Industry 4.0
Softwear Automation introduces next generation LOWRY SEWBOT
Since the beginning, Software Automation has worked to make the SEWBOT® a platform for industrial sewing automation. While sewing is at the center of that challenge, they have been successful because of their ability to master material handling like picking, placing, moving, stacking, lifting, holding, labeling, welding and more. As it turns out, automated sewing may be the easiest part of sewing automation. What makes the LOWRY® special is the sheer number of products, operations and styles that one system can handle without an operator and without it being retooled, reprogrammed or re-configured.
"The major advancements in this next generation SEWBOT® have come from the improved vision technology, which has put them light years ahead in flexible production automation from the previous releases", stated the company. There is no question that textiles present challenges unique to industrial automation. The needs as consumers to have textile products that are light, breathable, stretchable and fashionable creates an ever changing landscape of complexity. Unlike hardware intensive solutions, vision technology allows the SEWBOT® to adapt to handling the unique pieces of a material good.
The vision technology recognizes material shape, size, fabric, style and sewing requirements in order to calculate and complete full automation of a product. This means minimal retooling is required any time a change or an upgrade is made to the style or appearance of the product – reducing cost, down time and labor. The machine vision also allows users to see material distortion in real time and to dynamically adjust to correct that distortion without any programming, resulting in high quality produced goods each and every time.
The LOWRY® leverages all of our advancements made in vision technology allowing for efficient production of sewn goods. Made of durable industrial-grade steel, the base frame has been upgraded to provide a machine that can run 24/7 and is able to withstand the test of time. Whether from potential damage from giant forklifts or wear and tear from micro particles, it is truly built to last on the factory floor. The LOWRY® can also undertake simultaneous automated operations, like automated loading, flaw detection, sewing, seaming, cutting, labeling and re-stacking all through a simple control touch panel. One single machine operator is able to control up to six LOWRY®s at once, resulting in a significantly higher production scale.
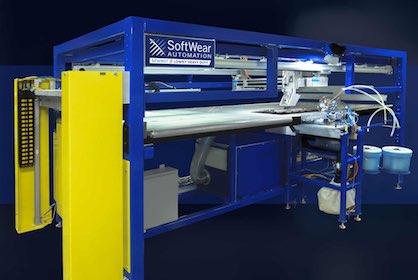
The LOWRY® enables companies to achieve on-demand production automation with its modular design and interchangeable components. "We understand that every sewn good is constructed differently, which is why the LOWRY® has flexible configurations to support a variety of goods", the company says. Each machine module can be removed, replaced, upgraded, repurposed and repaired depending on your unique product specifications. For each product listed below, the LOWRY® has a product specific configuration available to enable full automation.
It is built to serve a number of different industries, supporting both local and global supply chains and is available now, worldwide.
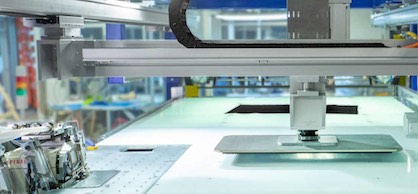