Recycling / Circular Economy
The world’s first 100% “fiber-to-fiber” biorecycled clothing unveiled by multi-brand consortium
The collective achievement marks an important milestone for the consortium’s ultimate aim of demonstrating fiber-to-fiber closed loop using CARBIOS’ biorecycling process at an industrial scale, and marks an important step forward for the textile industry’s shift towards a circular economy.

No ordinary t-shirt…
A plain, white T-shirt was a deliberate choice to showcase the technological achievement that made its production possible from mixed and colored textile waste. By using CARBIOS’ biorecycling technology, polyester is broken down using enzymes into its fundamental building blocks which are reformed to produce biorecycled polyester whose quality is on par with oil-based virgin polyester. Petroleum can now be replaced by textile waste as a raw material to produce polyester textiles, that will in turn become raw materials again, thus fueling a circular economy, with the added benefit of a lower carbon footprint and avoidance of landfill or incineration.
No ordinary journey…
The t-shirt’s production began with all consortium members (On, Patagonia, PUMA, PVH Corp. and Salomon) supplying rolls and production cutting scraps to CARBIOS in Clermont-Ferrand, France. This textile waste consisted of some mixed blends with cotton or elastane, as well as various treatments (such as durable water repellent) and dyes which render them complex to recycle using conventional methods. The collected waste was deconstructed into its original monomers, PTA[1] and MEG[2], using CARBIOS’ biorecycling technology at its pilot facility. The resulting monomers were then repolymerized, spun into yarn and woven into new fabric by external partners, demonstrating the seamless integration into existing manufacturing processes. The resulting sports t-shirt made from 100% textile waste meets the quality standards and sustainability objectives of the apparel brands present in the “fiber-to-fiber” consortium.
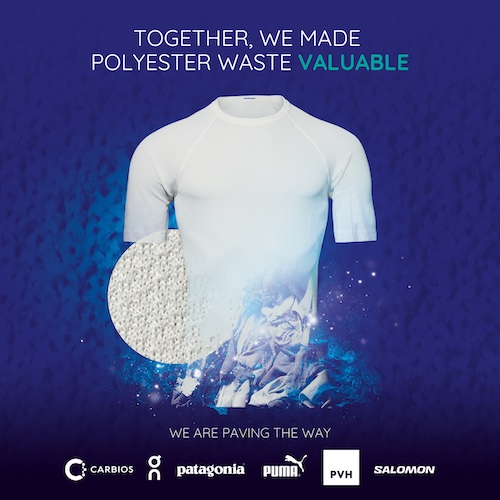
CARBIOS’ demonstration plant in Clermont-Ferrand, France, has been up and running since 2021, and its first commercial plant, the world’s first industrial-scale enzymatic PET recycling plant, is currently under construction in Longlaville, France. In addition, CARBIOS recently announced several letters of intent with PET producers in Asia and Europe, confirming global interest in its biorecycling technology and advancing the international roll-out of its licensing model.
"It may look like an ordinary t-shirt, but make no mistake, the technology behind it is extraordinary! To achieve “fiber-to-fiber” recycling is a technological feat. CARBIOS couldn’t have done it alone, so thanks to the collaboration with our consortium partners, we have overcome many technical hurdles together to produce the world’s first enzymatically recycled t-shirt made entirely from biorecycled fibers", stated CARBIOS CEO Emmanuel Ladent.
Begüm Kürkçü, Director of Sustainabililty, On, said:"We know that fiber-to-fiber recycling is a crucial step to drive our industry towards circularity, which is why we have dedicated energy and investment to researching this area. Achieving the proof-of-concept and creating the first T-shirt made out of 100% biorecycled fibers is an important milestone. Our engagement with CARBIOS and the other consortium members is an important step towards enabling the industry to game-changing circular technologies at scale."
"PUMA’s wish is to have 100% of our polyester coming from textile waste. Today’s announcement is an important milestone towards achieving this and making our industry more circular. We now need to work together to make sure we can scale up this technology to make the largest possible impact. We’re excited to be part of this breakthrough and setting new standards for fiber-to-fiber recycling", said Anne-Laure Descours, Chief Sourcing Officer at PUMA.
Guillaume Meyzenq, Chief Product Officer Softgoods, Salomon, said: "This T-shirt is the first tangible result of our ‘fiber to fiber’ consortium with CARBIOS, overcoming textile challenges to create a garment from enzymatically recycled waste with the same quality as virgin fibers. It builds on Salomon’s commitment to material circularity, following Index - the first recyclable running shoe, and highlights our dedication to reducing factory waste and our engagement to reduce by 30% our carbon footprint by 2030. This project, in collaboration with footwear and apparel Brand partners, reflects our shared leadership and vision for a more sustainable footwear and textile industry."
[1] Purified Terephthalic Acid
[2] Monoethylene Glycol