse. When pressing the pre-layers, the reinforcing fibers are dissolved superficially, thereby bonding them inseparably to the cellulose matrix. This is what gives the material its surprisingly good mechanical composite properties.
One has complete freedom with regard to the design possibilities by adjusting parameters of the composite. For instance, the composite body can be coated with a cellulose matrix layer on one side. This compact cellulose layer is extremely resilient and easily processable (painting, topcoat etc.)
The renewable raw material offers significant advantages due to its comprehensive recycling cycle. The Purcell plates are cleaned, shredded, dissolved in an ionic liquid and once again applied as a matrix. The compostability of the waste products that cannot be reused has not yet been tested, but it is a known fact that cellulose composts well. Based on these systemdependent properties, no waste is generated in the end-of–life state. In terms of costs, cellulose raw materials are also very competitive.
The cooperative PURCELL project between the ITCF and the ITV is funded by the Ministry of Finance and Economy, Baden-Württemberg under the category of “Technological Protection of Resources”.