Composites
The JEC Composites Innovation Awards: 2023 Official finalists line up
- The competition is open to any company or R&D Center with a strong collaborative innovation or concept to present. The success of each competitor is closely linked to the partnerships and collective intelligence involved.
More than just a ceremony, these awards, in partnership with KORDSA, are an opportunity to bring possibly undisclosed projects in the limelight as well as a source of inspiration and stimulation to an expert audience always eager to reach out towards new horizons.
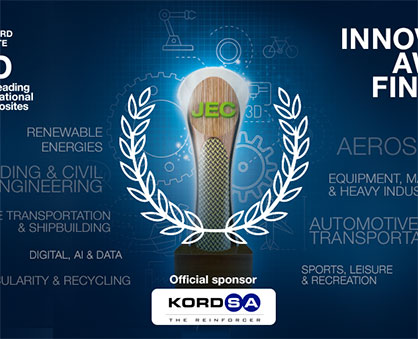
After pre-selection of the 30 finalists, one winner will be selected in each of the 11 categories:
Aerospace – Parts
Aerospace – Process
Automotive & Road Transportation – Design Part
Automotive & Road Transportation – Process
Building & Civil Engineering
Circularity & Recycling
Digital, AI & Data
Equipment, Machinery & Heavy Industries
Maritime Transportation & Shipbuilding
Renewable Energies
Sports, Leisure & Recreation
The international jury representing the entire composites value chain includes:
• Dr. Deniz KORKMAZ, Chief Technology Officer, Kordsa Teknik Tekstil AS
• Pr. Véronique MICHAUD, Head of the Laboratory for Processing of Advanced Composites, Ecole Polytechnique Fédérale de Lausanne
• Dr. Alan BANKS, UK Innovations Manager, Ford Motor Company
• Pr. Christophe BINETRUY, Professor of Mechanical Engineering, Centrale Nantes
• Mr. Dale BROSIUS, CCO, IACMI-The Composites Institute
• Dr. Enzo COSENTINO, Technical Authority and Composite Expert, Airbus
• Mr. Guy LARNAC, Materials, Structures & Industrialization Technical Coordinator, Ariane Group
• Dr. Karl-Heinz FUELLER, Manager Future Outside & Materials, Mercedes-Benz
• Pr. Kiyoshi UZAWA, Director / Professor, Innovative Composite Center, Kanazawa Institute of Technology
• Pr. Sung Kyu HA, Professor, Hanyang University
• Mr. Michel COGNET, Chaiman of the Board, JEC
The awards ceremony will take place in Paris on March 2nd, 2023.
Discover here the finalists in each category!
CATEGORY: AEROSPACE – PARTS
Hybrid seating structure
Fraunhofer ICT (Germany)
ict.fraunhofer.de
Partner(s): Alpex Technology GmbH, Austria – AMADE-UdG, Spain – Leitat, Spain
Aircraft hybrid seating structure designed and demonstrated under sustainability criteria, based on easy to recycle light weight composite material and produced with efficient automated processes.
Commercial aircraft seats consist of many materials and individual parts, mostly a mix of polymers and metals, so very complex to recycle. The seats must also be lightweight to increase the overall efficiency of the aircraft. To achieve both goals (lightweight and recyclability), an aircraft seat series was developed based on the following sustainability criteria:
- Ease of recycling using one polymer type for all polymer parts for which recycling process is available.
- Reduction of number of seat components and weight through function-integrated lightweight design.
- Effective production of the plastic components through processes suitable for series production
- Elimination of toxic primers to improve the adhesion of metal inserts to the polymers (…).
Key benefits
- Fuel Sustainable PU based light weight CFRP to reduce CO2 emissions and waste.
- Radically reduction of numbers of seat parts for low maintenance.
- Automated high volume production technologies (SMC/WCM) to reduce costs
- Reduce the economic cost for carbon fiber aircraft seats
- Carbon Fiber attractive design
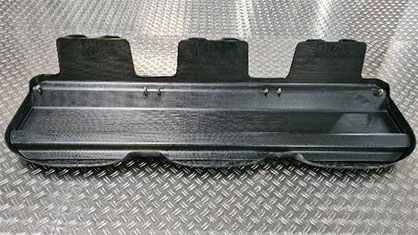
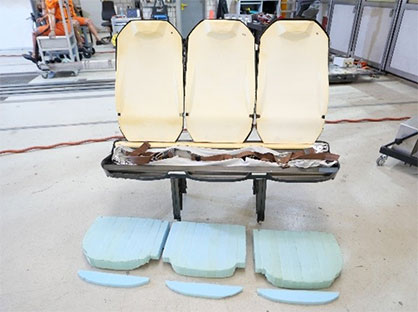
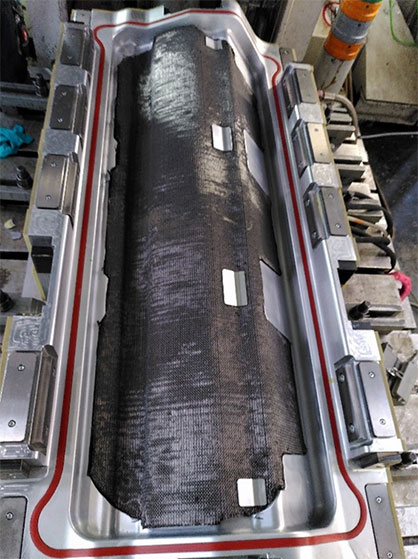
Integrally Stiffened TP Primary Structure
Nikkiso (Japan)
nikkiso.com
Partner(s): A&P Technology, United States – Solvay Japan, Japan
Development of a high-rate molding process using aerospace qualified thermoplastic materials for parts with complex geometries enabling the replacement of heavier metallic components with composites.
Nikkiso, Solvay and A&P have been working in partnership during the last two years to address industry your composite innovation needs for high rate, sustainable, complex geometry components targeting primary and secondary structures for aerospace and AAM (Advanced Air Mobility) market for small to mid-size applications. This innovation consists of the development of Nikkiso’s design of the integrated stiffening component allowing a one-shot processing technology which eliminates multiple fabrication processes. Total process time is reduced from 7 hours to 1 hour (…).
Key benefits
- Unique design as integrated stiffened panels made with continuous fiber.
- A&P’s ability to tailor the material width/real weight eliminates material waste.
- Solvay’s sustainable thermoplastic tape allows ease of processing and reforming.
- High quality one-shot fabrication without large trim and auxiliary materials
- Highly drapable with aerospace performance
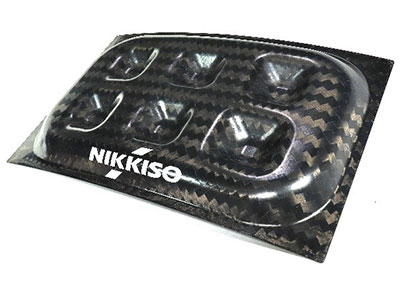
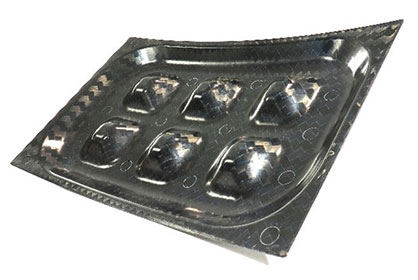
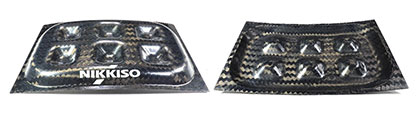
Lunar Lander with Carbon Monocoque Structure
Toray Carbon Magic Co., Ltd. (Japan)
carbonmagic.com
Partner(s): ispace, inc., Japan
Lightweight structure by committing completely to the pursuit of specific strength and stiffness.
Encouragement of the airframe structure as close to a one-piece composite structure
On December 11, 2022, ispace launched a lunar lander on a SpaceX Falcon-9 rocket which now continues to maintain a stable attitude and power supply. The precedents to be set by ispace, which is expected to land on the moon in April 2023, could strongly influence future directions in the concepts for lander form and structure. Understanding that weight reduction of the structure for Luner Lander is a critical factor that impacts the efficiency of its business, ispace and Toray Carbon Magic planned a lightweight structure that is optimal in principle by committing completely to the pursuit of specific strength and stiffness in materials, structure, and fabrication methods (…).
Key benefits
- Carbon Composite Monocoque Structure
- Sandwich-Structured Composites
- Mandrel-Molded Process with Cost-Effective
- Integrated Composite Structure
- Speedy Development Production in Composite Parts
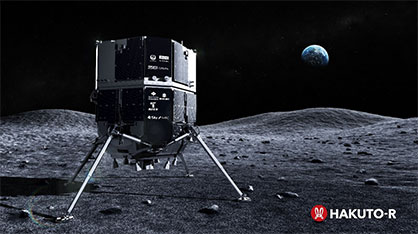
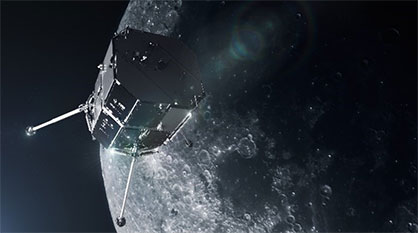
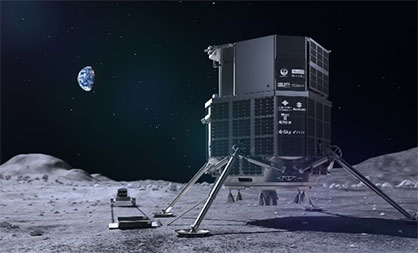
Manufacture a Krueger wing flap in thermoplastic.
CETIM (France)
cetim.fr
Partner(s): Loiretech, France – AFPT GmbH, Germany – SONACA SA, Belgium
Innovative Krueger Flap produced In-situ with an automated thermoplastic process.
The innovative Krueger flap, produced through this multi-partner project, has a large and complex shape and was manufactured using an in-situ thermoplastic consolidation process. It outperforms existing processes in terms of structural and industrial performance with higher production, better process stability and improved composite quality (…).
Key benefits
- In-situ consolidation with full automated process (laser filament winding)
- Recyclability (thermoplastic part)
- Repeatability and reliability of the process
- Reduction of production costs
- Mass reduction of large parts
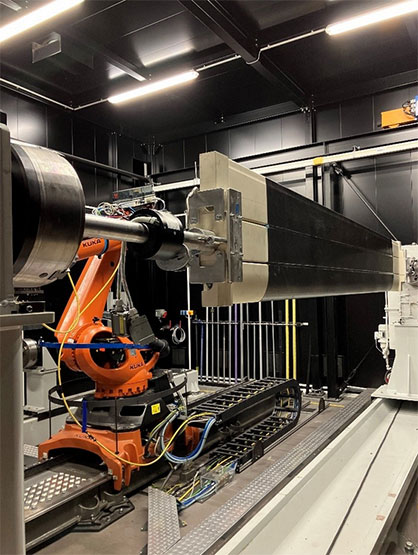
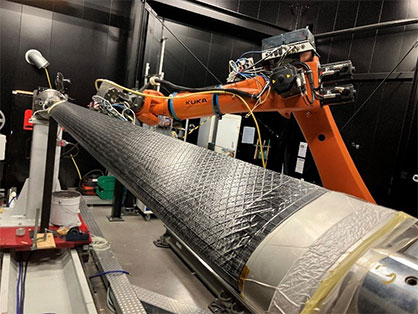
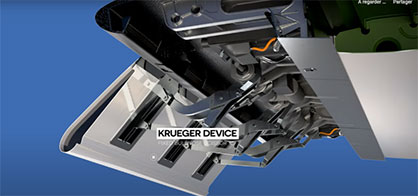
Self-Cure of CFRP for Aerospace Applications
The AMRC with Boeing, Wallis Way, Catcliffe (UK)
amrc.co.uk
Partner(s) : Embraer RT Europe, Portugal
Self-Cure is joule heating of CFRP to cure temperature, significantly increasing the energy efficiency of the curing process, reducing cure time and increasing the quality of cured components.
Self-cure utilizes the Joule effect to heat conductive carbon fibers in composite components up to their cure temperature. This was developed in the H2020 project MASTRO, from small lab scale panels, up to 2-metre-long aerospace inspired components. Using self-cure, it was possible to cure pre-preg and VARTM components using less than 1% of energy compared to oven-cured components (…).
Key benefits
- Low energy curing of CFRP
- Low capital expenditure
- Higher quality laminates
- Almost limitless size constraints
- Path to more multifunctional composites
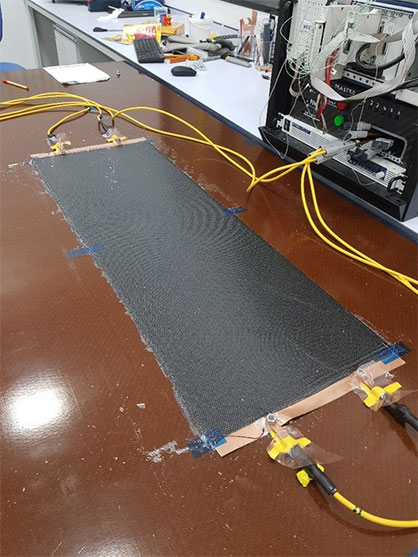
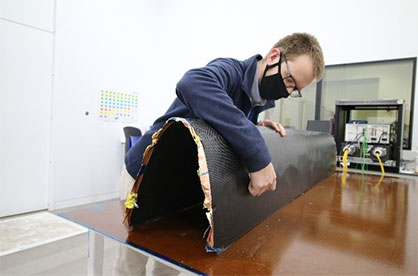
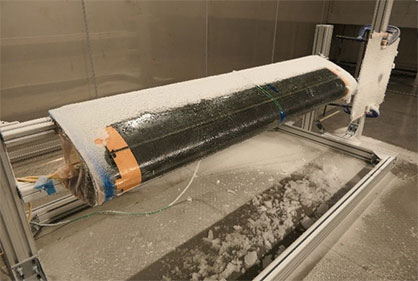
Hydrostatic Membrane Press Technology for Composites
CTC GmbH (Germany)
ctc-composites.com
Partner(s): Airbus, Germany – Siempelkamp Maschinen- und Anlagenbau GmbH, Germany
The metal membrane press concept allows for the production of high-temperature thermoplastic composites using a flexible metal tooling side to achieve high laminate quality and production rates.
The idea of the technology is the use of a thin, flexible steel membrane for pressure application in composite manufacturing processes. With this technology, the disadvantages and tolerance issues of using hard-hard tooling are mitigated. The flexibility of the membrane compensates all thickness tolerances in the laminate, creating a perfect consolidation. This technology also enables the consolidation of a skin structure while integrating stiffening elements such as stringers in a single process (…).
Key benefits
- Hydrostatic pressure yielding a perfect processing pressure
- One-Shot consolidation and integration for high production rates
- No auxiliary materials necessary, which greatly contrasts autoclave or oven
- Cycle times of 1h for high-temperature thermoplastics lead to lower energy use
- High versatility, as the same upper tooling can be used for multiple parts
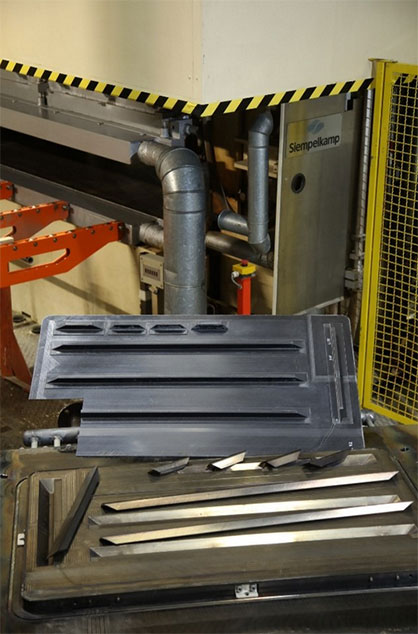
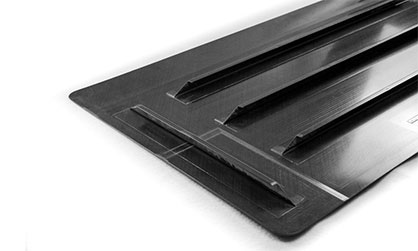
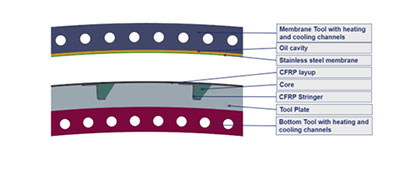
CATEGORY AUTOMOTIVE & ROAD TRANSPORTATION – DESIGN PART
2022 Toyota Tundra™ Composite Seatback Design
L&L Products (United States)
llproducts.com
Partner(s): BASF Corporation, United States – Toyota, United States
Taking an all-steel assembly that contained 60 stamped and welded parts and integrating it into 4 composite parts reducing weight by 20% while passing all relevant crash test requirements.
L&L Products CCS™ (Continuous Composite Systems) CCS™ are continuous fiber-reinforced composite materials that can be used as a carrier when combined with our highly engineered sealants and/or structural adhesives. This two-dimensional part is designed to provide strength, stiffness, and rigidity to a lightweight structure. This is the first interior application to use L&L Products Continuous Composite Systems (CCS) technology with BASF’s polyurethane pultrusion system Elastocoat 74850 (…).
Key benefits
- In-house engineering expertise
- Advanced CAE capabilities
- Ultra-high strength to weight ratio
- Competitive pricing
- Seamless integration of adhesives/sealant
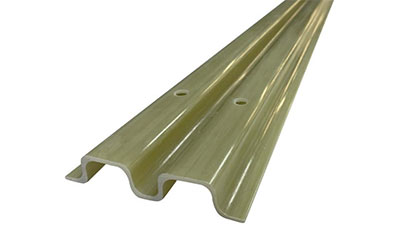
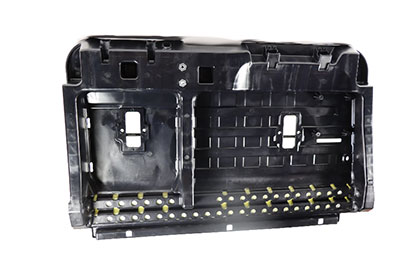
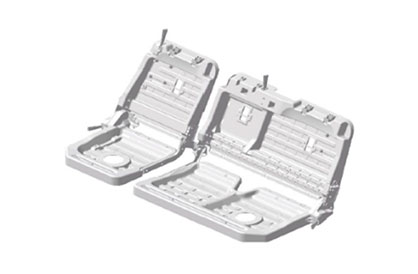
World’s first carbon roll cage for production cars
Dr. Ing. h.c. F. Porsche AG (Germany)
porsche.de
Partners(s): Action Composites GmbH, Austria – Kube GmbH Ingenieurbüro, Germany – Lab for Lightweight Design, IKTD, University of Stuttgart, Germany
Extreme lightweight carbon roll cage, to be road legally fitted into a production car, enabled by engineering a unique geometry.
The initial metal design withstands extreme elongations. Thus, the use of carbon fibers, presented a major challenge for this application due to the low elongations at break. The Engineering innovation of the project is a new 3 step structural optimization process providing a specific design suitable for CFRP under full consideration of an extremely limited design space as well as multiple crash and FIA load cases (…).
Key benefits
- High weight reduction compared to steel and even titanium
- Topology optimized, unique bionic design
- Innovative calculation approach – automated link between CAD an FE
- Innovative manufacturing process – structural hollow part in serial production
- Fulfills FIA load collective
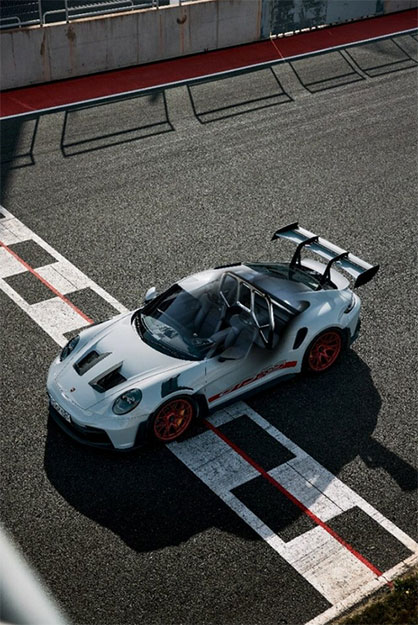
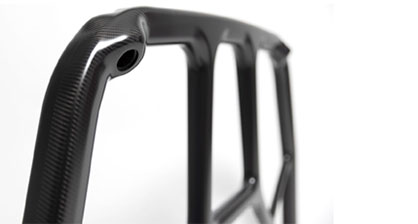
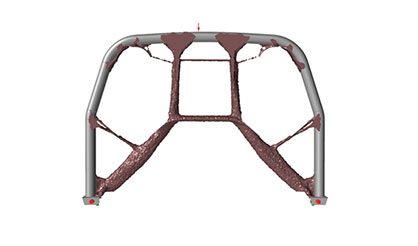
DRIFT-Technology
Brose Fahrzeugteile SE & Co. KG, Bamberg (Germany)
brose.com
Partner(s): 1 A Autenrieth Kunststofftechnik GmbH & Co. KG, Germany – Dr. Ing. h.c. F. Porsche Aktiengesellschaft, Germany – Fraunhofer IGCV, Germany – Kube GmbH Ingenieurbüro, Germany – WAFIOS AG, Germany
Wire-shaped inserts for load-oriented fiber reinforcement of injection-molded thermoplastic components.
Implemented on two full-scale industrial demonstrators within the automotive sector The DRIFT-Technology features a combination of thermoplastic pultrusion, wire bending technique and injection molding technology. This new technology combines large-scale production capability, cost efficiency, design freedom and sustainability to an unmatched degree (…).
Key benefits
- Topology-optimised load-adapted 3D-design-freedom
- Disruptive structural/functional property profiles
- Large-scale production capability
- Significantly enhanced cost-efficiency & material-utilization
- Distinct integration of sustainability concept
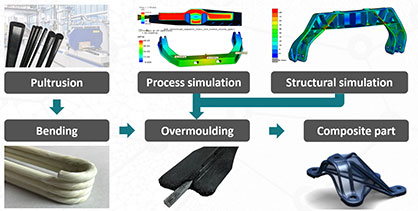
CATEGORY AUTOMOTIVE & ROAD TRANSPORTATION – PROCESS
KORIDION – ACTIVE CORE MOLDING
Alia Mentis SRL (Italy)
alia-mentis.com
Partner(s): Automobili Lamborghini S.p.A. Italy – FERRARI Spa, Italy – FILIPPI Boats Srl, Italy – GEVEN Spa, Italy – MFC Hawaii, United States, SABELT Spa, Italy – SCUDERIA ALPHATAURI Spa, Italy – SUM Srl, Italy
Active core molding. The new process that cancel all current limits on CFRP Transformation.
KORIDION is the first active core for the self-forming of CFRP to its final shape. No more autoclaves, No more bags. Its ultralight structure expands by heat, applying equalized pressure to every detail of the CFRP structure within the mold. The viscous behavior absorbs overlaps and all the overall interference involved in the component forming. The Koridion core allows previously impossible forms, is completely fire-proof, is soluble, permits the reduction of CFRP materials guaranteeing ultralight compositions and is easy to use (…).
Key benefits
- Design freedom + impossible shapes + self-forming structures + monolithic
- Equalized pressure up to 12bar + ultralight+ fireproof + shockproof + soluble
- No autoclaves + no bags + simple process
- + 40% CFRP saving + 50% labor saving.
- 50% green-house-gas reduction
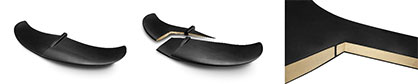
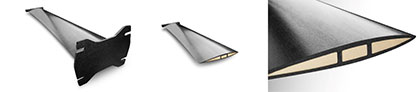
BEV battery protection plate in composite design
AUDI AG (Germany)
audi.de
Partner(s): POLYTEC GROUP, Netherlands
Largest, innovative, sustainable BEV underride guard in thermoplastic sandwich lightweight design with highly efficient one-shot manufacturability for the new Audi Q8 e-tron.
The innovative composite part is characterized by its mechanically extremely robust light-weight sandwich design as well as its large dimensions of about 2100 mm x 1400 mm and a total weight of app. 23 kg, of which about 13 kg are UD-tapes. Due to the large size of the component, production using injection molding is technically not feasible, thus a novel one-shot process had to be developed.
The overall design is an excellent trade-off in terms of lightweight potential, design suitability for cost-efficient high-volume production, mechanical robustness and sustainability (…).
Key benefits
- high light-weight potential for BEV underride guards, replacing Al-design
- significant reduction of CO2-footprint compared to aluminum design
- novel press-process for high-volume production of complex sandwich parts design for recycling
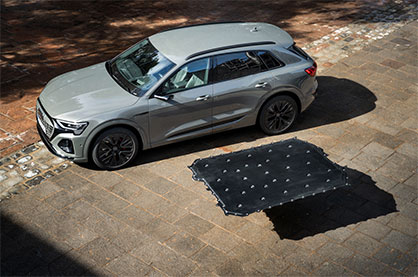
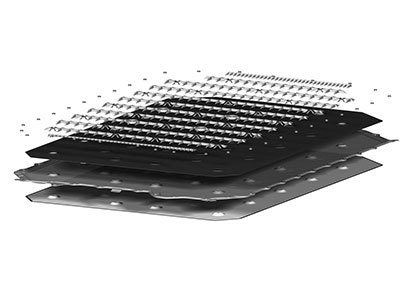
Graphene from waste tire for lightweight vehicles
Nanografen (Türkiye)
nanografen.com.tr
Partner(s): Farplas Otomotiv A. S., Türkiye – Oyak Renault, Türkiye – Ravago Petrokimya Üretim A.?., Türkiye
Nanografen produces graphene from waste tires in pilot scale used as a co-reinforcement in compounding process for cost-effective and lightweight automotive composites without changing the mould.
Nanografen scaled up the upcycling sustainable graphene manufacturing technology by using the recycled carbon black obtained from the pyrolysis of waste tires. In this process, the conversion of waste tires to carbon black is 35% and the reaction is occurred under nitrogen environment at 450°C by using catalytic bed process (…).
Key benefits
- Sustainable graphene manufacturing from end-of-life tires in pilot plant scale
- Lightweight design by reducing main reinforcement and integrating graphene
- Ease thermoplastic processing with graphene requiring no additional treatment.
- Lowering cost of graphene by using end-of-life tires compared to prime graphene
- Large volume production capacity and easily scalable process
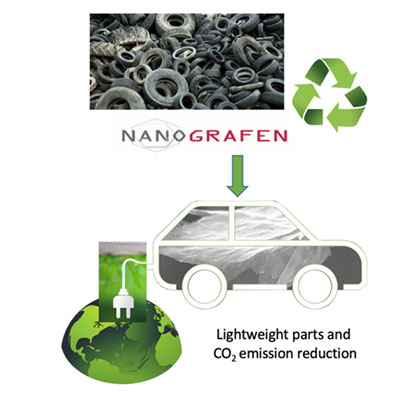
CATEGORY BUILDING & CIVIL ENGINEERING
CFRP Cable-Net Glass Façade
CARBO-LINK AG (Switzerland)
carbo-link.com
Partner(s): seele, Germany
An innovative and novel CFRP cable-net structure for glass façades providing maximum transparency with no visible supporting structure, enabling a clear design language for building envelopes.
The CFRP cable-net innovation is an evolution of seele’s steel glass design façades integrated into some of the world’s most recognizable architecture. Combining seele’s innovative glass panels and engineering experience with Carbo-Link’s CFRP tension members has led to a new structural solution for large-scale glass façades (…).
Key benefits
- High tensile strength capacity = increasing ability to carry structural load
- Super lightweight = less superstructure demand at more extensive project scale
- No relaxation over lifespan = high level of pretension maintained over the life
- No service demands = increased active lifespan, reduced cost of ownership
- Small cross-section = hidden structural components for increased transparency
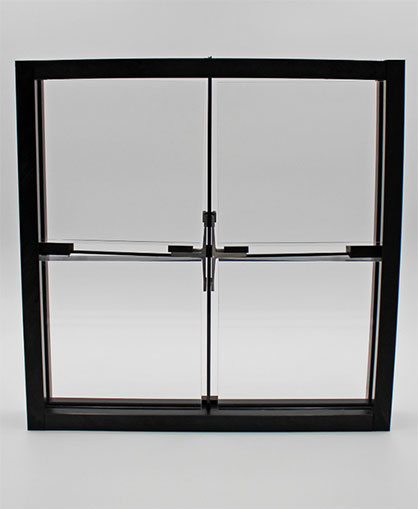
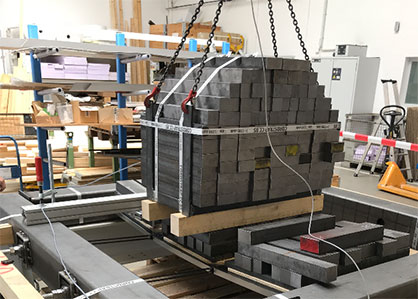
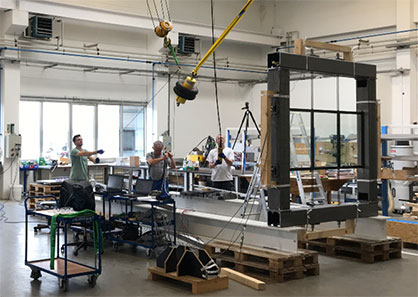
Sheephouse Wood Bat Mitigation Structure
Asset International structures (United Kingdom)
assetint.co.uk
Partner(s): COWI UK, United Kingdom
Provide a safe structure, ensuring the protection of a rare species of the bat using offsite modular construction, minimizing embodied carbon, and maximizing safety using our FRP and concrete units.
Our use of innovative FRP composites for the mesh panels was driven by the design scope. Part of the original requirement was for a minimal maintenance structure to reduce future maintenance costs for the stakeholders which we reviewed and proposed the current adopted design. Using FRP allowed us to create a system that met all the design loadings, 60% open porosity for aerodynamic loads, met smoke and toxicity requirements, created small enough apertures that the bat species cannot enter the structure and allowed for minimal maintenance over the lifespan of the structure (…).
Key benefits
- Showcasing FRP In Major Infrastructure Projects such as underground projects
- Protecting the habitat & 13 species of bats including the rare Bechstein’s bat
- Reduced long term maintenance offering low life costs
- Construction time reduced minimising the effect on local population & wildlife
- Reduces the construction time thus the overall construction cost

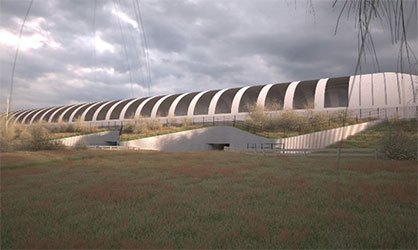
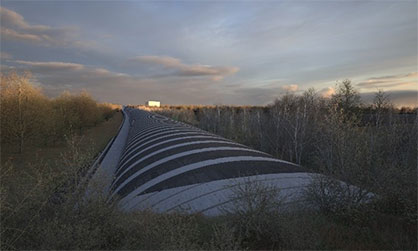
A Composite Roof for The Stadium Of Real Madrid
Nanotures (Spain)
nanotures.com
Partner(s): COMPOSYST, Germany – DIAB, Spain – FIBERTEX, Denmark – Gavazzi, Italy – MAP Yachting, France – MEL, Spain – SAERTEX GmbH & Co. KG, Germany, Sicomin, France – SKY, Hungary – Zoltek, Hungary
Three elements are mechanically joined to reach beams with a span of 75 m. The manufacturing process was infusion with double VAP membrane, avoiding the use of holes in the core and excess polymer.
Critical parameters such as fiber linearity and core joints have been controlled in production to obtain elements with high compression resistance. Strategically, different reinforcements have been utilized in the design to meet the load case and assist in joining to the metallic elements. Finally, the lightweight composite beams allow simplification in the assembly operations on site as well as the simplification, weight and energy reduction of the displacement and elevation motors.
Key benefits
- Weight reduction and simplification on site installation
- Excellent mechanical properties
- Environmental and energy benefit
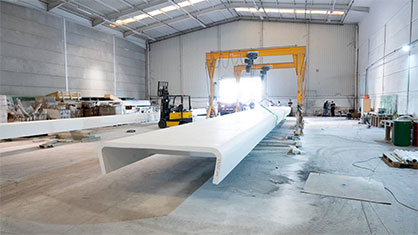
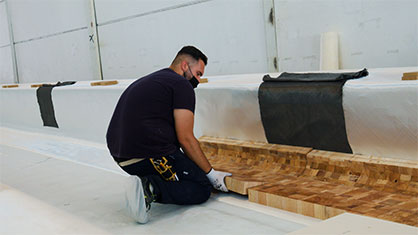
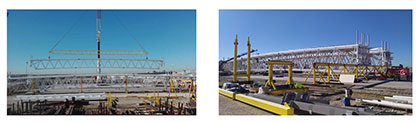
CATEGORY CIRCULARITY & RECYCLING
Circular Welding Process for Thermoset Composites
University of Applied Sciences and Arts Northwestern Switzerland (Switzerland) fhnw.ch/d
Partners(s): HUNTSMAN ADVANCED MATERIALS SWITZERLAND GmbH, Switzerland
A super-fast, reusable welding process that creates high-performance joints between fast-curing epoxy composites involving a co-bonded thermoplastic interlayer that enables the design for circularity.
To achieve this, a thermoplastic coupling layer is created by co- bonding with the thermoset resin. This leads to a weldable surface that can be processed with thermoplastic welding methods such as ultrasonic welding. The thermoplastic coupling layer (phenoxy resin) is utilized as a thin film, compatible with the fast-curing epoxy system Araldite® LY3585/Aradur® 3475 in the sense that it can partially diffuse in a controlled way into the thermoset resin during the 1 min curing time at 140°C (…).
Key benefits
- Design for circularity
- Fast welding of thermoset composites
- Lightweight joint design
- CO2 reduction by disassembly and reuse
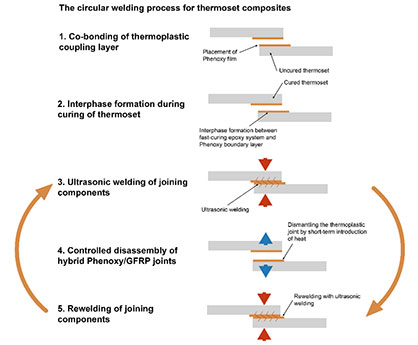
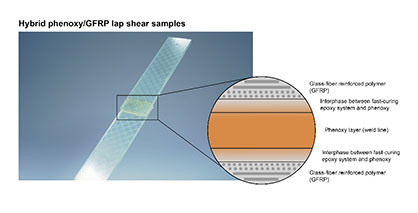
100% Recycled Cf Spun Yarn and Applied Products
TOYOTA INDUSTRIES CORPORATION (Japan)
toyota-industries.com
Partner(s): Kurimoto, Ltd., Japan – Nagoya University, Japan – NAKASHIMA PROPELLER Co., Ltd., Japan – Toyota Central R&D Labs., Inc., Japan – Toyota Motor Corporation, Japan – Uster technologies AG, Switzerland
100% recycled CF spun yarn compatible to pultrusion process. Establishment of comprehensive CF circulation system from recycling to product application.
CFRP properties of rCF spun yarn achieve about 70% tensile strength and 90% elastic modulus compared to virgin CFRP. There is no limitation to the process and matrix, and we are the world’s first manufacturer that successfully utilizes rCF in pultrusion molding with epoxy resin. Due to wind energy market growth, we expect future rCF spun yarn application to the demand for carbon neutral production for wind power generation blades. Furthermore, we established a comprehensive CF recycling system from CF recovery to reproduction (…).
Key benefits
- Applicable recycle CF to pultrusion molding using epoxy matrix
- Recycled CFRP highly compatible with virgin CFRP performance
- A comprehensive high value CF recycling system
- High compatibility for existing process and resin matrix
- Low environmental impact
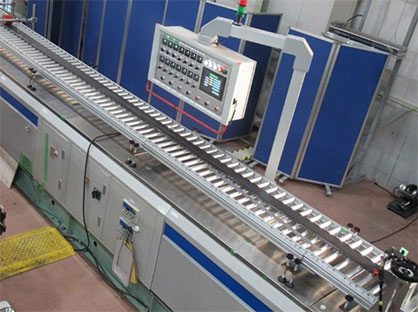
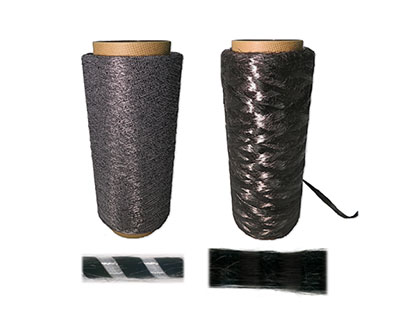
True Bio-Based Thermoset Resin
Evonik Operations GmbH (Germany)
evonik.com
Partner(s): Kemijski Institut,Slovenia
We developed a new, low viscosity thermosetting resin based on lignin. Designed to work with established processes, i.e. VARI, it reduces the carbon footprint of composites significantly.
Vanillin methacrylate, derived from lignin, a waste product from the paper and pulp industry, is the backbone of our new bio-based thermoset resin. Our innovation converts this solid material into a liquid suitable for commercial peroxide hardeners. We made composite panels using flax fiber fabric and VARI (vacuum-assisted resin infusion) equipment. Testing with benchmark materials (epoxy and vinyl ester resins) showed a comparable performance of the laminate. By optimizing the hardener package the performance can be enhanced further.
Key benefits
- 75 % carbon footprint reduction
- Bio-based from waste material of the paper and pulp industry
- Easy to use, low viscosity
- Excellent performance, especially in combination with flax
- Drop-in thermoset resin
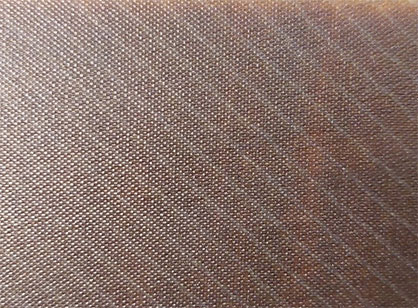
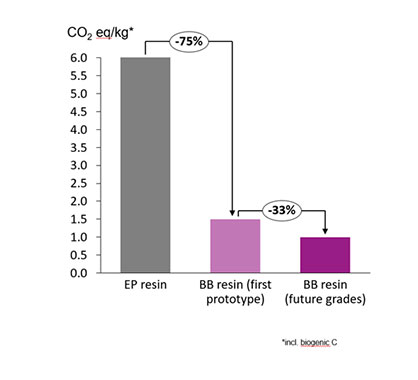
CATEGORY DIGITAL, AI & DATA
Auto-Teaching Algorithm for Thermography
Twin Robotics (France)
twin-robotics.ai
Thermography is a fast way to robotically inspect a composite part. The innovation lies in an auto-teaching algorithm that automatically defines the optimal path(s) for inspection.
Currently, industrial robots automate repetitive tasks (e.g. automotive ind), Industry 4.0, however, demands more flexible, easier to program, and smarter robots that are capable of performing tasks on a small series or parts or even single parts. This flexibility requires being able to define the tasks that the robot must do in a simple way. The programming of a robot must be able to be done in a few minutes by a person with no knowledge of robotics. With our software – AppRob – we offer a digital twin of the robotic inspection machine that reduces programming time to a few hours for experts in NDT and not in robotics (…).
Key benefits
- Automatic Off-Line Programming (OLP)
- Full simulation of Thermographic Machine
- No knowledge in Robotics needed
- Design a complete Digital Twin for the robot system
- Shrink the OLP time to the minimal possible
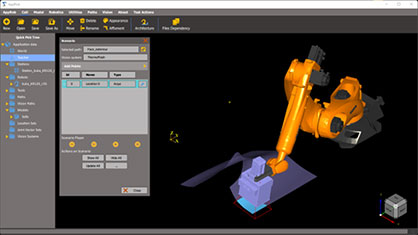
Ai-Powered, Cloud-Based Real-Time Process Control
NETZSCH Process Intelligence GmbH (Germany)
sensxpert.com
Partners(s): CARBON REVOLUTION LTD., AUSTRALIA – German Aerospace Center and the CosiMo Project, Germany – NETZSCH Group, Germany – Schwarz Plastic Solutions GmbH, Germany
sensXPERT is an end-to-end, integrated equipment as a service solution for the plastics manufacturing industry solving challenges around consistent process stability while ensuring cost efficiency.
Dielectric sensors are the heart of the system, favorably positioned at or close to the main gate, while the second one sits best at the end of the flow—regardless of part size. Data collected by the sensors are transferred to the sensXPERT edge device, which is placed machine near. The edge device acts as an industrial PC with the main task of evaluating and communicating the data received to the Cloud via secured servers maintained by Amazon Web Services.
Key benefits
- Real-time process cycle optimization
- In-mold process control
- Full tracking/traceability for every part produced
- Up to 50 % scrap reduction & 23 % energy cost savings
- Optimized use of human-based resources
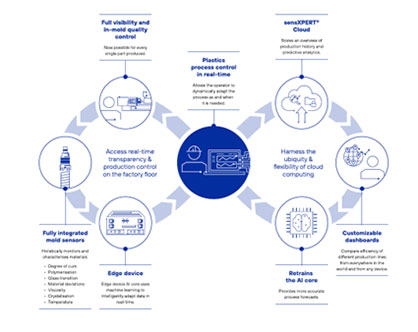

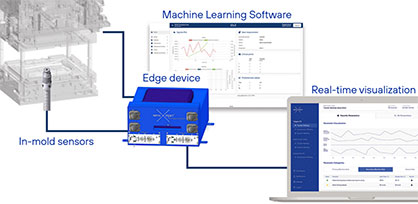
In-Process Afp Manufacturing Inspection System
NIAR/WSU (United States)
wichita.edu
In-process AFP Manufacturing Inspection System (IAMIS) for automated fiber placement (AFP) head to detect manufacturing defects and a user-friendly augmented reality visualization module.
IAMIS detects manufacturing defects that are above the certification basis (or unacceptable) using machine-learning (ML) algorithms for reducing time-consuming and operator-dependent manual inspection processes that require significantly interrupting the manufacturing process.
Key benefits
- Increase automated manufacturing system utilization (operational efficiency)
- Eliminate labor-intensive manual inspections and improve quality
- Eliminate human error associated with operator experience levels
- Augmented reality visualization for repair and quality assurance
- Create a digital record of defects for certification and sustainment support
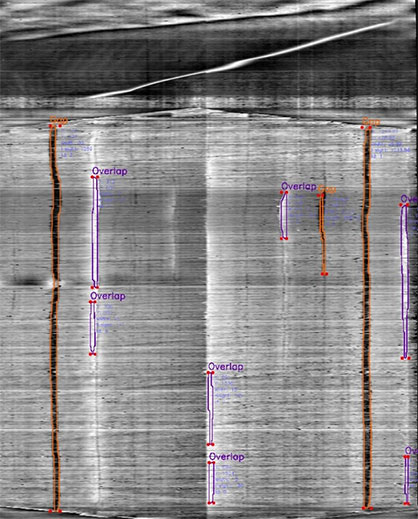
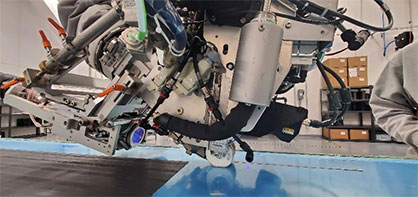
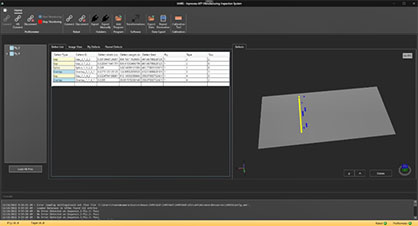
CATEGORY EQUIPMENT, MACHINERY & HEAVY INDUSTRIES
Composite High-Speed Railway Car body
Talgo (Spain)
talgo.comb
Partners(s): Aernnova, Spain – FIDAMC, Spain, TECNALIA, Spain
The development is a hybrid composite car body structure for Very High-Speed train made of CFRP composite and Aluminum with a 25% weight reduction. The demonstrator is a whole carbody of an intermediate coach of Talgo 350 at TRL 6/7 1:1 scale.
Talgo 350 is a High-Speed Train running in Spain since 15 years and Talgo HHR, a variation of it, running in Saudi Arabia since 5 years. The car body is divided in two main parts that are integrated at the end of the assembly process: – End walls, made on aluminum and – CFRP main tube (roof, lateral panels, and floor/main frame) made using monolithic, sandwich and pultrusion profiles. The technologies used to manufacture the composite components (apart from pultrusion profiles) are based on hand and semi-automatic lay-up CFRP semi-prepreg compliant with the Fire-Smoke-Toxicity standards for the railway. This way, we are removing completely the use of welding on steel and/or aluminum in the manufacturing of the main tube.
Key benefits
- Increase of capacity due to weight reductions
- Decrease of energy consumption
- Simplified assembly process
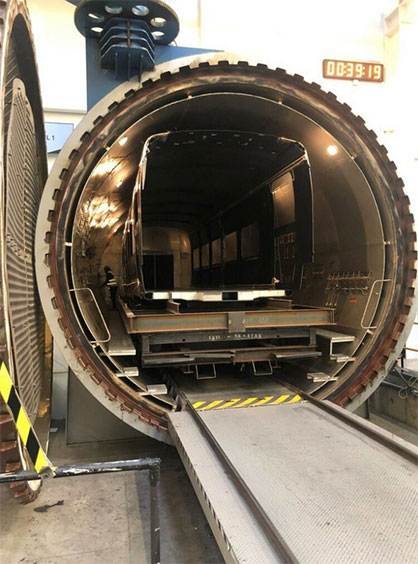
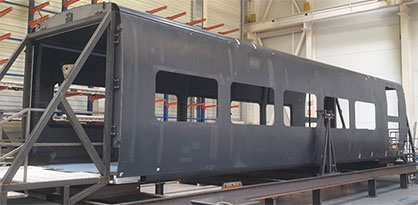
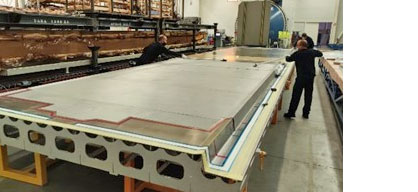
Isotruss® Carbon Fiber Tower
IsoTruss, Inc (United States)
isotruss.com
Partners(s): My Learning Alliance, US – U.S. Bureau of Land Management Wyoming, United States – United States Department of Agriculture National Institute of Food and Agriculture (USDA- NIFA), United States – Utah State University, United States
IsoTruss® Carbon Fiber Towers are up to twelve times stronger than steel for a given weight, or as little as one-twelfth the weight for a given load, depending on the design, site and specifications.
IsoTruss was originally invented for aerospace applications and is ideally suited in load bearing structures anywhere low weight and stiffness are critical. Overall, the IsoTruss® combines high performing continuous fiber (such as carbon, glass, aramid, etc.) reinforced polymer composite materials with a very efficient geometry to allow those elements to carry the load efficiently, allowing extremely lightweight and extremely high performance.
Key benefits
- Material Advantages: High Strength/High Stiffness/High Durability/
- Transversely Isotropic/Radio Frequency Transparent/Corrosion Resistant
- Structural Advantages: Resists Shell Buckling/Lighter Weight/Low Drag/
- Damage Tolerant/Aesthetics/Eco-Friendly/Corrosion Resistant
- Less CF to mfg/lightweight lowers shipping/install costs-reduces CO2 em.by 70%
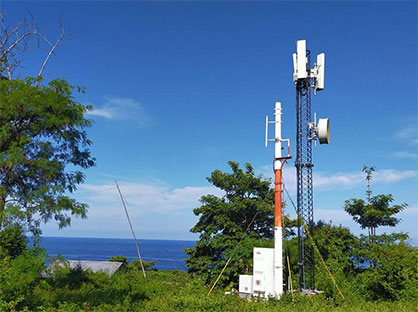
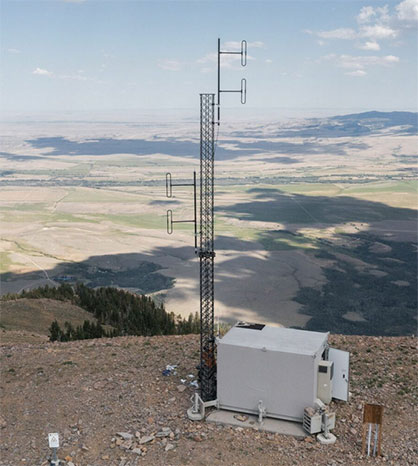
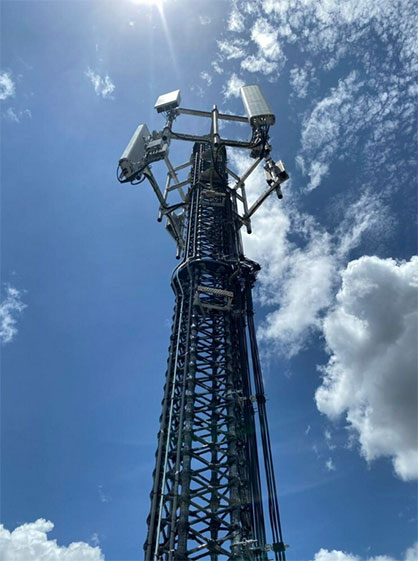
Lightweight Booms for Agricultural Sprayers
BK COMPONENTS S.A. (Argentina)
Bk-comp.com
Partners(s): BCK ID SRL, Argentina – CAIMAN SRL, Argentina – KOHLENIA SRL, Argentin
A modular concept of sprayer boom with intelligent use of composites and manufacturing processes, to provide a scalable, cost efficient and environmentally friendly solution for agriculture.
The composite materials and their manufacturing processes used for the boom are specially selected and developed, aiming for a scalable, cost efficient and environmentally friendly product. The carbon fiber tubes are made by wet filament winding for a high level of automation, the maximum integration in the value chain, and to avoid the higher costs and drawbacks associated to the logistics of prepregs.
The compression-molded composite part is 80% cheaper than its aluminum counterpart and there is a reduction of 66% of the industrial waste (…).
Key benefits
- Longer working span boosts productivity
- Reduced weight and better dynamic response of the spraying booms
- Reduced environmental impact (less fuel/scrap recycling/spot spraying systems)
- Easy repairability thanks to adhesive bonding of the repair kit
- Vertical integration and high automatization of production processes
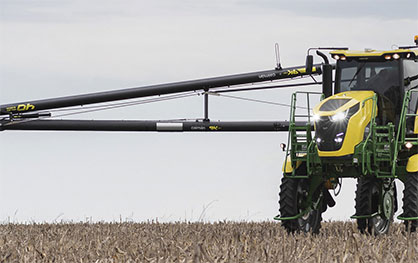
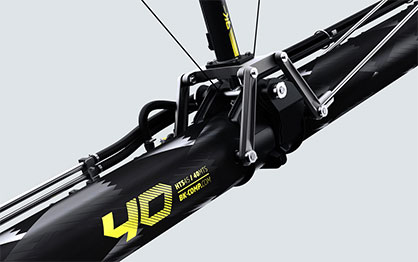
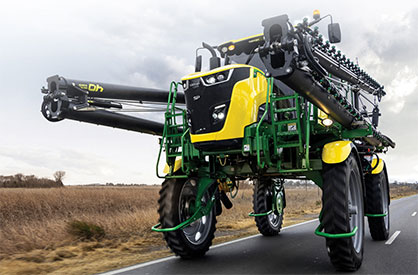
CATEGORY MARITIME TRANSPORTATION & SHIPBUILDING
Automated, Mouldless Composite Wing Sail for Yacht
Rondal (Netherlands)
rondal.com
Partners(s): Artemis Technologies, United Kingdom – Curve Works, Netherlands.
Rondal, Curve Works and Artemis Technologies present a fully customizable, automated, composite solid wing sail assembled from load bearing carbon fiber skin panels manufactured on adaptive tooling.
Rondal, Curve Works and Artemis Technologies are seeking to increase the market share of wind propelled yachts and have created a highly efficient, automated, composite solid wing sail technology that can be “ready-to-sail” in seconds, further increasing the amount of time vessels rely solely on clean, renewable wind propulsion (…).
Key benefits
- Fully automated composite wing sail technology for lower emission yachts
- 100% sustainable wind propulsion with lowest possible manufacturing footprint
- Innovative structural assembly created from multiple prepreg carbon panels
- Modeless, scalable, customizable manufacturing process with integrated heating
- Maximizes sailing time and comfort, ready to sail in only 10 seconds
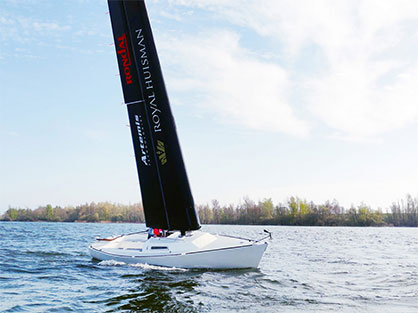
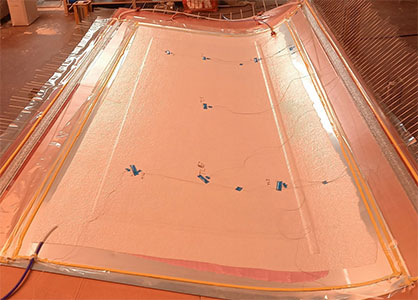
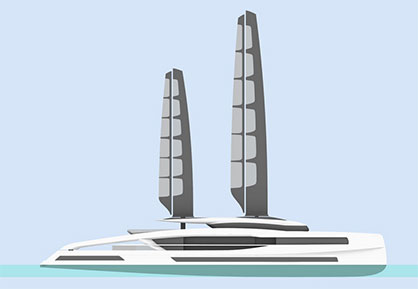
Solid Sail Mast
CHANTIERS DE L’ATLANTIQUE (France)
chantiers-atlantique.com
Partners(s): AVEL ROBOTIC, France – BUREAU VERITAS, France – CDK, France – HEXCEL, France – LORIMA, France – MECA, France – MULTIPLAST, France – SMM, France
Industrialization of the fabrication of very large mast to fit to price and delay of marine industry market.
SOLID SAIL MAST fabrication is based on carbon preg pieces made in autoclave. We cut the mast in sections able to enter the largest autoclave (24m x 6m) we had and develop an assembly method using AFP fabricated sleeves to assembly the 24m long sections together in a quick and efficient way.
Key benefits
- Higher quality standard through precisely automated lamination
- Higher productivity from faster/fewer manufacturing processes
- Lower production cost from reduction of processes
- Reduced waste and reduced manufacturing hazard
- Higher consistency in the mass manufacturing of parts
Serial Use of Hemp For Small Parts In Boating
GROUPE BENETEAU (France)
beneteau-group.com
Partners(s): Chomarat, France
Development and integration of a glass-hemp complex in the industrial production of composite parts in closed mold process for boatbuilding applications.
In boat industry activities, to date, there is no mass production integrating natural fibers. The BENETEAU Group manufactures more than 30,000 composite parts per year to equip its boat decks.
The solution developed by CHOMARAT allows a compromise between the industrial constraints of the small parts production process and customer expectations, all within a sustainable development framework (…).
Key benefits
- Small parts in boat industry.
- Sustainability Improvement
- Serial production marine with Hemp fibers
- Development of local industry
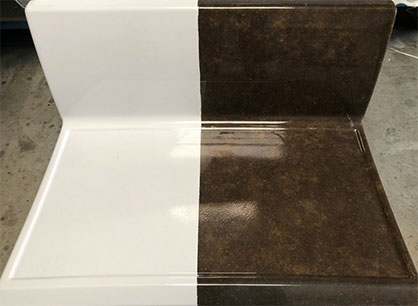
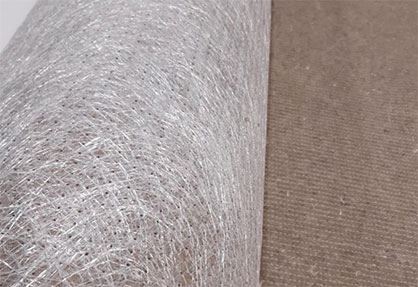
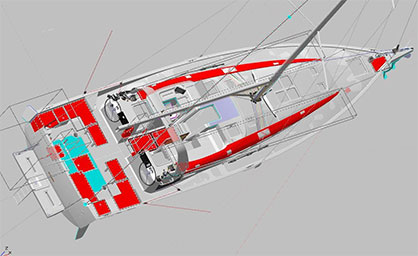
CATEGORY RENEWABLE ENERGIES
New Acrylic Adhesives for A Better World
HUNTSMAN Advanced Materials (Switzerland)
huntsman.com
Partners(s): Antala, Spain – Biesterfeld Oezel Kimy. Tic. A.S., Turkey – Bodo Moeller Chemie GMBH, Germany – Emanuele Mascherpa S.p.A, Italy – Samaro, France – VIBA NL, Netherlands.
New technology of non-flammable, low-odor, and primer-free structural acrylate adhesives with a favorable health and safety profile, providing exceptional bonding performance on multiple substrates.
The innovation is a new acrylic adhesives technology that cures fast, creates high strength and high elongation bonds, outstanding stress and impact resistance, and importantly, unlike many structural
adhesives, provides an effective solution to multiple sustainability-related challenges, without
compromising performance (Non-flammable classification, favorable health and safety profile, Low odor and limited surface preparation) (…).
Key benefits
- Safety, wellbeing, and productivity
- Reduced CO2 emissions (transport)
- Financial savings (storage/protection)
- Performance, multi-substrates, and composites bonding
- Material models available for simulation
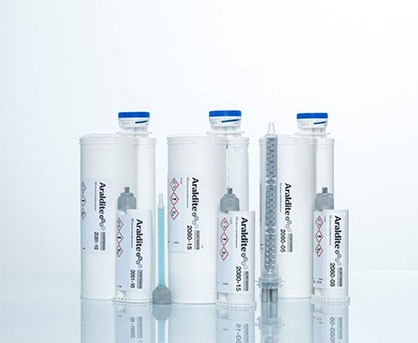
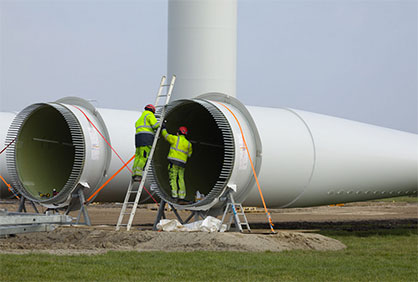
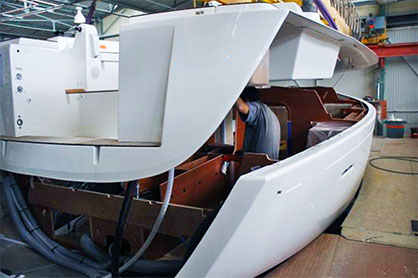
Opticore Design Platform for Blade Lightweighting
Gurit (Switzerland)
gurit.com
OptiCore is a software enabling more efficient core kits for wind blades – considering mechanical properties, geometrical fit, blade weight, resin uptake, manufacturing cost, health, permeability.
Thanks to this new OptiCore software solution, product design parameters can be considered.
simultaneously. Design parameters are often interdependent and impact each other. The software
mitigates this complexity by considering these interdependencies reliably and quickly (…).
Key benefits
- Reduced cost of wind energy
- Faster product development time
- Explore multiple designs quickly
- Improved wind blade mechanical properties
- Cost and weight saving
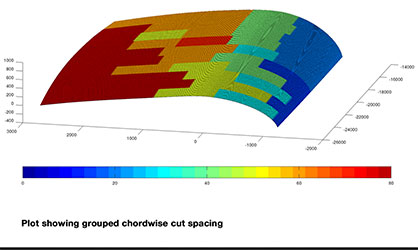
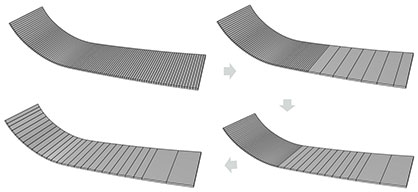
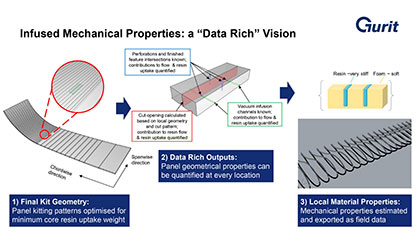
Corpower Wec – Clean Electricity from Ocean Waves
Corpower Ocean AB (Sweden)
corpowerocean.com
Partners(s): Corpower Ocean Portugal Lda, Portugal
Industrial-scale wave energy converter enabled by an innovative mobile filament winding factory for composite hull manufacturing at scale.
The WEC hull has been designed with a low-cost sandwich structure made of filament-wound composite skins for the inner and outer layer separated by a core material. The inner skin combines glass fiber roving and specially developed 141-millimeter-wide bands of fabric – a layer of Diab (Helsingborg, Sweden) Divinycell H structural PVC foam core designed for strength and to adapt to the curvature of the hull – and an outer skin also comprising filament-wound roving and fabric. Composite hulls can be built rapidly on customer sites thanks to a “mobile factory” concept, with additive manufacturing dramatically reducing lead times, cost, and CO2 footprint by eliminating transportation of the finished product (…).
Key benefits
- 20-30% increase in annual energy production (AEP) yield vs. steel
- 70% reduction in end-to-end hull production costs vs. steel
- 15-20% improvement in levelized cost of energy (LCOE) vs. steel
- Increased reliability, robustness and durability in harsh oceans
- Highly scalable onsite WEC hull production via mobile winding factory concept
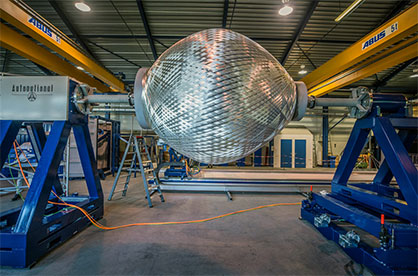
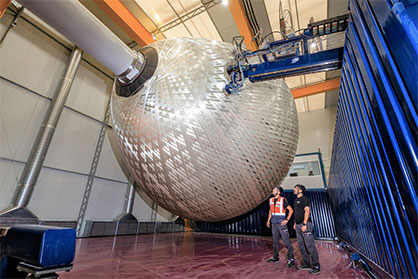
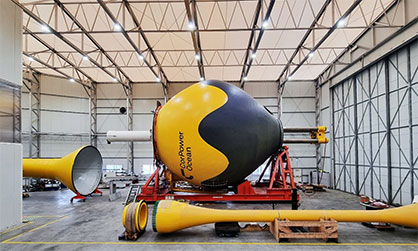
CATEGORY SPORTS, LEISURE & RECREATION
Recyclable Thermoset Cfrp Composite Bike
SWANCOR HOLDING CO., LTD (Taiwan)
swancor.com
Partners(s): GIGANTEX COMPOSITE TECHNOLOGIES CO., LTD, Taiwan
Thermoset CFRP bicycle was made from recyclable EzCiclo prepreg. Composite parts can be recycled by CleaVER liquid to reclaim resin and fiber enabling closed-loop recycling of thermoset composite.
Swancor presents recyclable thermosetting resin “EzCiclo” and degradation liquid “CleaVER”. EzCiclo is a recyclable epoxy resin. Hot melt prepregs made of EzCiclo RB-564 with different Fiber Average Weight (FAW) are used to produce composite bicycle parts including frame, handlebar, front fork and rims. The End-of-life composite parts made from EzCiclo can be degraded by CleaVER liquid at 130°C-150°C for 4 hours, enabling complete separation of matrix and fiber. The crosslinked matrix is dissolved in CleaVER and can be reused. The reclaimed fiber shows comparable properties compared to virgin fiber (…).
Key benefits
- 100% recyclable thermoset composite bicycle parts with promising properties
- Innovative resin system enables closed-loop recycling of thermoset composite
- Ease of adoption with existing manufacturing facilities and processes
- Lower carbon emission recycling and generate no waste
- Higher value of recycled resin and fiber
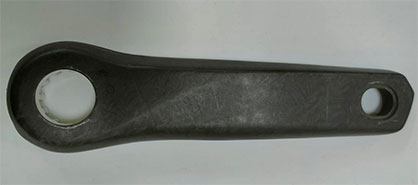
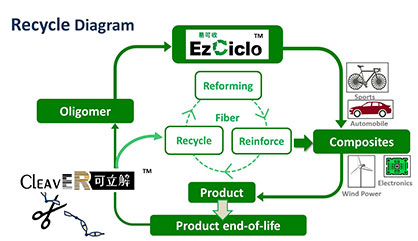
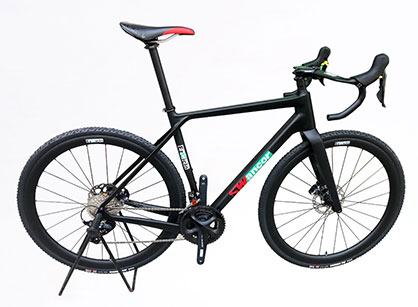
Integrated Loop Technology Bicycle Frame
COMPO TECH PLUS SPOL, s r.o. (Czech Republic)
compotech.com
Partners(s): Czech Technical University in Prague., Czech Republic
A bicycle frame produced by an automated fiber winding process, incorporating continuous fibre tube joining development “integrated loop technology” (ILT).
The proprietary fiber winding and integrated loop process technologies have been used here to manufacture the interconnected frame sub-assembly parts, namely the bottom bracket shell, chainstays and the top, head, down and seat tubular sections of a mountain bike frame. CompoTech’s ILT production processes can manufacture a single large hollow integrated loop end joint or multiple individual loops to accommodate specific fixings and fastener systems.
Key benefits
- More productive than comparative hand built assembled frame
- Stronger joints and efficient material use, eliminating over laminated joints
- Reduced machining – connection designed into the ILT AFL process
- Reduced labour time – higher productivity, lower part cost achievable
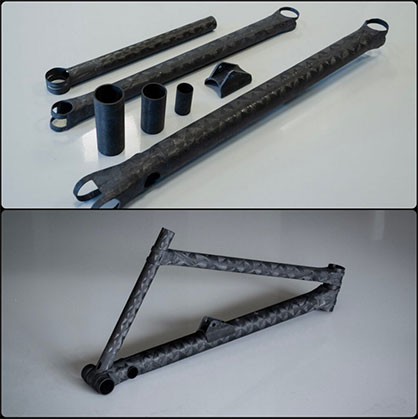
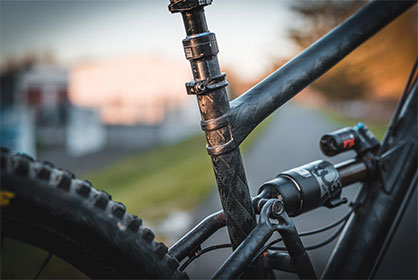
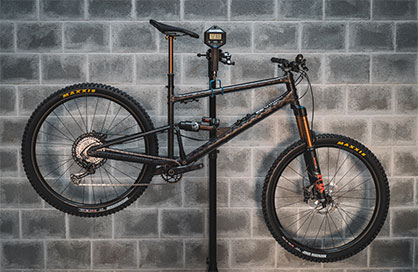
Modular Suitcase Made from rCFRP
PITAKA (China)
ipitaka.com
Partners(s): a-Motion Advanced Materials & Technology Co. Ltd., China – Expliseat, France – Roctool, France
Application of rCFRP and of Natural flax fibers with Roctool TP technology;Recycle & Reusing from Expliseat;Modular design makes it possible to recyle the composite parts from the products.
Innovation is based on dual axis:
New Materials: Develop a variety of materials which accommodate one unique goal which is sturdy and yet a lightweight product. Each design line is using some recycled materials from different industries to show and demonstrate that recycled composite materials can be used to manufacture premium products.
Modular Design: Our most important strategic goal for innovation is to achieve product recyclability. With our approach any consumer can easily disassemble their suitcase & recycle the composites. We can then encourage the end-users to take real action to reduce waste and protect the environment.
Key benefits
- Modular design and easy repair
- Composites’ sustainability in leisure industry
- Highly customized
- Lightweighted, durable and greener
- Fashionable travel