Composites
BASF shows latest innovations at JEC in Paris
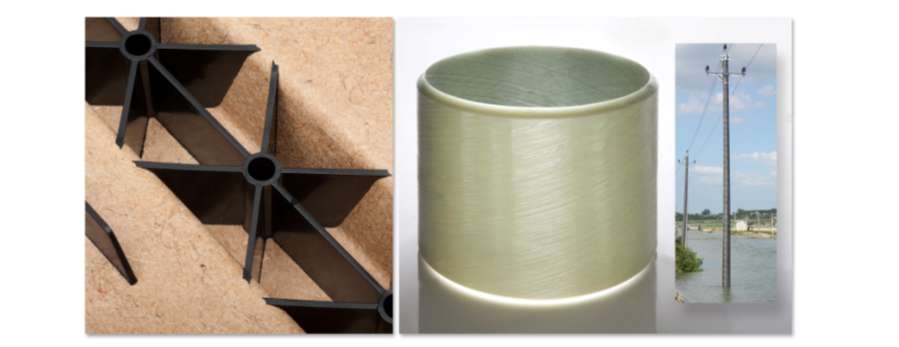
- Strong and ultra-lightweight utility poles made with Elastolit®
- Cost efficient Acrodur® Power 2750 X enables higher share of natural fibers
- Demonstrator parts for future automotive technologies
Infrastructure
Ultra-light utility poles made of Elastolit® withstand extreme loads
BASF presents a new type of very strong and wind resistant utility pole made with BASF’s polyurethane system Elastolit®. The technology is already proven in China and now available in Europe as well.
These poles based on a filament winding technology are much lighter and at least 2.5 times more wind-resistant than the commonly used concrete utility poles for medium voltage grids. Due to their very light weight – a 12 meter composite pole weighs only 250 kg – they are easy to install and no heavy equipment is needed when erecting the poles. The bending strength of the new type is at least 2.5 times higher compared to concrete poles which allows long distances between the single poles of up to 120 meters.
The utility poles already proved their superior wind resistance during last year’s typhoon “Rammasun” in China. The storm destroyed 70.000 concrete and metal utility poles while none of the polyurethane based utility poles were affected and are still in service.
Automotive
Examples of various composite materials for high-performance composite parts
BASF is showing examples of new uses for thermosets and thermoplastics for automotive lightweight design. These achieve further reductions in component weight and CO2 emissions. The structural component exhibited was made by wet pressing with an Elastolit® RTM polyurethane system (RTM: resin transfer molding) in an experimental mold. The Elastolit® used here features fast curing, very good fiber impregantion, and excellent fatigue properties.
For MAI Qfast, a project involving Audi, BMW, the Fraunhofer Institute for Chemical Technology and KraussMaffei in the MAI Carbon Cluster, a part of a generic vehicle structure has been optimized and manufactured using various composite production processes. Two demonstrator parts can be seen on the BASF stand: the RTM variant of a generic floor structure produced with the epoxy system Baxxodur®; and a thermoplastic variant with load-path-optimized reinforcement made of UltratapeTM from BASF – a carbon-fiber-based system using unidirectional tape. In both cases optimization using BASF’s Ultrasim® simulation tool was the key to achieving compliance with the component specification together with a significant weight saving. So while BASF’s Ultrasim® was already a valuable design tool for the continuous-fiber-reinforced thermoplastic composite system UltracomTM, the simulation toolbox has now also been extended to reactive processes like RTM.
Novel Acrodur® binder helps produce cost-efficient automotive lightweight composites with integrated functions and a higher share of natural fibers
BASF is launching a new binder – Acrodur® Power 2750 X. The product is designed for the production of natural fiber composites for automotive lightweight applications such as interior car door panels or shelves. As a low-emission alternative to formaldehyde-based reactive resins, Acrodur Power 2750 X gives natural fiber composites high mechanical stability. At the same time, the product offers thermoplastic processability and, unlike traditional thermoplastic binders based on polypropylene, it allows the use of up to 75 percent natural fibers in lightweight components. In addition, the molding of natural fiber pre-preg and the injection of functional and structural elements with BASF’s plastic Ultramid® can be carried out in one single step.
At the JEC Composites Show BASF is going to present a functionalized natural fiber lightweight composite based on Acrodur Power 2750 X.
The low-emission Acrodur binders are used to reinforce natural fiber composites before these can be processed into molded components. They are also used for the production of high quality lightweight applications in the furniture and automotive industry.
Recently, the Acrodur 950 L binder received the innovation award from JEC, the international industry network for composites. The French automotive supplier Faurecia had used the BASF product to develop a light composite with great mechanical stability, to reinforce long flax fibers.
Wind power
Solutions for the wind industry with Baxxodur® epoxy resin systems and Kerdyn® PET (polyethylene terephthalate) structural foams
Another highlight of the show will be BASF’s range of solutions for the wind industry encompassing Baxxodur® epoxy resin systems and Kerdyn® PET (polyethylene terephthalate) structural foams, which address the trend toward larger parts and comprise a variety of production processes. The Baxxodur® system offerings for composites are based on BASF’s comprehensive portfolio of amine-based curing agents that are unmatched in the industry. Kerdyn® PET (polyethylene terephthalate) structural foam unites good mechanical properties with wide process compatibility. Thanks to its high temperature and chemical resistance, it adds stability to rotor blades.
Related News
Performance Chemicals for Textiles