Composites
Composites Innovation on stage at the 9th JEC Asia International Composites Event Suntec Center, Singapore – November 15-17, 2016
Announcing the JEC Innovation Awards 2016 – Singapore winners
With 11 prizes and 19 involved companies, the JEC Asia 2016 Innovation Awards reward excellence in the use of composite materials throughout the whole value chain. From Raw Materials to Design and Manufacturing, to industrial applications in widespread fields such as Automotive, Aeronautics, Construction and Oil & Gas and finally covering Non-destructive Testing and Recycling, this year’s projects offer a wide variety of innovation. The Asian-Pacific region is becoming increasingly dynamic and competitive with light-weighting once again finding itself at the center of many innovations, and thermoplastics playing an important part in reaching that goal.
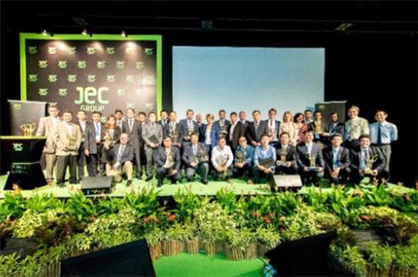
Pic: JEC Innovation Awards in Singapore
First ever Startup Competition on JEC Asia
“For the first time in Asia we wanted to create convergence between actual market needs, industrial processes and innovative ideas through this new competition that will highlight the potential of promising startups in the industry. We are thrilled to partner with xC Consultants for this new competition”, states Christian Strassburger, JEC Asia Director. A selection of startups will have a physical presence on a startup village on JEC Asia 2016 during the 3 days of the event and will be able to pitch their project in front of a jury of experts and network with composites professionals onsite.
6 conferences to cover Composites Developments and End-User markets
JEC Asia will also be the stage where more than 35 speakers will present papers about:
- Carbon Fiber in Mass Production Vehicles
- Software for Advanced Composite Design and Manufacturing
- Easy Design Tools for Composite Structures
- Testing and Life Cycle
- Advances and Challenges in the Aeronautics Industry
- Market Drivers in Off-shore Activities: Energy, Oil & Gas
More information: www.jec-asia.events
11 CHAMPIONS OF COMPOSITES MATERIALS RECEIVING A JEC INNOVATION AWARD
Category: RAW MATERIALS
Winners: National University of Singapore (SG)
Partner: University of Cambridge (UK)
Name of Product or Process: Advanced Carbon Nanotube Fiber Composites from Aerogel Techniques
Description:
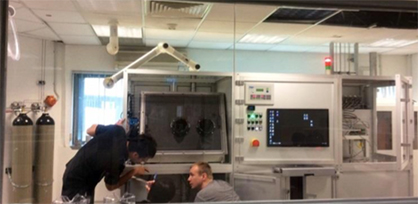
Another advantage of this method is the use of protective layers to prevent damage in the CNT fibre/film structures during the densification process. After combining with epoxy infiltration, the treated fibres exhibit an impressive increase of 13.5 times in strength and more than 63 times in stiffness, the highest improvement factors reported in literature so far. CNT fibres possess excellent mechanical properties that are significantly better than those of CNT fibres post-treated with other methods. They also present high electrical properties, thus showing great potential to replace convention metal wires. In addition, CNT fibres have excellent knot strength performance and high thermal properties.
This project also includes a direct and scalable aerogel method that makes it possible to fabricate self- supporting CNT aerogels at higher deposition rates. The whole fabrication process takes only about 1-2 hours and can produce metre-long CNT aerogels continuously without freeze drying and supercritical drying processes. The undeniable advantages of the established process also include its precise control of the amount of impurities and the morphology of the CNT aerogel.
Category: DESIGN
Winner: Revology (NZ)
Partner: D2 Design & Development (AU)
Name of Product or Process: Bistrot
Chair: 100% Organic Composite Materials and Biobased Resins
Description:
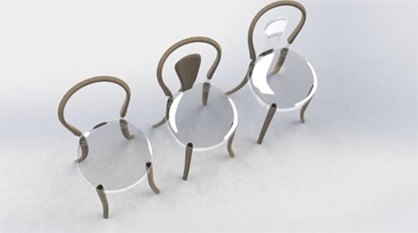
Revology has reinvented the bistrot chair, 100% made of organic composite materials and bio-based resins. All the structural parts are made ofthermoplastic braids reinforced with flax fibre, using the RocTool process to reduce the production cycle time. All the transparent parts are made with bio-based materials. The Revology chair will be one of the lightest chairs in the world, and indestructible. Revology chose flax composite materials not only for their mechanical properties, but also to highlight the natural beauty of this design chair. The launch involved 18 months of development to enable presenting the Revology concept chair for the first time in March 2016, at JEC World. The next steps include Kickstarter and Indiegogo campaigns to presell the products and organize the mass production and industrialization in three factories (Europe, Asia and USA), in order to deliver the chairs worldwide within five business days. There are about 300 million bistrot chairs to replace. The Revology chair is one of the lightest chairs in the world. What’s more, it is indestructible and uses natural and sustainable materials.
Category: MANUFACTURING
Winner: Techni-Modul Engineering (France)
Partner: Pascal Institute (France)
Name of Product or Process: Robotized Cell for the Creation of Dry Fibre Preforms Without Operator
Description:
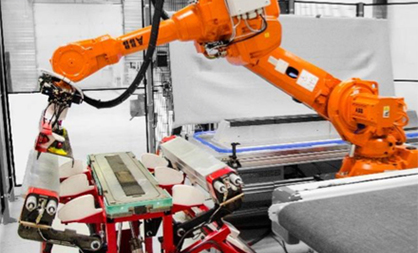
To meet composite manufacturers’ need for more automation, Techni-Modul Engineering (TME) developed a robotized cell that can create a preform made out of dry fibre materials without operator intervention throughout the entire cycle. Dry fibres were chosen to enable out-of-autoclave solutions. TME designed and manufactured its first RTM mould in 1988 and rapidly specialized in this manufacturing process. The company conducted many RTM projects and identified the need to automate this process for various reasons. They also identified the demand for robotized lay-up of pre-impregnated materials. The innovation is related to the improvement of the composite part manufacturing process. The added value comes from the integration of new functions, including intelligent automation and pick, place and fold in a 3D shape. The preform robot cell was developed for several reasons. While the aerospace and automotive industries are struggling to meet the production rates required for the current backlog, the robot makes it possible to reduce the cycle time by a factor of 2, 3 or 4, depending on part geometries and the manual layup process previously used. It also ensures quality and repeatability by eliminating all potential errors. The robot is programmed to pick, place and fold the plies accurately at the right place, whereas the manual process involves as many chances for human errors as the number of plies to lay up. Since this solution can replace the human operator, it also avoids potentially harmful repetitive movements.
Category: WIND ENERGY
Winner: Aditya Birla Chemicals (Thailand)
Name of Product or Process: Instant Thixotropic Structural Epoxy Adhesive
Description:
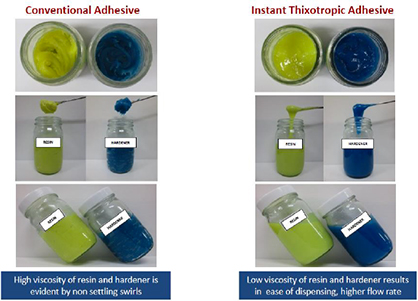
The thixotropic nature of the components makes it challenging to process these materials and leads to air entrapment and voids during application, which in turn leads to defects and bonding failures after curing of the adhesive mass.
The innovation concerns the development of a two-component epoxy adhesive with low-viscosity flowable components that, on mixing, develop instant thixotropy and provide superior sagging resistance compared to the currently used materials. This innovative product is also designed to provide longer curing times and faster strength development, together with similar mechanical properties such as bonding strength, stiffness, critical stress intensity factor, critical strain energy release rate and fatigue performance.
While the product was designed with rotor blade requirements in mind, it can also be used in other demanding composite bonding applications. Considering the growth rate of wind energy in terms of installed capacity year on year and the growing need for high-performance adhesives in other segments, the product is estimated to have a potential of over 20,000 tons per annum. The product can also cater to the needs of industrial and infrastructure applications, since it addresses the limitations of mixing high-viscosity thixotropic components.
Category: AUTOMOTIVE
Winner: Daimler AG (Germany)
Partners: Multimatic (CA), Carbon Nexus (Australia), IFB Stuttgart (Germany)
Name of Product or Process: Carbon-Fibre-Reinforced Plastic Composite Rear Wall of Mercedes-Benz S-Class AMG
Description:
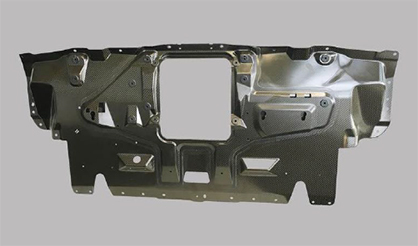
Similar examples of structural panel components currently exist in low-volume production (e.g. for the BMW i3 & i8 or Audi R8) with the ability to expand existing industrialized processes (RTM) to higher production volumes having shown only limited economic viability. The key to high-volume CFRP manufacturing was to split the conventionally sequential in-mould process steps of injection-infiltration-cure into parallel press compression moulding process steps of impregnation and curing.To achieve an efficient CFRP design, the structure was optimized using advanced engineering tools to attain an aggressive mass reduction of 50% versus the existing aluminium-plastic hybrid solution.
From a design aspect, the tangible end-user product benefit is a reduced component mass with equal performance that contributes to lower fuel consumption and, of particular importance for Mercedes-Benz AMG performance cars, improved vehicle dynamics. From a manufacturing aspect, the SPP process opens up new opportunities to extend CFRP component performance benefits from lower to higher production volume vehicle applications (e.g. 100,000 vehicles per annum).
Category: AERONAUTICS
Winner: National Aerospace Laboratories (India)
Name of Product or Process: Development of a 14 Seater Civil Aircraft: ‘SARAS', Integrating The Fuselage Bulkhead With The Composite Dome
Description:
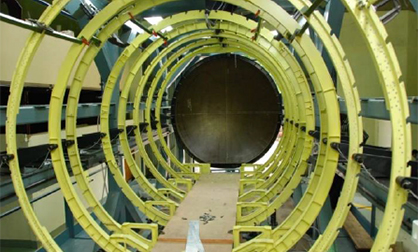
Weight savings and performance can be maximized using co-curing technology, resulting in significant reductions of fabrication cycle time, cost and weight. Co-cured structures have fewer fasteners, resulting in shorter assembly cycle times and reduced sealing issues.
The pressure bulkhead separates the pressurized region of the fuselage from the unpressurized region. Ideally, a dome (shell) type of construction is more efficient in transferring pressure loads by membrane action, which is reacted as in-plane stresses in the composite dome. This property of the shell makes it more economical than a flat plate under the same loading conditions. Composite domes have been used for rear pressure bulkheads in recent aircraft programmes such as the A380, A350, B787, etc.
The rear pressure bulkhead consists of the fuselage frame, which is a ring of 1.8m diameter having an I-section co-cured with a dome-shaped skin. Gussets are provided on either side of web to connect longerons (stringers) on either side of the bulkhead. The entire part is conceived such that all three regions are integrally made into one part, taking the design/stress requirements along with manufacturing feasibility into consideration. The bulkhead is manufactured using a Hexcel prepreg and an autoclave moulding technique.
Category: RAILWAY Winner: Miyagi Kasei Co., Ltd. (Japan)
Partner: Research Institute for Chemical Process Technology (AIST) (Japan)
Name of Product or Process: EXVIEW: An Innovative Transparent Composite For Trains With a New Flame Retardant Concept
Description:
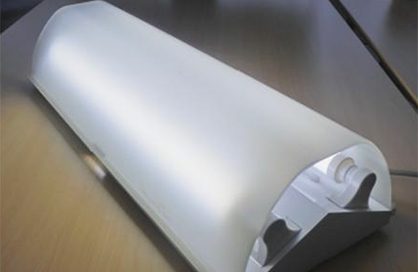
Developed by AIST, the Claist transparent clay film is 3 to 200μm thick and possesses heat resistance and high gas-barrier properties. It was already used for various CFRP gas-barrier tanks (hydrogen tanks for automobile fuel and oxygen tanks for rocket fuel).
Inspired by this application, AIST conducted tests to apply these gas-barrier properties for flame retardant performance. The composition combines the flexible transparent clay film with advanced transparent epoxy composites.
First, the transparent epoxy composite was moulded by infusion (8 layers of glass fibre, clear epoxy resin and crystalline silica). Then it was cured in an oven and the clay paste was coated using a spray process. As a result, the moulded transparent epoxy composite possesses higher flame retardant properties than standard flame-retardant composites and high enough strength to be taken into consideration for train lighting covers.
This innovative technology of clay film and transparent epoxy composites was developed and adopted for the lighting covers of the Japanese railways. The partners received the authorization of JRMA in 2014 and named this transparent epoxy composite EXVIEW®.
Category: CONSTRUCTION
Winners: Republic Polytechnic (Singapore), ETH Zürich/Singapore-ETH Centre (Singapore)
Name of Product or Process: Maximizing Bonding Between Sustainable Bamboo Composite and Concrete
Description:
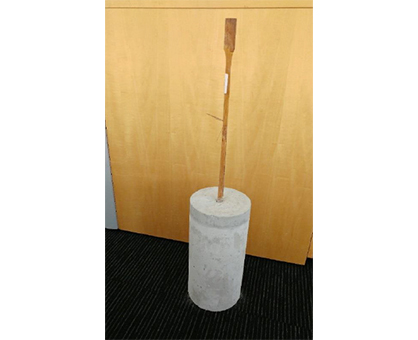
However, one of the limitations of current FRP rebars using carbon fibre-reinforced polymer (CFRP) or glass fibre-reinforced polymer (GFRP) is their high cost and non-sustainable sources. As a result, there is a demand for cheaper FRP made of sustainable materials that retain a high strength-to-weight ratio and good corrosion resistance properties. In recent years, bamboo FRP has been preferred. Bamboo is a fast-growing and sustainable raw material that grows in abundance in the tropical belt, making it cheaper than other materials.
Similar to other FRP, the adhesive strength between bamboo FRP and concrete is one of the limiting factors that prevent the use of bamboo FRP in rebars.
Therefore, this project aims to develop an adhesive coating to chemically enhance the bonding strength between bamboo FRP and concrete. It will then be possible to use bamboo FRP for rebars while achieving the required bonding strength. Converting bamboo into a bamboo composite improves the water resistivity of the material and opens great prospects for use in structural applications such as concrete reinforcing bars.
Press contacts: JEC GROUP - Thierry-Alain TRUONG - mail: truong@jeccomposites.com APOCOPE - Dorothée DAVID – Marion RISCH +33 (0)1 45 78 87 37 / mail: media@agenceapocope.com
Category: OIL & GAS Winner: Technip (France)
Name of Product or Process: Durable and Light-weight Flexible Riser Reinforced with Carbon Fiber Composites for Extreme Environments of Offshore Oil and Gas Fields
Description:
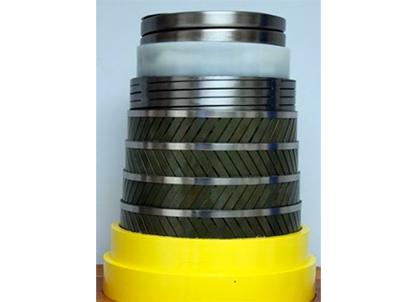
The material is made of a UD material reinforced with high-strength transverse carbon fibre combined with an epoxy resin (potentially thermoplastic).The material can be pultruded into continuous lengths up to 5000 metres without splices. Its service life is 20 to 30 years under harsh environments that involve fatigue corrosion, water, CO2, H2S, CH4 up to 100°C, etc.
In this project, the use of composite materials results in several advantages. Most notably, the weight of pipelines for oil and gas exploration and production in ultra-deep water is drastically reduced. Pipe service life is also increased, a major step towards innovative designs for offshore flexible pipes.
The main application sectors are the deep and ultra-deep water oil and gas markets.
The main benefits of this project are:- reasonable size of the required installations and equipment, as well as significantly shorter installation times;- improved corrosion resistance and longer service life of the pipeline; - no need for the buoyancy modules currently used with conventional steel pipelines; - drastically reduced overall costs without affecting the safety of the whole system.
Category: NON-DESTRUCTIVE TESTING
Winner: SURAGUS GmbH (Germany)
Name of Product or Process: Isotropy and Integrity Testing Solution for Recycled Carbon Fibres
Description:
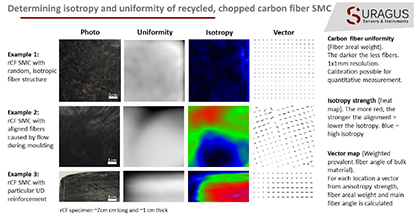
The non-contact isotropy testing system enables effective re-manufacturing and efficient re-use of rCF, rCFRP and CF-SMC due to novel sensors that non-destructively measure the key properties for mechanical use: main fibre directions (an/isotropy) and fibre distribution.
Category: RECYCLING
Winner: Toho Tenax Europe GmbH (Germany)
Partner: Sintex NP Group (France)
Name of Product or Process: Closing the Loop for Tenax® Thermoplastic Composites
Description:
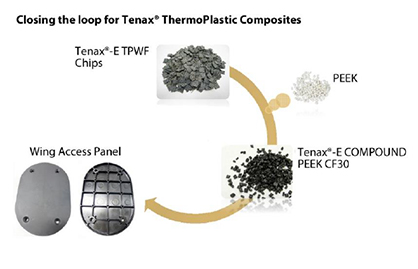
The Tenax®-E COMPOUND PEEK CF30 is a “green“ composite innovation based on recycled by-products from Tenax®-E TPCL PEEK-HTA40 (Carbon Fiber /PolyEtherEtherKetone) production and customer scrap.
The material reinforced combination of recycled 30% carbon fiber and recycled semi crystalline PEEK, offers high performance in strength and stiffness for injection moulding applications.
This material is almost identical to virgin material at much lower costs. Toho Tenax’s intention was to develop a closed-loop concept for their thermoplastic materials, reconverting the exceptional properties of this high-performance material combination through the use of different reprocessing techniques to turn the materials back into serial non-structural aircraft OEM parts.
The Sintex NP Group was as partner responsible for the part manufacturing process based on Tenax®-E COMPOUND PEEK CF30 and the assessment of material processability compared to today’s virgin material standards within their production processes.